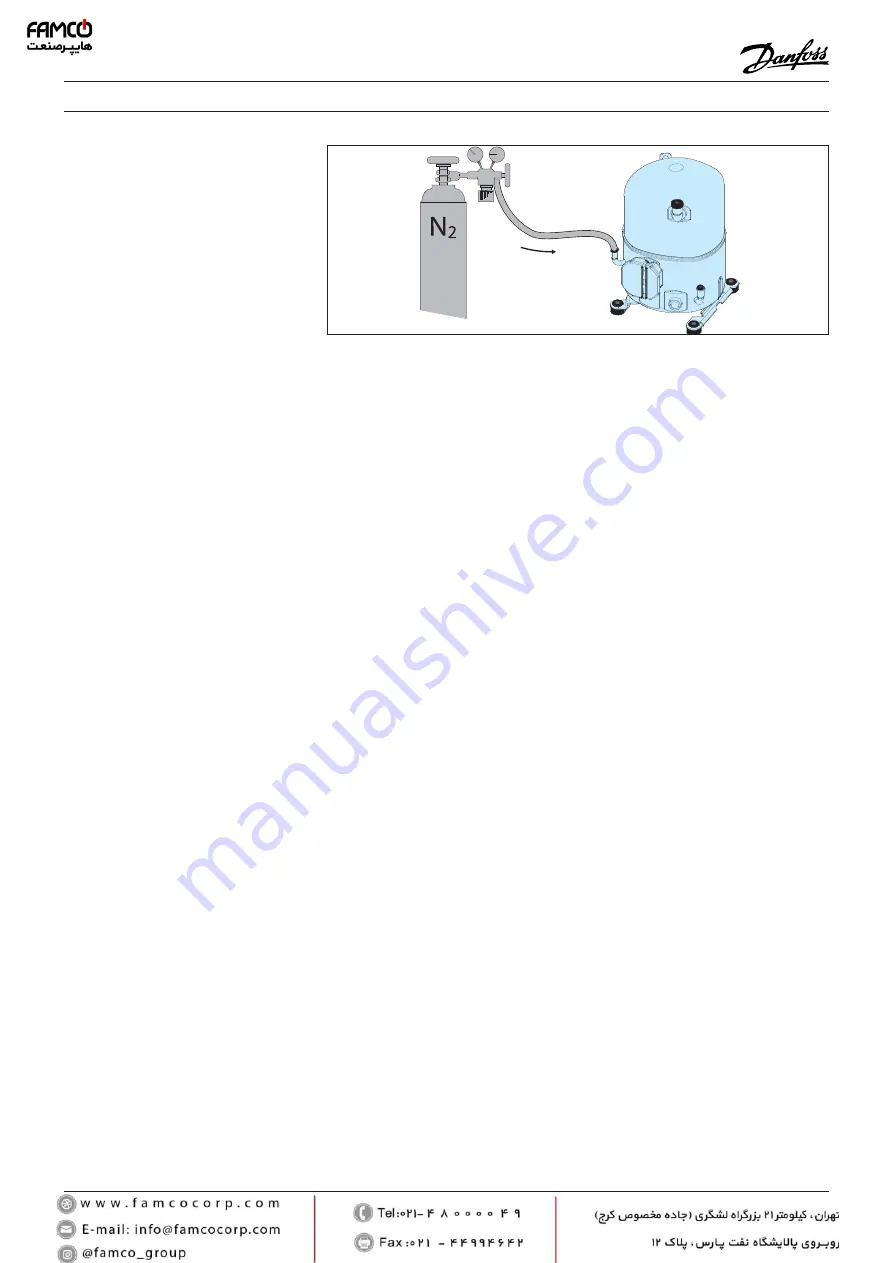
22
INSTALLATION AND SERVICE
System pressure test
Leak detection
It is recommended that an inert gas
such as nitrogen be used for pressure
testing. Always use the appropriate
pressure regulator with gas cylinders.
Any attempt to use a high pressure
gaz supply without a suitable pressure
regulator can lead to personal injury or
death as well as system damage. Dry
air may also be used but care should be
taken since it can form an infl ammable
mixture with the compressor oil. When
performing a system pressure test, the
maximum allowed pressure for the
diff erent components should not be
exceeded.
For Danfoss MPZ compressors the
maximum test pressure is 25 bar(g).
Perform a leak detection test on
the complete system by means
of electronic detector after circuit
pressurization with nitrogen and
R404A.
The low side test pressure must not
exceed 25 bar(g). Should a leak be
discovered, proceed with repair steps
and repeat the leak detection.
It is forbidden to use other gasses
such as oxygen, dry air or acetylene as
these gasses can form an infl ammable
mixture. Never use CFC or HCFC
refrigerants for leak detection of HFC
systems.
Note 1
: Leak detection with refrigerant
may not be allowed in some countries.
Check local regulations.
Note 2
: Leak detecting additives shall
not be used as they may aff ect the
lubricant properties.
Warranty may be voided if leak
detecting additives have been used.
Vacuum pull-down
moisture removal
Moisture obstructs the proper
functioning of the compressor and the
refrigeration system.
Air and moisture reduce service life
and increase condensing pressure,
and cause excessively high discharge
temperatures, which can destroy
the lubricating properties of the oil.
Air and moisture also increase the
risk of acid formation, giving rise to
copper plating. All these phenomena
can cause mechanical and electrical
compressor failure.
To eliminate these factors, a vacuum
pull-down according to the procedure
below is recommended:
1.
Whenever possible (if valves are
present) the compressor must be kept
isolated from the system.
2.
After the leak detection, the system
must be pulled-down under a vacuum
of 500 microns (0.67 mbar). A two
stage vacuum pump shall be used
with a capacity appropriate to the
system volume. It is recommended
to use connection lines with a large
diameter and to connect these to the
3/8" process tube connection.