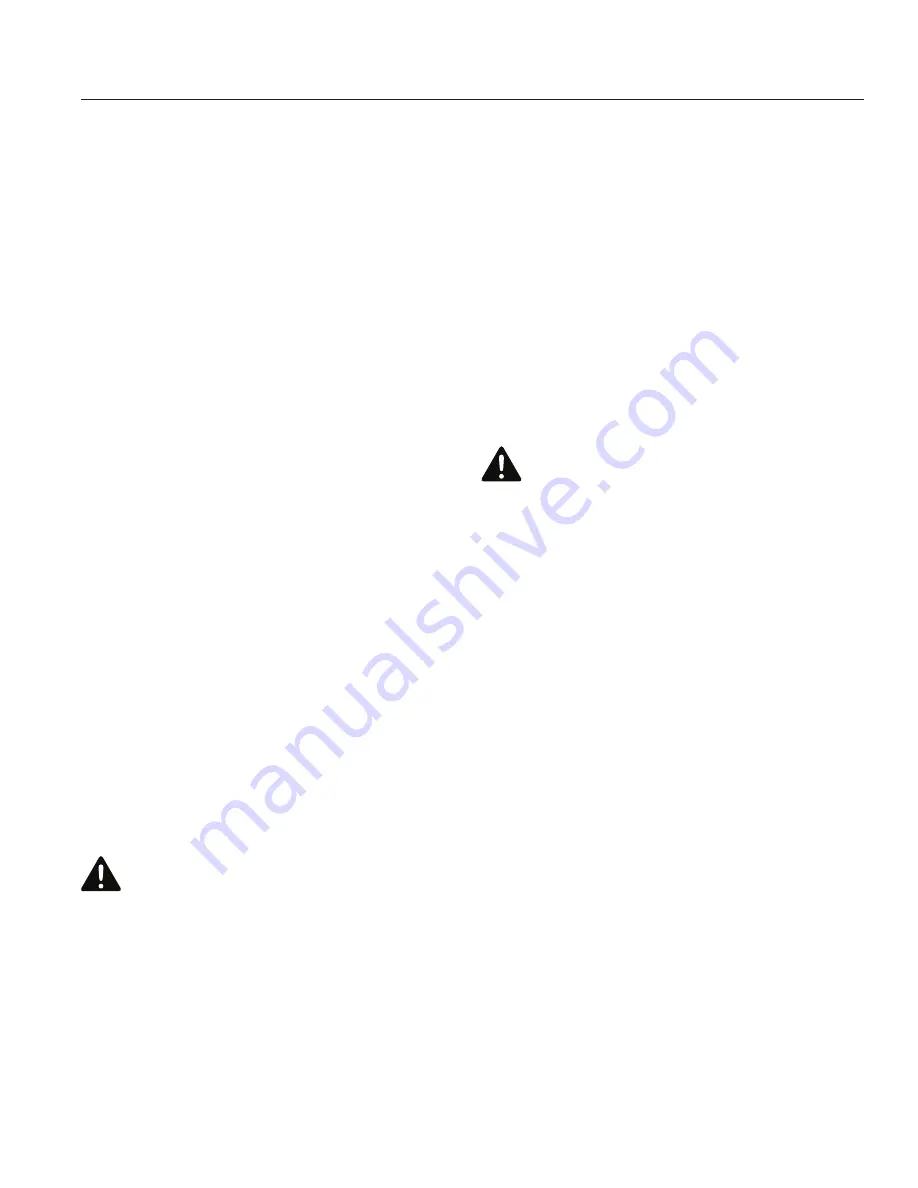
TTX Series DC Actuator Installation & Maintenance Instructions |
9
www.exlar.com
| 952.500.6200
3.2 MOUNTING CONSIDERATIONS
3.2.1 General Operation
The Tritex TTX linear actuators function in the same manner as
a brushless servomotor. The servo amplifier is used to rotate
the motor at controlled speed and torque, and for controlled
numbers of revolutions and move times. This rotary motion is
translated into linear motion by the internal planetary roller screw
mechanism of the Tritex TTX Series linear actuator.
See sections 2.2.1, 2.2.2 and 2.2.3 regarding the holding brake,
anti-rotate mechanisms, and external limit switches and that can
affect the operation and motion of the actuator.
The relationship between the rotary motion of the motor and
the linear motion of the actuator corresponds to the following
relationships:
English
Linear Distance Traveled (in)=(Motor Revolutions)*
(Roller Screw Lead (in))
Linear Speed (in/sec) = ((Motor RPM) / 60)*
(Roller Screw Lead (in))
Linear Force (lbf) = ((Motor Torque (in-lbf))*(2π)*
(efficiency)) / (Roller Screw Lead (in))
Metric
Linear Distance Traveled (mm) = (Motor Revolutions)*
(Roller Screw Lead (mm)
Linear Speed (mm/sec) = ((Motor RPM) / 60)*
(Roller Screw Lead (mm))
Linear Force (N) = ((Motor Torque (N-m))*(2π)*
(efficiency)) / (Roller Screw Lead (mm))
All of the above relationships require proper anti-rotation of the
Tritex TTX actuator rod. For more information on sizing and
selection of Tritex TTX actuator and servo amplifiers to power
them, consult the sizing and selection section of the Exlar
catalog.
CAUTION!
Care should be taken not to exceed the
physical travel limits of Tritex TTX actuators. Doing so will cause
the actuator to end-crash internally. End crashes can physically
damage the roller screw and the internal components of the
actuator. Care should be taken to avoid high-speed impact with
objects of high rigidity that immediately stop the travel of the
actuator with no deceleration or energy absorption. An example
would be a high-speed impact of two solid steel parts. The
resulting impact will create a very short
effective deceleration
time. Kinetic energy contained in the rotating inertia of the
actuator and motor can possibly generate extremely high impact
forces that exceed the mechanical capacities of the actuator and
cause physical damage to the actuator. For applications requiring
this type of impact, contact Exlar application engineering to
ensure that the actuator is properly sized or provisions are made
to absorb the induced energy.
3.2.2 Actuator Alignment
IMPORTANT!
Aligning the Tritex TTX Series actuator with
respect to the load it is moving is critical. Any misalignment
will decrease the life of the actuator’s components and may
adversely affect application performance.
CAUTION!
Excessive side load on the actuator output
rod will dramatically reduce the life of the actuator and should
be avoided. Side load can result from misalignment or loading
that is not in line with the actuator output rod.
Side-mounting notes:
Tritex TTX Series actuators include threaded holes in the
faceplate and endplate. Exlar recommends using hardened
fasteners to mount an actuator to your machine frame with an
engagement depth of two times the screw diameter for tapped
holes.
Stroke length and centering must be carefully considered to
avoid hitting physical travel limits in linear actuators, including
over travel in fast motion profiles. Homing to end of travel may
be done at very slow speed and limited force, but homing
manually or to a limit switch, or maintaining continuous Logic
Power or using the absolute position feedback option to avoid
frequent homing should be considered. Apply appropriate
deceleration ramps to end of moves, or velocity and
acceleration limits in positioners to prevent over-travel.
IMPORTANT!
Tighten four cap screws to 12.24 Nm
(9.0 ft-lb) max. Failure to properly tighten the screws can affect
normal operation, damage the actuator and/or cause possible
premature actuator failure.