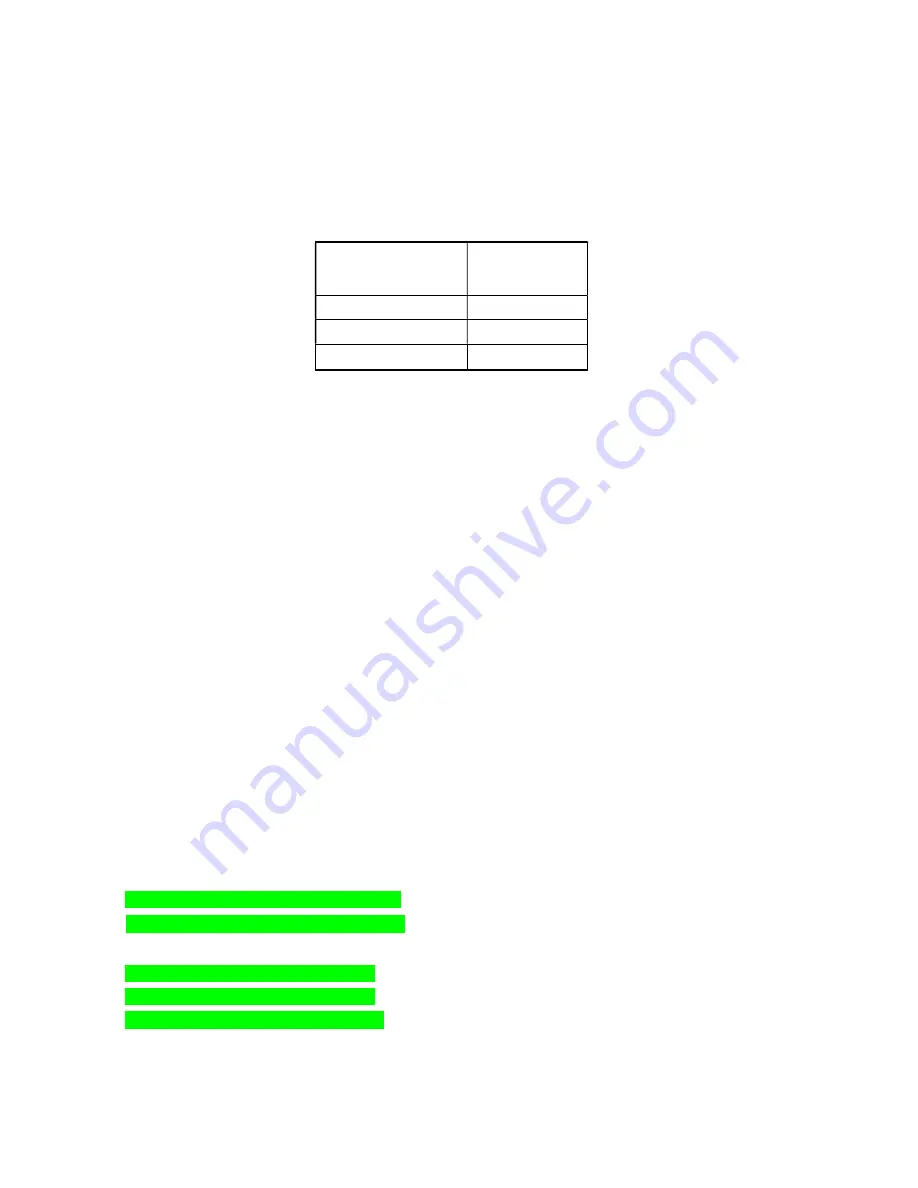
4000 Series
Page
23
of
41
3460006-17_serial series 5000000
Profile Heading:
Under Profile, there are 4 Profile sections (Profile 1 Step, Profile 2 Step, Profile 3 Step, and Profile 4 Step). The
steps listed under these sub-sections are a continuous list of 40 Steps that can each be individually configured
into various step types to accomplish the desired profile temperature parameters. (Steps 38, 39, and 40 are
reserved for the defrost function, and should not be changed from factory default. More information on the defrost
is listed below)
The following table outlines the starting step of each of the 3 profiles selectable with the MODE selection Switch.
MODE Switch
Positon
Profile
Start
Step
Profile 1
Step 1
Profile 2
Step 11
Profile 3
Step 21
There is a total of 10 steps available for Profile 1 (Step 1 – Step 10), and Profile 2 (Step 11 – Step 20). Profile 3
has a larger number of steps available (Step 21 – Step 37) if a desired temperature profile will require more than
10 steps to be programmed successfully.
(If more than 10 steps are needed for Profile 1 and Profile 2, the start
steps of each of the 3 Profiles can be changed to different step numbers. Please contact Farrar Scientific for aid
in changing the appropriate settings).
A Temperature profile is made by configuring sequential steps that either change the temperature set point of the
air in the chamber or maintain a previously defined set point. Each profile starts at that Profile’s start step and
ends with a step type that either turns the unit off, or holds a specific temperature until a user interacts with the
unit to stop operation.
The available step types that can be used with the 4000 series unit, and example profiles, are listed below. Each
step type has individual parameters that must be set correctly to ensure proper operation of the 4000 series unit.
When the Step Type is changed on each individual step, only the parameters that can be changed will be in
BOLD
, all other parameters will be greyed, and have no effect on that step type. The parameters that need to be
set for each set type are highlighted in green below.
Available Step Types:
Time Step
Used to change the set point of the cabinet over the specified time. This is the step that can be used to
slowly change the temperature of the cabinet at a controlled rate, or be used to change the temperature
of the cabinet as fast as possible by using a short timespan setting. The set point will change from the
current temperature of the cabinet, to the target set point over the specified time.
See below for more specifics on this step type and the format that matches what will be seen in EZ-
Zone.
Step Type
Time
Target Set Point Loop 1
-80ºC
Set point for this step type
Target Set Point Loop 2
-18ºC
Hours
0
Time settings for the time the set point
Minutes
0
will change over
Seconds
10
Rate
0ºC
Wait for Process Instance
1