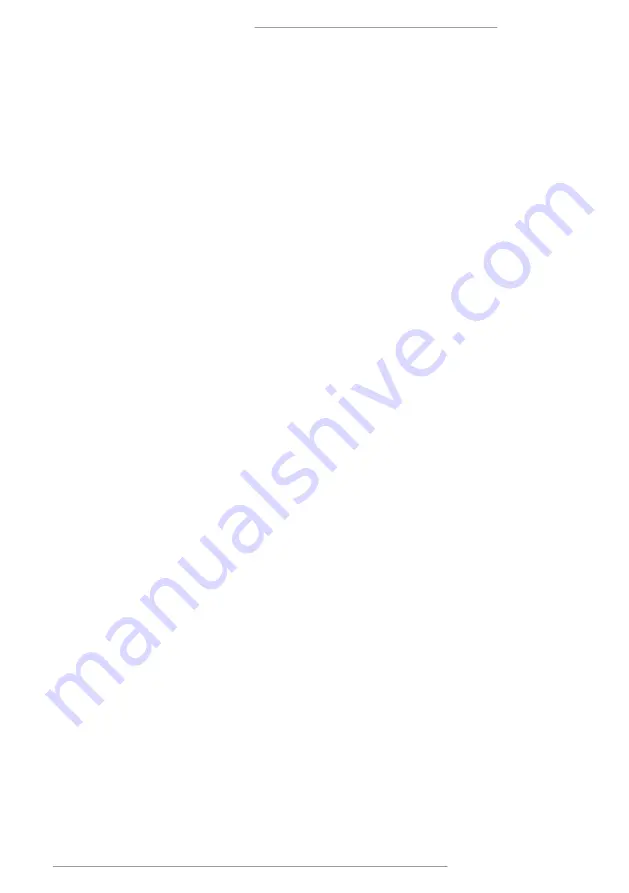
English | 11
www.ffgroup-tools.com
wobble. Push the chuck up on the spindle nose as
far as it can go. Turn chuck sleeve anticlockwise
(when viewed from above) and open jaws in chuck
completely. Place a piece of wood on the machine
table and lower the spindle onto the piece of
wood. Press firmly to ensure that the fitting of the
chuck is properly done.
NOTE:
All bare parts are greased in order to protect them
from corrosion. Before mounting the drill chuck
onto the spindle, both parts must be completely
degreased using an environmentally friendly sol
-
vent. This ensures optimal transmission of power.
Installing the machine:
Before you use the drill for the first time it must
mounted in a stationary position on a firm sur
-
face. Use both mounting holes in the base plate
to do this. Ensure that the machine is freely acces
-
sible for operation, adjustment and maintenance.
WARNING:
The fixing screws may only be tightened to a point
where they do not distort or deform the base plate.
Excessive tension can lead to fracture.
NOTE:
The installed electric motor is completely wired
ready for operation. The customer‘s connection to
the power supply sys¬tem, and any extension cables
that may be used, must conform with local regula
-
tions. Check electrical connection cables regularly
for damage. Make sure the cable is disconnected
from the mains when checking. Electrical connection
cables must comply with the regulations applicable
in your country.
Single-phase motor:
f
The mains voltage must coincide with the voltage
specified on the motor’s rating plate.
f
Dimension cables up to a length of 25m must have
a cross-section of 1.5mm
2
and beyond 25m at least
2.5mm
2
.
f
The connection to the mains must be protected
with an appropriate slow acting fuse.
NOTE:
The motor is automatically switched off in the event
of an overload. The motor can be switched on again
after a cooling down period that can vary.
WARNING:
Connect the machine only to a socket with the prop
-
erly installed ground contact.
OPERATING THE UNIT
WARNING:
For your own safety, keep the machine switch in off
position while performing any of the below proce
-
dures. Machine should be turned on, only if a specif-
ic step of the procedure states so and only for that
particular step.
Installing drill bits:
WARNING:
Only cylindrical tools with the stipulated maximum
shaft diameter may be clamped in the scroll chuck.
Only use a tool that is sharp and free of defects. Do
not use tools whose shaft is damaged or which are
deformed or flawed in any other way. Use only ac
-
cessories and attachments that are specified in the
operating instructions or have been approved by
the manufacturer. If the pillar drill should become
jammed, switch off the machine and return the drill
to its starting position.
Insert the drill bit into chuck far enough to obtain
maximum gripping of chuck jaws. When using a small
drill bit do not insert it so far that the jaws touch the
spiral grooves of the drill bit. Make sure that the drill
bit is centered in the chuck before tightening the
chuck with the chuck key. Tighten the drill chuck
sufficiently, so that the drill bit does not slip while
drilling.
Turn the chuck key clockwise to tighten, anticlock-
wise to loosen.
NOTE:
Your pillar drill is equipped with a keyless chuck. This
enables tools to be changed without the need for an
additional chuck key. To do so, insert the tool in the
quick-change drill chuck and tighten by hand.
Setting the speed (Fig. 1):
The operating speed of the machine is infinitely
adjustable.
NOTE:
Speed adjustments are allowed only when the motor
is running and in idle.
Slowly and steadily move the speed control lever (6)
while the machine is in idle mode. Ensure that the
machine can run without interruption (e.g. remove
work pieces, drill bits, etc.).
WARNING:
Never let the pillar drill run when the V-belt cover
is open. Always pull power plug before opening the
cover. Never touch the V-belt when it is rotating.
Drill depth stop (Fig. 13):
The drilling spindle has a swiveling scale ring (17)
for setting the drill depth. Only adjust the setting
when the equipment is at a standstill.
1. Press the drilling spindle downwards until the
tip of the drill bit touches the work piece.
2.
Loosen the clamping screw (13) and turn the
scale ring (17) forwards until it stops.
3. Turn the scale ring (17) back to the desired drill
depth, and then lock this setting into place us-
ing the clamping screw (13).
NOTE:
When setting the drill depth of a cylindrical hole you
must add the length of the drill tip.
Setting the angle of the drill table (Fig. 14):
Loosen the carriage bolt (18) under the drill table.
Set the drill table to the desired angle. Tighten
down the carriage bolt (18) in order to lock the
drill table into this position.
Setting the height of the drill table (Fig. 15):
Loosen the tightening screw (3). Set the drill table
to the desired position with the help of the hand
crank (14). Screw the tightening screw (3) back
down again.
DPB 16/12 PLUS | DPF 16/12 PLUS
Summary of Contents for DPB 16 PLUS
Page 4: ...4 4 3 12 2 7 8 6 10 9 11 9 10 6 10 9 11 11 12 DPB 16 12 PLUS DPF 16 12 PLUS...
Page 27: ...27 www ffgroup tools com f f f f f f DPB 16 12 PLUS DPF 16 12 PLUS...
Page 28: ...28 1 5 mm2 f DPB 16 12 PLUS DPF 16 12 PLUS...
Page 33: ...33 www ffgroup tools com 1 2 3 4 5 1 2 3 DPB 16 12 PLUS DPF 16 12 PLUS...
Page 53: ...53 www ffgroup tools com DPB 16 12 PLUS DPF 16 12 PLUS...