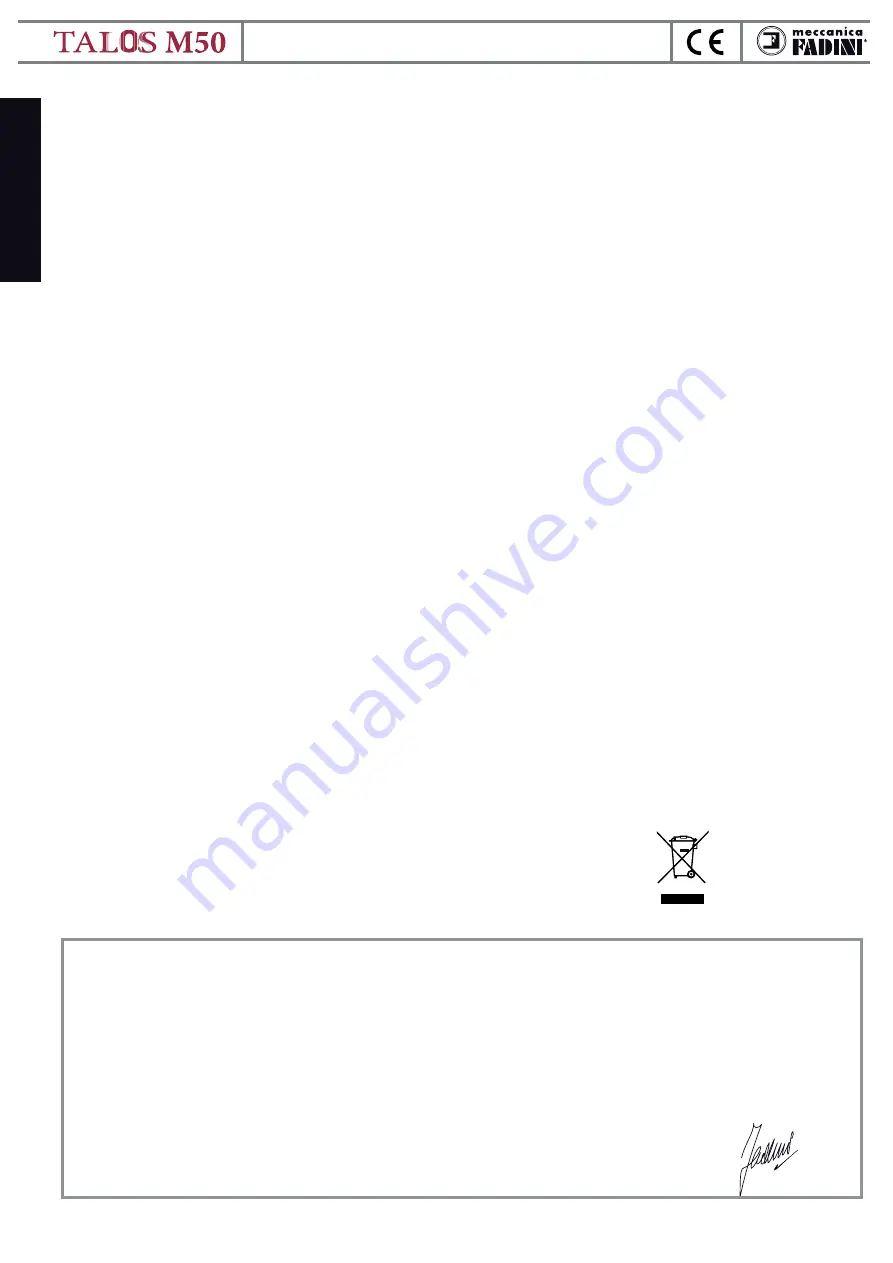
English
Anti-terrorism retractable oil-hydraulic bollard
GENERAL WARNINGS FOR PEOPLE SAFETY
THANK YOU
Thank you for purchasing a Fadini product.
Please read these instructions carefully before using this appliance.
The instructions contain important information which will help
you get the best out of the appliance and ensure safe and proper
installation, use and maintenance. Keep this manual in a
convenient place so that you can always refer to it for the safe and
proper use of the appliance.
INTRODUCTION
This operator is designed for a specific scope of applications as
indicated in this manual, including safety, control and signaling
accessories as minimum required with
Fadini
equipment.
□
Any
applications not explicitly included in this manual may cause
operation problems or damages to properties and people.
□
Meccanica Fadini snc is not liable for damages caused by the
incorrect use of the equipment, or for applications not included in
this manual or for malfunctioning resulting from the use of
materials or accessories not recommended by the manufacturer.
□
The manufacturer reserves the right to make changes to its
products without prior notice.
