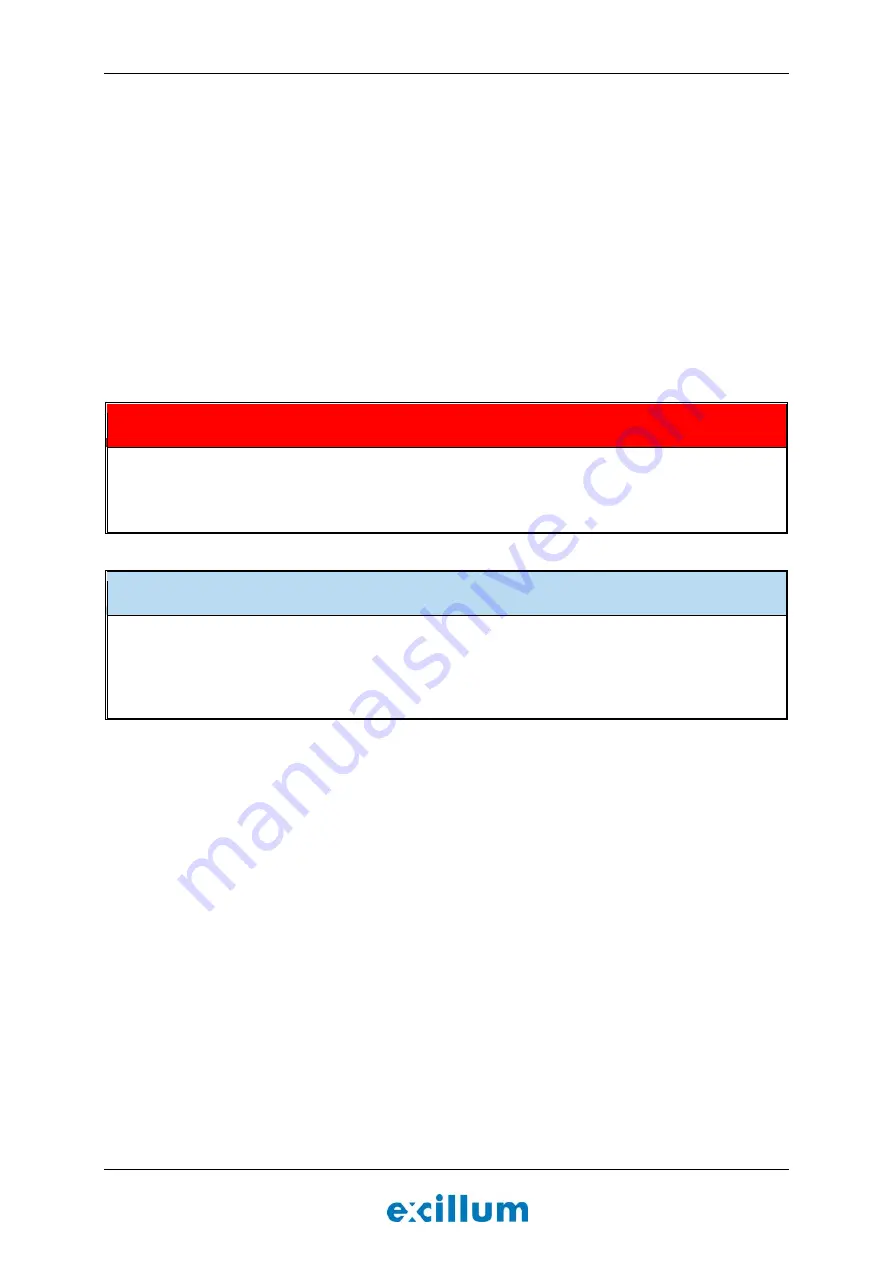
METALJET D2+
Revision 19, November 2016
Page 6-7
Service instructions:
Service manual under Section
Replace exit window
.
6.2.7
Liquid metal spillage
Background:
During installation and service spillage may occur. Under normal conditions there should not be
any leaks from the MetalJet D2+ source causing spillage of liquid metal.
If liquid metal is leaking from any part of the system, immediately contact Excillum according to instructions in
Section 1.3.1.
Excillum recommendation:
Droplets and puddles of liquid metal should be removed using the MetalJet D2+
cleaner. The remaining stains are easiest cleaned using a soap-and-water solution and some lint-free tissue
paper, or a Scotch Brite sponge to remove tougher stains. Gloves should be used to protect hands. Please read
and follow the instructions of the material safety data sheet for the alloy used in your MetalJet D2+ system.
These are appended to this operation manual.
DANGER
Disconnect electricity before cleaning
All parts to be cleaned, or close to those parts being cleaned, must be properly disconnected and de-
energized before cleaning may begin. High voltage is potentially lethal.
NOTE
Gallium is corrosive:
Gallium has a rather high corrosion rate when in contact with a number of different
metals. Among the materials with the lowest corrosion resistance to gallium are aluminum, gold, silver,
zinc, and alloys containing large fractions of these materials. There may, however, be exceptions from this
rule. Contact Excillum (see page ii) for information regarding a specific material.
6.3
Electron gun
6.3.1
Cathode assembly
Background:
The electron emitter of the MetalJet D2+ system consists of a LaB6 crystal that is heated to
extract electrons. The temperatures that these cathodes operate under cause the material to evaporate at a
slow rate. The minimum evaporation rate occurs in a temperature region determined by a combination of
regular material evaporation and a complicated surface chemistry. The emission current from the cathode is
determined by the temperature and the surface area of the cathode, which means that a certain cathode
diameter operates optimally within a certain power range.
Beam dynamics:
When the surface of the cathode evaporates it changes the optical characteristics of the
emitted beam. This can be recorded as a change in the e-beam minimum spot size and focusing angle/beam
aperture over time. These parameters are also logged and displayed at the end of the focusing algorithm and
characterize the optical status of the e-beam. The spot size growth over time can also be understood in terms
of brightness conservation which, neglecting aberrations, forces the focus angle*spot size product to be
constant in an optical system. Generally the nominal beam aperture is optimized depending on the required
DOF (depth-of-focus) and magnitude of aberrations that can be tolerated in the application, with large spot
operation being much more forgiving. Small focusing angles increases the DOF and reduces aberrations, both
of which are considered positive optical effects, but also increases the minimum achievable spot size and