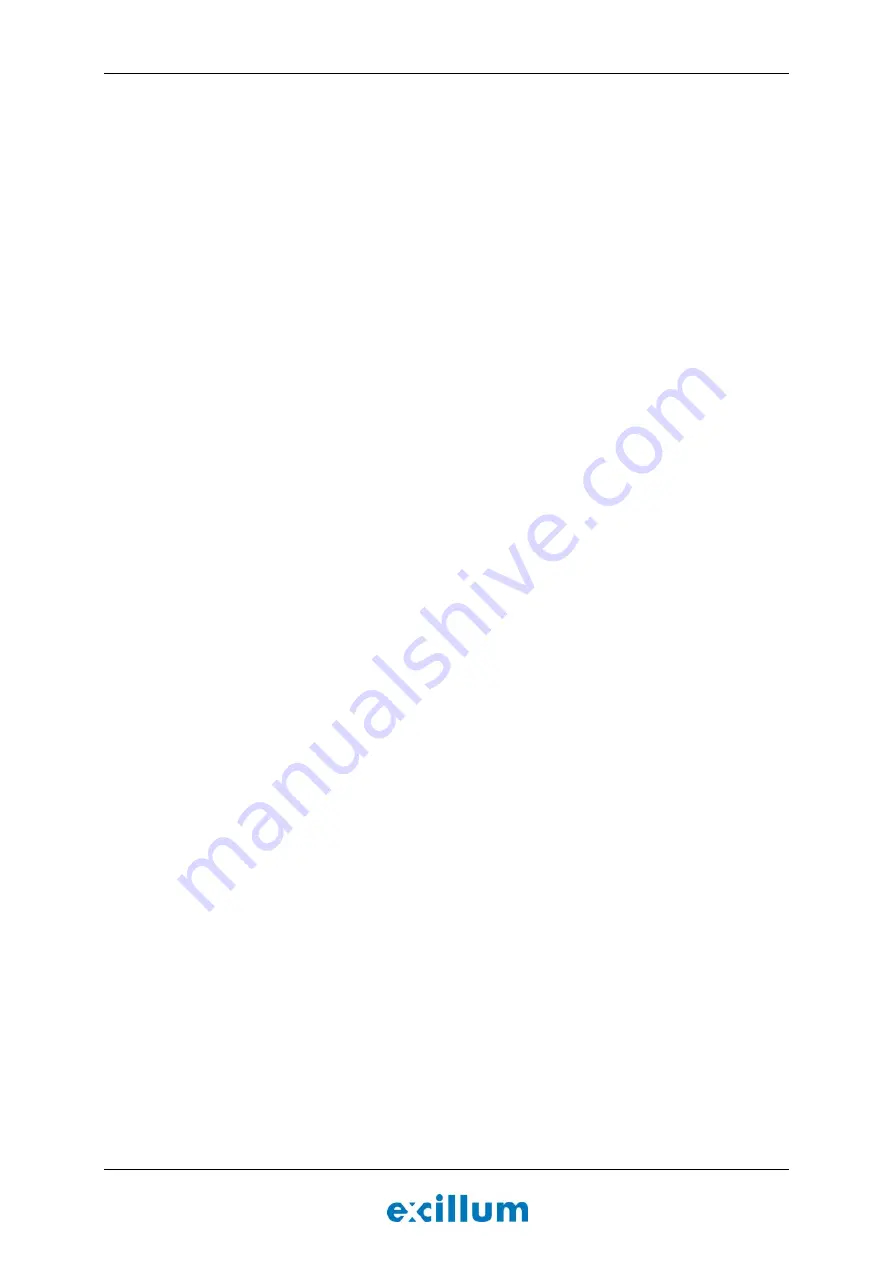
METALJET D2+
Revision 19, November 2016
Page 6-8
maximum aspect ratio of the line focus, which in turn limits the useful lifetime of the cathode. Practically, it
means that the spot size has to be recalibrated on a regular basis.
Periodic spot size calibration:
Periodically running calibrate compensate for the beam dynamics described
above. It keeps the source at specs, and avoids overloading the jet target. Based on beam dynamics
observations we have set the required calibration interval to 24 hours. Calibration can be initiated externally by
sending commands to the server software. Another option is to set up the server to calibrate at a time every
day/night that avoid interrupting experiments.
The accuracy of the calibration routine is controlled by calibrate.max_allowed_deviation_um in the database.
The repeatability between two successive calibrations is better than ±0.5
μm and the default setting of the
parameter is currently 1.0
μm.
Power loading - metal vapor:
Reducing the electron beam spot size increase power loading of the jet which
reduce the safety margin against generating metal vapor. If metal vapor is generated, a fraction will become
ionized and accelerated onto the cathode, causing anisotropic sputtering which increases the cathode
recession rate and deteriorates the general e-beam quality. The power loading limit for MetalJet D2+ targets
are fuzzy limits where cathode lifetime can be traded for application performance.
Linefocus:
When the machine has been set to operate with an elliptical beam, a line focus is generated by
reshaping the circular spot using a combination of lens defocus and stigmator coils. The maximum aspect ratio
that can be achieved is determined by the beam size at the stigmator and the strength of the B field generated
of the coils. If the focusing angle gets below a certain threshold value, the stigmator will stall and will no longer
be able to maintain large aspect ratios.
Lifetime:
The useful lifetime of the cathodes used in the MetalJet D2+ systems is determined by when the
minimum spot size has increased beyond the desired setting or the beam divergence has reduced to the point
where the stigmator coils have reached 500 mA. This assumes that the source operate close to the calibrated
spot size settings where no metal vapor is generated. The source can still be stably operated well beyond this
time but a performance loss can be expected unless the fundamental source parameters are adjusted by an
increase in power or reduced aspect ratio of the beam as compensation.
As a reference, Excillum has significant experience operating the MetalJet D2+ source with an
80x20 μm
2
spot
size at 250 W and 70 kV acceleration voltage. For these settings we can typically operate the source for more
than 2000 hours.
Excillum recommendation:
Service interval driven by application spot size requirements as described above.
Manufacturer information:
Follow recommendation above.
Service instructions:
Service manual under Section
Replace cathode assembly
.