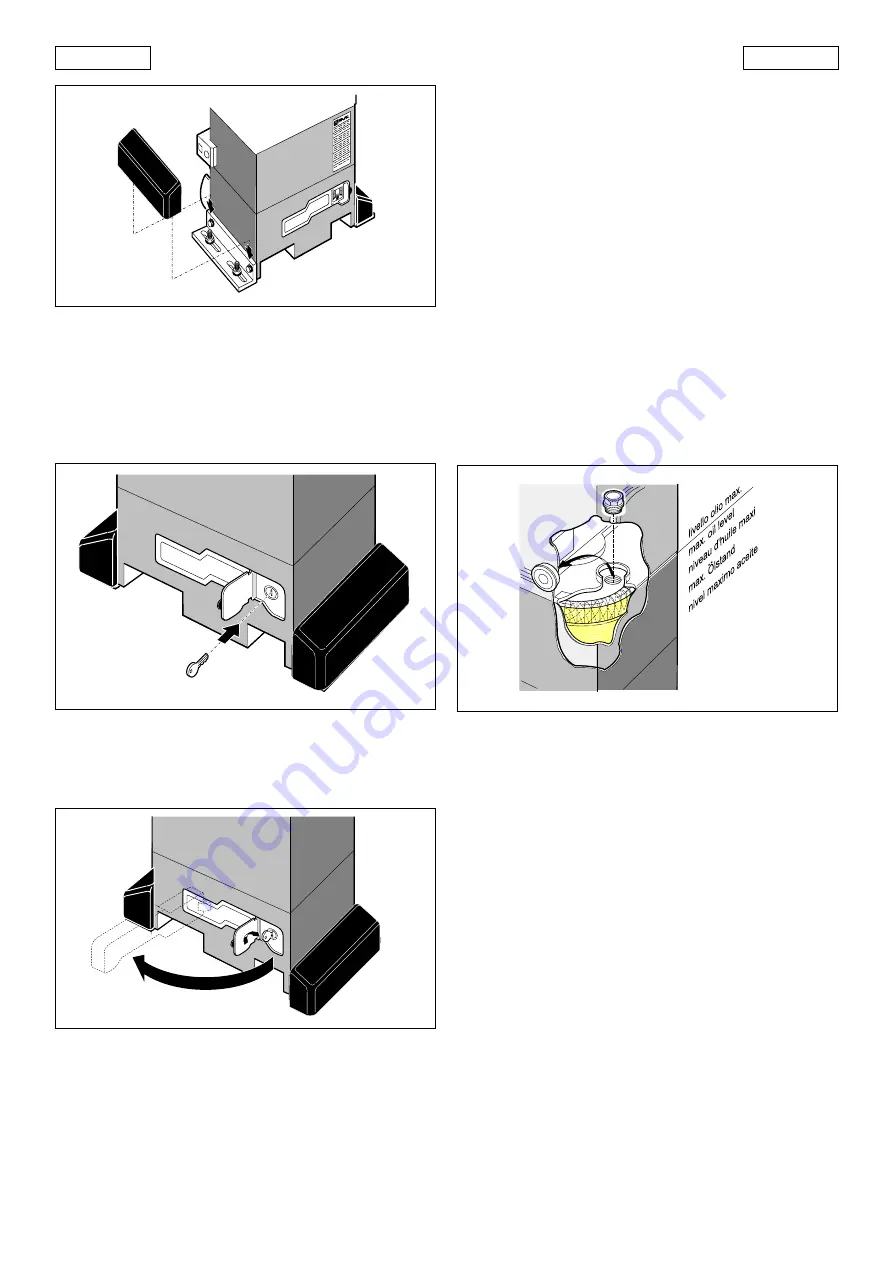
22
ENGLISH
ENGLISH
Fig. 36
Fig. 37
Fig. 38
Fig. 35
Give the customer the User Guide. Explain correct use and
operation of the gear motor and draw attention to the potential
danger zones of the automation.
7. MANUAL OPERATION
If it is necessary to operate the gate manually due to a power
failure or malfunction of the automation, release the electric
lock using the special key and move the gate leaf manually.
If this is not sufficient (serious mechanical malfunction), carry
out the following operations on the release system:
1)
Open the lock cover and insert the key supplied in the lock
(Fig.36).
2)
Turn the key anti-clockwise.
3)
Remove the key and close the lock cover.
4)
Move the gate until the release device engages.
9. SPECIAL APPLICATIONS
There are no special applications.
10. MAINTENANCE
When performing maintenance, always check that the anti-
crushing clutch is correctly adjusted and that the safety devices
operate correctly.
10.1. TOPPING UP WITH OIL
Check the quantity of oil in the operator periodically.
For medium-low duty cycles an annual check is sufficient; for
more intensive use, check every 6 months.
To access the oil reservoir, remove the oil filler cap (Fig.1 ref.10).
The oil level should be up to the copper windings of the electric
motor (Fig. 38).
To top up, pour in oil to the correct level.
Use exclusively FAAC XD 220 oil.
11. REPAIRS
For repairs contact an authorised FAAC Repair Centre.
2)
Turn the key clockwise and pull out the release lever as
shown in Fig.37.
3)
Open or close the gate manually.
8. RETURN TO NORMAL OPERATION
To prevent accidental operation of the gate during this
procedure, turn off the electricity supply to the system before
relocking the operator.
1)
Close the release lever.