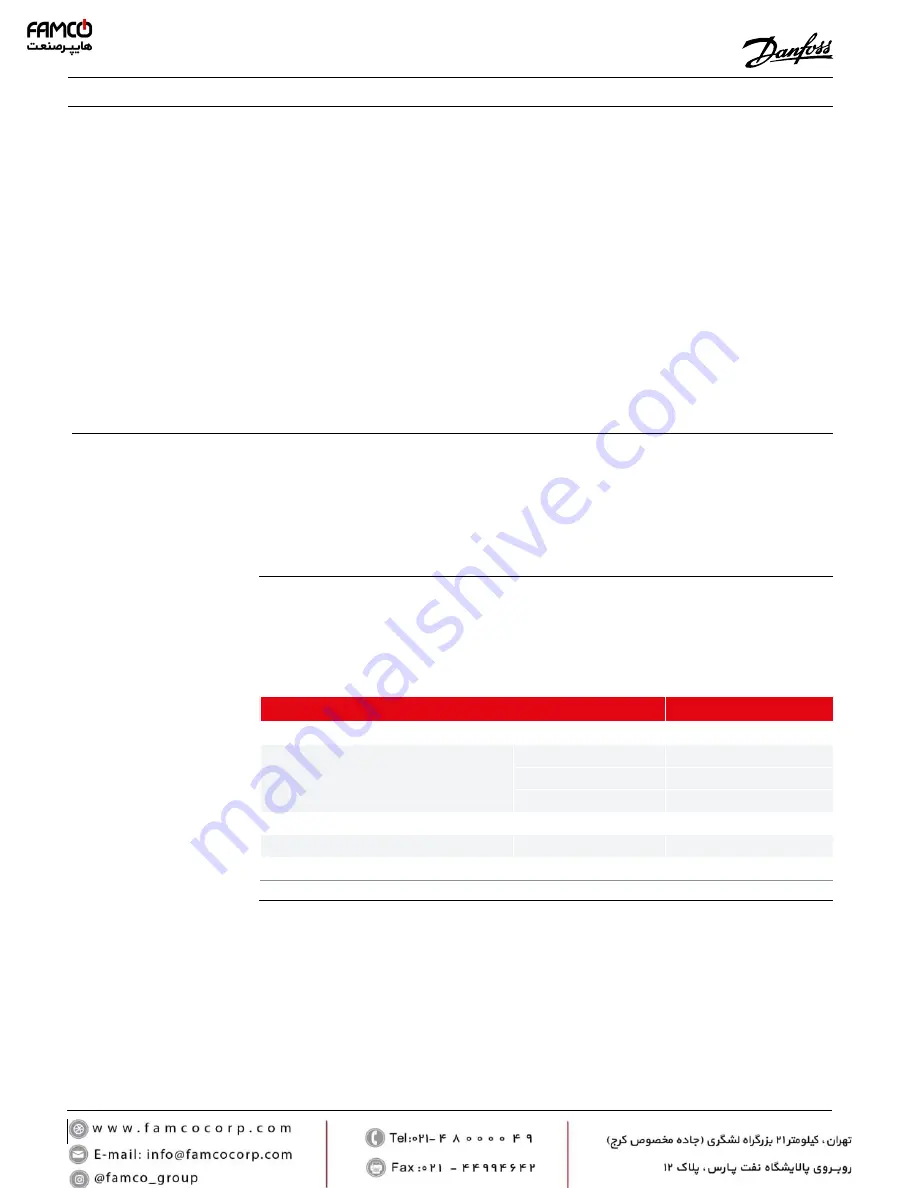
Application guidelines
30
FRCC.PC.004.A9.22
Installation and service
System cleanliness
System contamination is one of the main factors
affecting equipment reliability and compressor
service life.
Therefore it is important to ensure system
cleanliness when manufacturing a refrigeration
system. During the manufacturing process,
system contamination can be caused by:
• Brazing and welding oxides
• Filings and particles from removing burrs from
pipe-work
• Brazing flux
• Moisture and air.
Only use clean and dehydrated refrigeration
grade copper tubes and silver alloy brazing
material. Clean all parts before brazing and
always purge nitrogen or CO
2
through the
pipes during brazing to prevent oxidation. If
flux is used, take every precaution to prevent
leakage into the piping. Do not drill holes (e.g.
for schräder valves) in parts of the installation
that are already completed, when filings and
burrs can not be removed. Carefully follow the
instructions below regarding brazing, mounting,
leak detection, pressure test and moisture
removal. All installation and service work shall
only be done by qualified personnel respecting
all procedures and using tools (charging systems,
tubes, vacuum pump, etc.) dedicated for the
refrigerant that will be used.
Compressor handling,
mounting and connection to
the system
Compressor mounting
Compressor handling
Compressor connection to the
system
Maneurop® MT and MTZ compressors are
provided with a lifting lug. This lug should
always be used to lift the compressor. Once the
compressor is installed, the compressor lifting
lug should never be used to lift the complete
installation.
Keep the compressor in an upright position
during handling.
Mount the compressor on a horizontal plane with
a maximum slope of 3 degrees. All compressors
are supplied with three or four rubber mounting
grommets, each complete with metal sleeves
and nuts and bolts. Refer to the section “Outline
drawings”.
These grommets largely attenuate the
compressor vibration transmitted to the base
frame. The compressor must always be mounted
with these grommets. Refer to the table below for
torque values.
New compressors have a protective nitrogen
holding charge. The suction and discharge caps
should only be removed just before connecting
the compressor to the installation to avoid air
and moisture entering the compressor.
Whenever possible the compressor must be
the last component to be integrated into the
system. It is advisable to braze the solder sleeves
or service valves to the pipework before the
compressor is mounted. When all brazing is
finished and when the total system is ready,
the compressor caps can be removed and the
compressor can be connected to the system with
a minimum exposure to ambient air.
If this procedure is not possible, the sleeves
or valves may be brazed to the pipes when
mounted on the compressor.
Designation
Recommended torque (lbf.ft)
Cable screw of T connector in electrical box
screw 10/32 - UNF x 3
2
Rotolock valves and solder sleeves
1"
59
1"1/4
66
1"3/4
81
Mounting grommet bolts
1 - 2 - 4 cylinder
11
Oil sight glass
-
37
Oil equalization connection
1 - 2 - 4 cylinder
22