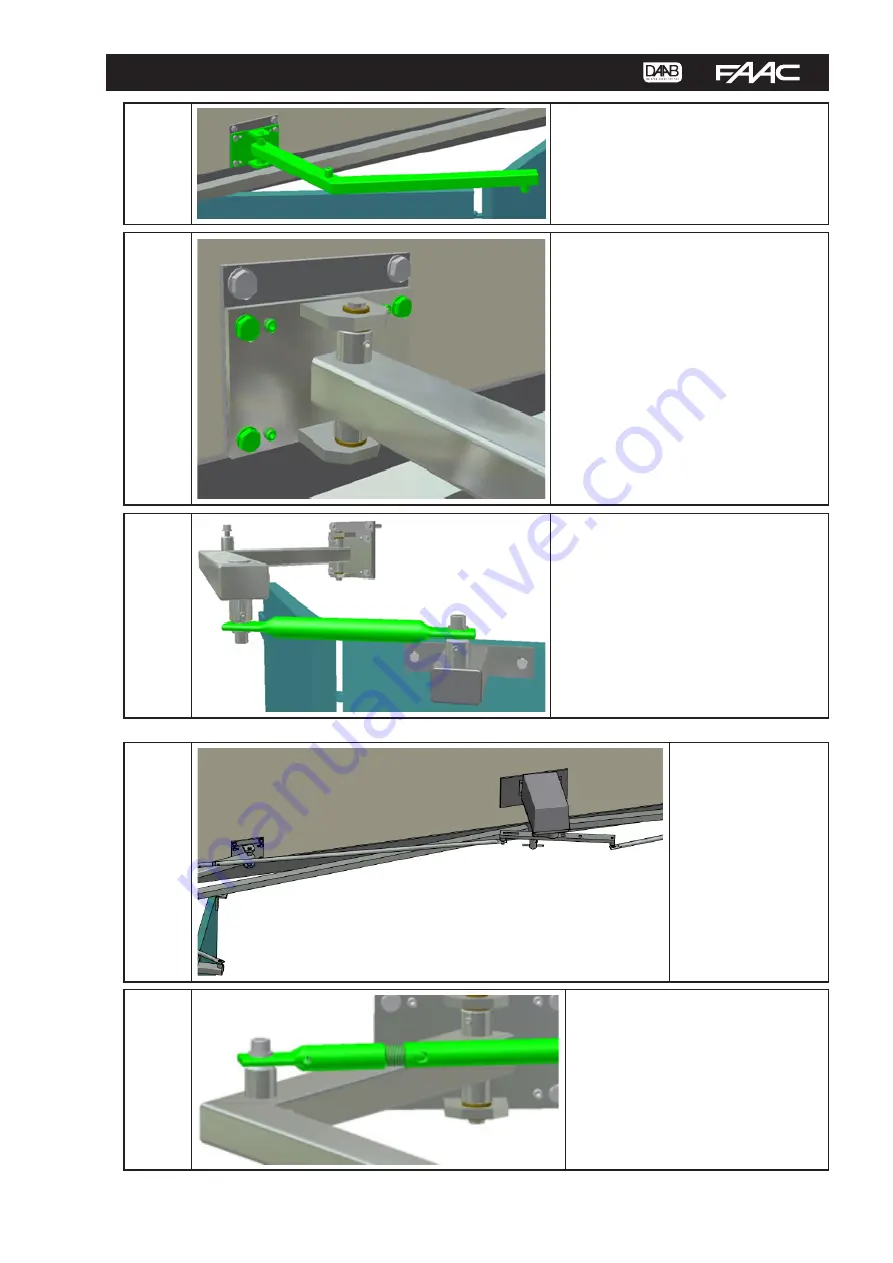
INSTRUCTION MANUAL MT, MA2, MK2, M10 DRIVE UNIT
23
5
Screw the bracket into place on the mounting
plate using four M10 bolts. Adjust the swing
arm so that it is always horizontal.
6
Adjust the mounting using the four set screws.
7
Screw in the short link arm between the outer
swing arm mounting and the gate mounting
using M12 bolts and washers.
Link arm
8
Screw in the link arm
between the drive arm
and swing arm using
M12 bolts and washers.
9
Adjust it by undoing one bolt and then
screwing the arm out or in at the swing arm
mounting.
Summary of Contents for DAAB MT
Page 29: ...INSTRUCTION MANUAL MT MA2 MK2 M10 DRIVE UNIT 29...
Page 30: ......