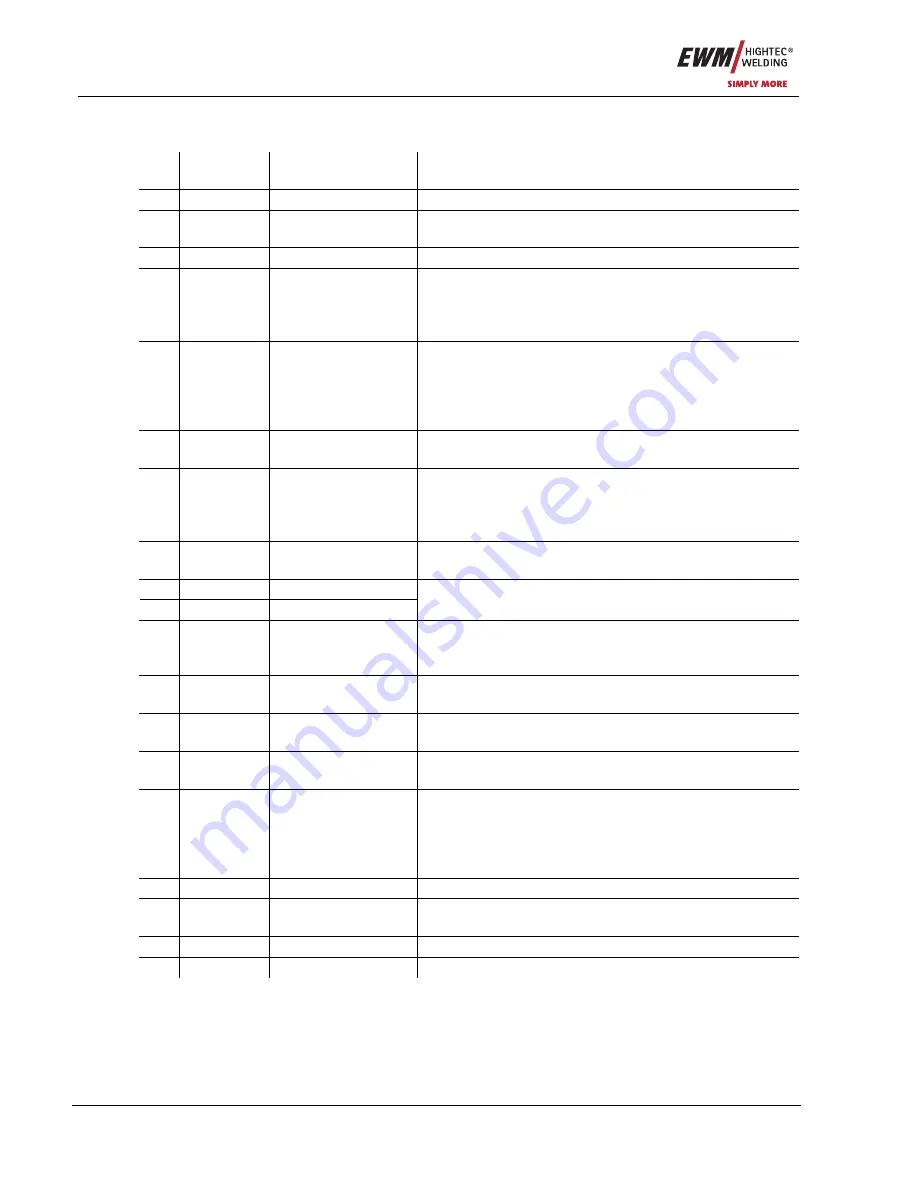
Functional characteristics
Interfaces
46
Item No.: 099-000155-EWM01
19-pole connection assignments for mechanised welding interface (X6):
Pin Signal
shape
Circuit diagram
signal name
Function
A
Output
PE
Connection for cable screen
B
Input
PULSEN EIN
Thermal pulse mode up to max. 50 Hz, fixed balance of
50%
C
Input
SYN_E
Synchronisation for master/slave operation
D
Input
IGRO RELAY
Current flows signal
I > 0
Contact closed = welding current flowing
(forms contact with signal G)
E
Input NOT/AUS
Emergency
stop
for
higher level shut-down of the power
source.
To use this function, jumper 1 must be unplugged on PCB
T320/1 in the welding machine.
Contact open
=
welding current switched off
F
Input
INOMINAL LOW
Control voltage specification for secondary current,
0-10 V (0 V = I
min
/10 V = I
max
)
G
Output
IGRO RELAY
Current flows signal
I > 0
Contact closed = welding current flowing
(forms contact with signal D)
H
Output UACTUAL
Actual
welding
voltage, measured on pin F,
0-10 V (0 V = 0 V, 10 V = 100 V)
J
Output SYN_AE
K
Input SYN_AC
Synchronisation for master/slave operation
L
Input START/STOP Start/stop
welding
current, same as torch trigger.
Only available in non-latched operating mode.
+15 V = Start, 0 V
=
Stop
M
Output
+15 V
Power supply
+15 V, max. 75 mA
N
Input I
soll
HIGH
Control voltage specification for main current,
0-10 V (0 V = I
min
/10 V = I
max
)
P
Input FREQUENZ Nominal
frequency
value
0-10 V (0 V= 50 Hz, 10 V = 0.1 Hz)
R
Input
Emergency stop
Emergency stop for higher level shut-down of the power
source.
To use this function, jumper 1 must be unplugged on PCB
T320/1 in the welding machine.
Contact open
=
welding current switched off
S
Output 0
V
Reference
potential
T
Output I
ist
Welding current, measured on pin F,
0-10 V (0 V = 0 A, 10 V = 1000 A)
U
Input
BR. KOLL. 1
Emergency shut-down collision prot24 V
V
Output
BR. KOLL. 2
Emergency shut-down collision protection