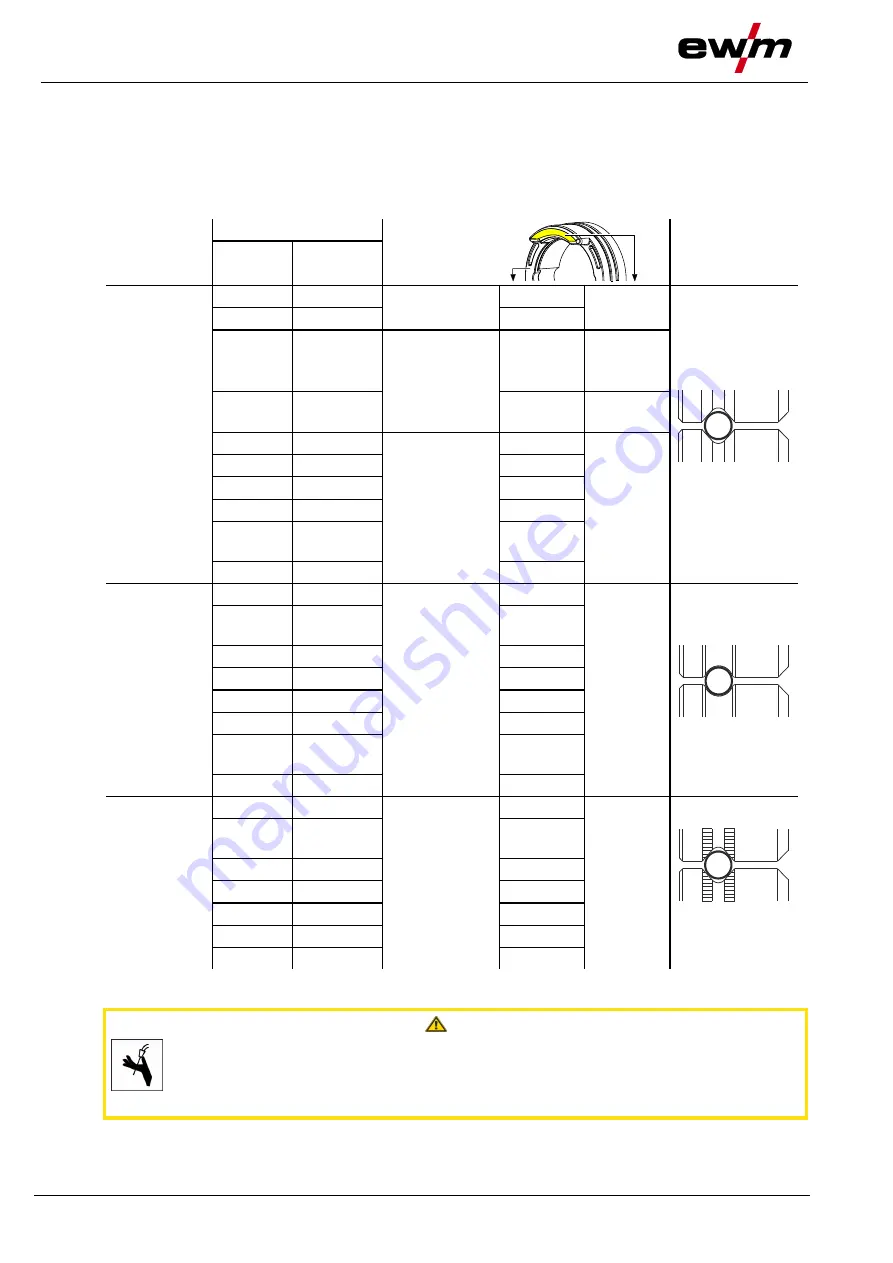
Design and function
MIG/MAG welding
30
099-005549-EW501
12.11.2018
Unsatisfactory welding results due to faulty wire feeding!
The wire feed rolls must be suitable for the diameter of the wire and the material. The wire feed
rolls are colour-coded to facilitate distinction (see the Wire feed roll overview table). When
working with a wire diameter of > 1.6 mm the drive has to be converted for the wire feed kit ON WF
2,0-3,2MM EFEED
> see 10 chapter
.
Wire feed roll overview table:
Material
Diameter
Colour code
Groove form
mm
inch
Steel
Stainless
steel
Brazing
0.6
.023
monochrome
light pink
-
V-groove
0.8
.030
white
0.8
0.9
1.0
.030
.035
.040
bicolour
white
blue
1.0
1.2
.040
.045
blue
red
1.4
.052
monochrome
green
-
1.6
.060
black
2.0
.080
grey
2.4
.095
brown
2.8
.110
light
green
3.2
.125
purple
Aluminium
0.8
.030
bicolour
white
yellow
U-groove
0.9
1.0
.035
040
blue
1.2
.045
red
1.6
.060
black
2.0
.080
grey
2.4
.095
brown
2.8
.110
light
green
3.2
.125
purple
Flux cored
wire
0.8
.030
bicolour
white
orange
V-groove,
knurled
0.9
1.0
.035
.040
blue
1.2
.045
red
1.4
.052
green
1.6
.060
black
2.0
.080
grey
2.4
.095
brown
5.2.2.4 Inching the wire electrode
CAUTION
Risk of injury due to welding wire escaping from the welding torch!
The welding wire can escape from the welding torch at high speed and cause bodily
injury including injuries to the face and eyes!
• Never direct the welding torch towards your own body or towards other persons!