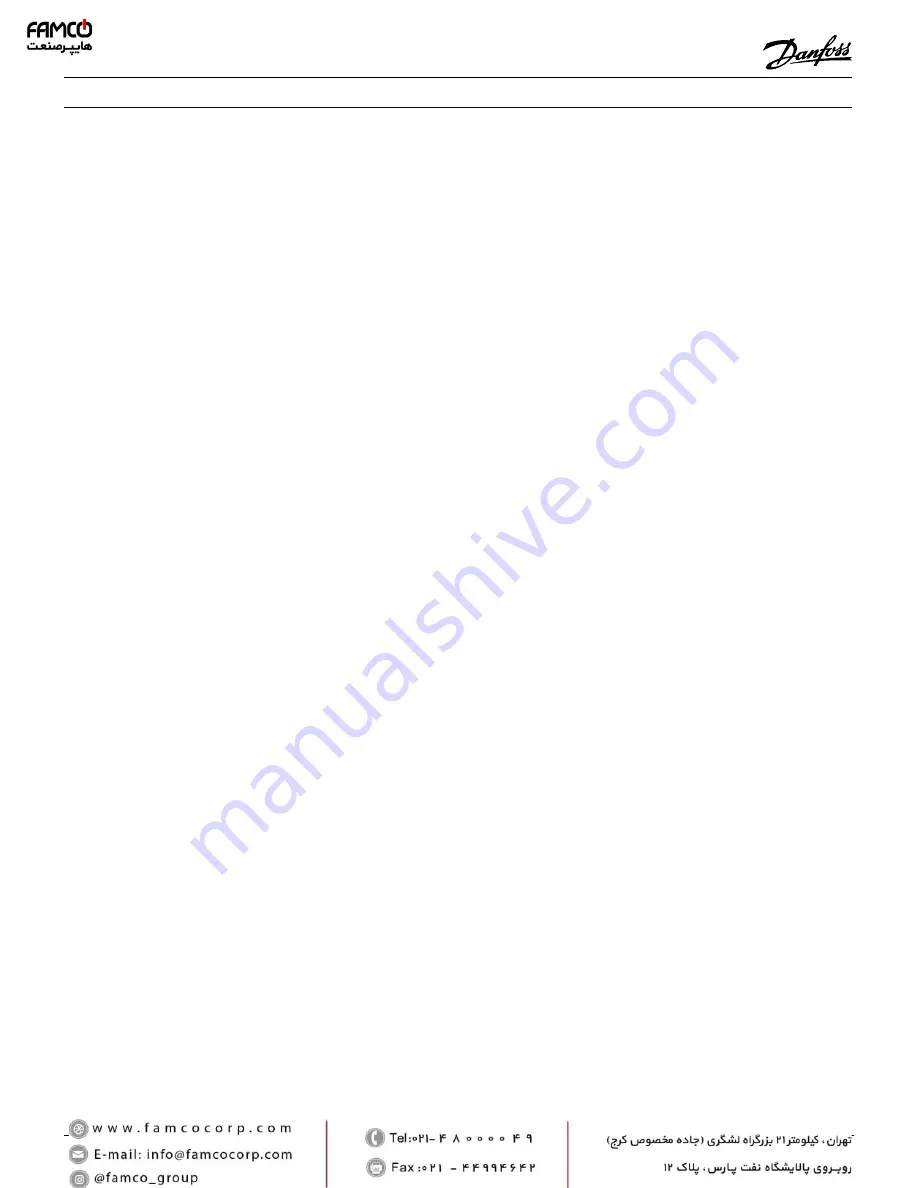
INSTALLATION AND SERVICE
Vacuum pull-down
moisture removal
Start-up
Refrigerant charging
flammable mixture. Never use CFC or
HCFC refrigerants for leak detection in
HFC systems.
Note 1:
Leak detection with refrigerant
may not be allowed in some countries.
Check local regulations.
Note 2:
Leak detecting additives shall
not be used as they may affect the
lubricant properties.
Warranty may be voided if leak detec-
ting additives have been used.
Moisture interferes with proper functio-
ning of compressors and refrigeration
systems.
Air and moisture reduce service life, in-
crease condensing pressure, and cause
excessively high discharge tempera-
tures, that can destroy the lubricating
properties of the oil. Air and moisture
also increase the risk of acid formation,
giving rise to copper plating. All these
phenomena can cause mechanical and
electrical compressor failure.
To eliminate these factors, a vacuum
pull-down according to the procedure
given below is recommended.
1.
Whenever possible (if valves are pre-
sent) the compressor must be kept iso-
lated from the system.
2.
After leak detection, the system
must be pulled down under a vacuum
of 500 microns. A two stage vacuum
pump must be used, with a capacity
appropriate to the system volume. Use
connection lines with a large diameter
and connect them to the service valves
and (not to the Schräder connection) to
avoid too high pressure losses.
3.
When a vacuum level of 500 mi-
crons is reached, the system must be
isolated from the vacuum pump. Wait
30 minutes, during which the system
pressure should not rise. When the
pressure rapidly increases, the system is
not leak tight. Leak detection must be
repeated and the vacuum pull-down
procedure should be restarted from step
1. When the pressure slowly increases,
this indicates the presence of moisture.
In this case steps 2 and 3 should be re-
peated.
4.
Connect the compressor to the sys-
tem by opening the valves. Repeat
steps 2 and 3.
5.
Break the vacuum with nitrogen or
the final refrigerant.
6.
Repeat steps 2 and 3 on the total sys-
tem.
At commissioning, system moisture
content may be up to 100 ppm. During
operation the filter drier must reduce
this to a level < 20 ppm.
Warning :
Do not use a megohmmeter or apply
power to the compressor while it is un-
der vacuum, as this may cause motor
winding damage.
Never run the compressor under va-
cuum as it may cause compressor mo-
tor burn-out.
Before initial start-up, or after a prolon-
ged shut down period, energize the
crankcase heater (if fitted) 12 hours
prior to start-up, or turn on power for
single phase compressors with trickle
circuit.
Zeotropic and "near-azeotropic" refri-
gerant mixtures such as R-407C and
R-404A must always be charged in the
liquid phase. For the initial charge, the
compressor must not run and service
valves must be closed. Charge refrige-
rant as close as possible to the nominal
system charge before starting the com-
pressor. Then slowly add refrigerant in
the liquid phase, on the low pressure
side as far away as possible from the
running compressor.
The refrigerant charge quantity must
be suitable for both winter and summer
operation. Refer also to section "Protec-
tion against flooded starts and liquid
floodback" for information about refri-
gerant charge limits.
Warning:
when a liquid line solenoid
valve is used, the vacuum in the low
pressure side must be broken before
applying power to the system.