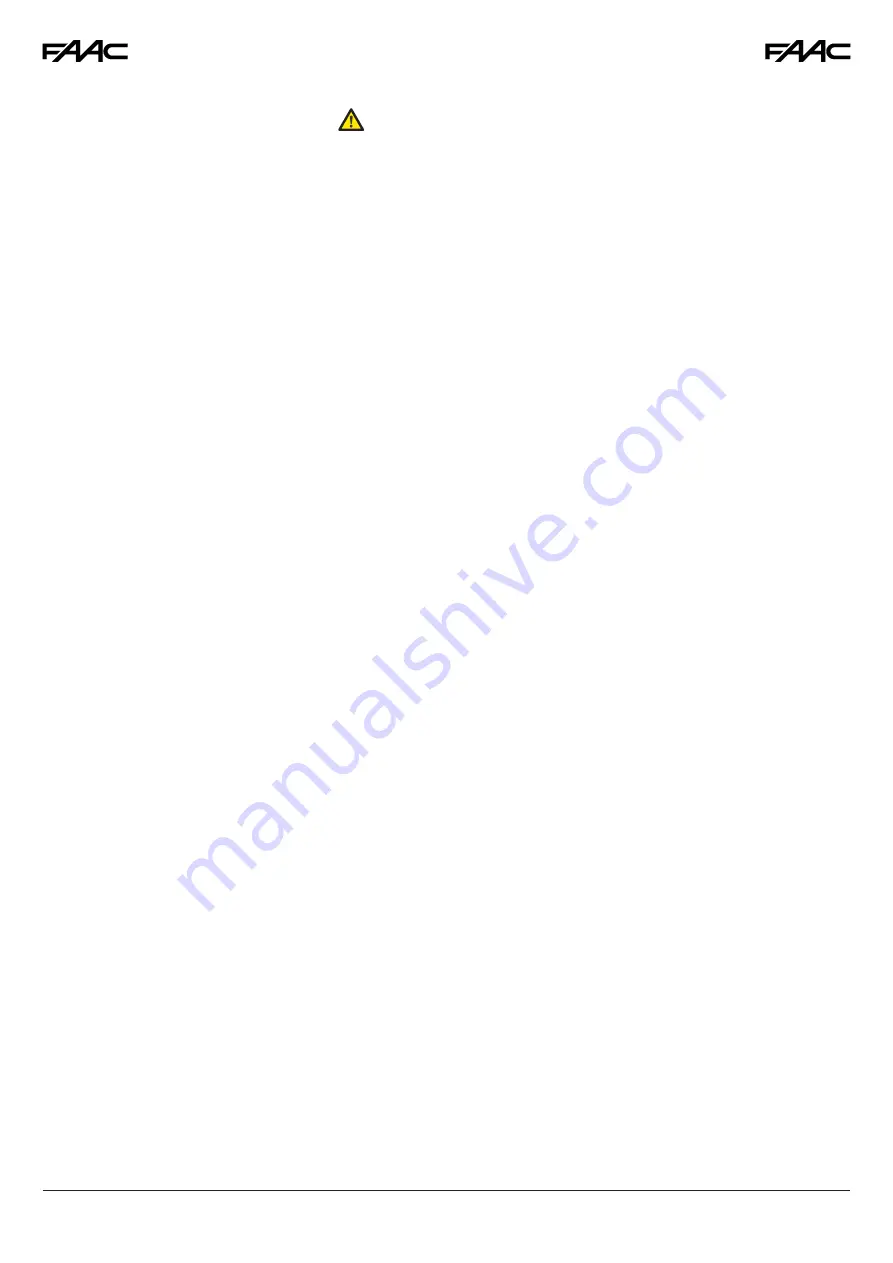
3
a) Install the gate operator only when:
1) The operator is appropriate for the construction of the
gate and usage Class of the gate,
2) All openings of a horizontal slide gate are guarded or
screened from the bottom of the gate to a minimum
of 1.83 m (6 ft) above the ground to prevent a 57.2
mm (2-1/4 in) diameter sphere from passing through
openings anywhere in the gate, and in that portion of
the adjacent fence that the gate covers in the open
position,
3) All areas of the moving vertical pivot gate panel from
the bottom of the gate to the top of the gate or a
minimum of 1.83 m (72 in) above grade, whichever
is less, that pass by a fixed stationary object, and in
the area of the adjacent fence that the gate covers
during the travel of the gate, shall be designed,
guarded or screened to prevent a 57.2 mm (2-1/4 in)
diameter sphere from passing through such areas.