□
All that is not explicitly indicated
in this manual is to be considered not allowed.
BEFORE INSTALLATION
Before commencing operator installation assess the suitability of
the access, its general condition and the structure.
□
Make sure
that there is no risk of impact, crushing, shearing, conveying,
cutting, entangling and lifting situations, which may prejudice
people safety.
□
Do not install near any source of heat and avoid
contacts with flammable substances.
□
Keep all the accessories
able to turn on the operator (transmitters, proximity readers,
key-switches, etc) out of the reach of the children.
□
Transit trough
the access only with stationary operator.
□
Do not allow children
and/or people to stand in the proximity of a working operator.
□
To
ensure safety in the whole movement area of a gate it is advisable
to install photocells, sensitive edges, magnetic loops and
detectors.
□
Use yellow-black strips or proper signals to identify
dangerous spots.
□
Before cleaning and maintenance operations,
disconnect the appliance from the mains by switching off the
master switch.
□
If removing the actuator, do not cut the electric
wires, but disconnect them from theterminal box by loosening the
screws inside the junction box.
INSTALLATION
All installation operations must be performed by a qualified
technician, in observance of the Machinery Directive 2006/42/CE
and safety regulations EN 12453 - EN 12445.
□
Verify the presence
of a thermal-magnetic circuit breaker 0,03 A - 230 V - 50 Hz
upstream the installation.
□
Use appropriate objects to test the
correct functionality of the safety accessories, such as photocells,
sensitive edges, etc.
□
Carry out a risk analysis by means of
appropriate instruments measuring the crushing and impact force
of the main opening and closing edge in compliance with EN
12445.
□
Identify the appropriate solution necessary to eliminate and
reduce such risks.
□
In case where the gate to automate is
equipped with a pedestrian entrance, it is appropriate to prepare
the system in such a way to prohibit the operation of the engine
when the pedestrian entrance is used.
□
Apply safety nameplates
with CE marking on the gate warning about the presence of an
automated installation.
□
The installer must inform and instruct the
end user about the proper use of the system by releasing him a
technical dossier, including: layout and components of the
installation, risk analysis, verification of safety accessories,
verification of impact forces and reporting of residual risks.
INFORMATION FOR END-USERS
The end-user is required to read carefully and to receive
information concerning only the operation of the installation so
that he becomes himself responsible for the correct use of it.
□
The
end-user shall establish a written maintenance contract with the
installer/maintenance technician (on -call).
□
Any maintenance
operation must be done by qualified technicians.
□
Keep these
instructions carefully.
WARNINGS FOR THE CORRECT OPERATION OF THE
INSTALLATION
For optimum performance of system over time according to safety
regulations, it is necessary to perform proper maintenance and
monitoring of the entire installation: the automation, the
electronic equipment and the cables connected to these.
□
The
entire installation must be carried out by qualified technical
personnel, filling in the Maintenance Manual indicated in the
Safety Regulation Book (to be requested or downloaded from the
site www.fadini.net/supporto/downloads).
□
Operator: maintenance inspection at least every 6 months, while
for the electronic equipment and safety systems an inspection at
least once every month is required.
□
The manufacturer, Meccanica
Fadini snc, is not responsible for non-observance of good
installation practice and incorrect maintenance of the installation.
DISPOSAL OF MATERIAL
Dispose properly of the packaging materials such as cardboard,
nylon, polystyrene etc. through specializing companies (after
verification of the regulations in force at the place of installation in
the field of waste disposal). Disposal of electrical and electronic
materials: to remove and dispose through specializing companies,
as per Directive 2012/19/UE.
Disposal of substances hazardous for the environment is
prohibited.
Meccanica Fadini s.n.c.
Director in charge
CE DECLARATION OF CONFORMITY of the manufacturer:
Meccanica Fadini snc (Via Mantova, 177/A - 37053 Cerea - VR - Italy) declares under its own responsibility that Talos M50 is
in compliance with the Machinery Directive 2006/42/CE, moreover: it is to be sold and installed as a comprehensive
“Automatic System”, including the accessories and components as recommended by the Manufacturing Company. In
observance of the current directives, any automatic system is to be regarded as a “machine”. Therefore it is required that all
the applicable safety norms be strictly complied with by the installation agents, who are also required to issue a
Declaration of Conformity of their own. The manufacturing company is not liable for incorrect applications or misuse of its
products that are declared to be produced in compliance with the following norms: EN 12445 & EN 12453 ie. analysis of the
risk and actions to cure them , Low Voltage Directive 2014/35/UE, Electro-magnetic Compatibility Directive 2014/30/UE.
In order to certify the product, the Manufacturer declares under own responsibility the compliance with the PRODUCT
NORMS EN 13241-1.
2