4) All exposed pinch points are eliminated or guarded,
and
IMPORTANT INSTALLATION INFORMATION
WARNING - to reduce the risk of severe injury or death:
1. READ AND FOLLOW ALL INSTRUCTIONS.
2. Never let children operate or play with the gate controls.
Keep remote controls away from children.
3. Always keep people and objects away from the gate.
NO ONE SHOULD CROSS THE PATH OF A MOVING GATE.
4. Test the gate operator monthly. The gate MUST reverse
on contact with a rigid object or stop when an object
activates the non-contact sensors. After adjusting the
force or the limit of travel, retest the gate operator. Fail-
ure to adjust and retest the gate operator properly can
increase the risk of injury or death.
5. Use the emergency release only when the gate is not
moving.
6. KEEP GATES PROPERLY MAINTAINED. Read the user’s
manual. Have a qualified service person make repairs
to gate hardware.
7. The entrance is for vehicles only. Pedestrians must use a
separate entrance.
8. SAVE THESE INSTRUCTIONS.
IMPORTANT SAFETY INFORMATION
5) Guarding is supplied for exposed rollers.
6) The operator instructions shall list the maximum number
of open and close entrapment protection devices
capable of being connected to the operator.
b) The operator is intended for installation only on gates used
for vehicles. Pedestrians must be supplied with a separate
access opening. The pedestrian access opening shall be
designed to promote pedestrian usage. Locate the gate
such that persons will not come in contact with the vehi-
cular gate during the entire path of travel of the vehicular
gate.
c) The gate must be installed in a location so that enough
clearance is supplied between the gate and adjacent
structures when opening and closing to reduce the risk
of entrapment. Swinging gates shall not open into public
access areas.
d) The gate must be properly installed and work freely in both
directions prior to the installation of the gate operator. Do
not over-tighten the operator clutch or pressure relief valve
to compensate for an improperly installed, improperly
functioning, or damaged gate.
e) For gate operators utilizing Type D protection:
1) The gate operator controls must be placed so that the
user has full view of the gate area when the gate is
moving,
2) An additional placard that is marked in letters at least
6.4-mm (1/4-in) high with the word “WARNING” and
the following statement or the equivalent: “Moving
Gate Has the Potential of Inflicting Injury or Death – Do
Not Start Gate Unless Path is Clear.” shall be placed
adjacent to the controls,
3) An automatic closing device (such as a timer, loop
sensor, or similar device) shall not be employed, and
4) No other activation device shall be connected.
f) Permanently mounted controls intended for user activa-
tion must be located at least 1.83 m (6 ft) away from any
moving part of the gate and where the user is prevented
from reaching over, under, around or through the gate to
operate the controls.
Exception: Emergency access controls only accessible
by authorized personnel (e.g.fire, police, EMS) may be
placed at any location in the line-of-sight of the gate.
g) The Stop and/or Reset buttons must be located within line-
of-sight of the gate. Activation of the reset control shall not
cause the operator to start.
h) A minimum of two (2) WARNING SIGNS shall be installed,
in the area of the gate. Each placard is to be visible by
persons located on the side of the gate on which the
placard is installed.
i) For gate operators that utilize a non-contact sensor (photo
beam or similar):
1) See instructions on the placement of non-contact
sensors for each type of application,
2) Care should be exercised to reduce the risk of
nuisance tripping, such as when a vehicle
trips the sensor while the gate is still moving, and
3) One or more non-contact sensors shall be located
where the risk of entrapment or obstruction exists, such
as the perimeter reachable by a moving gate or barrier.