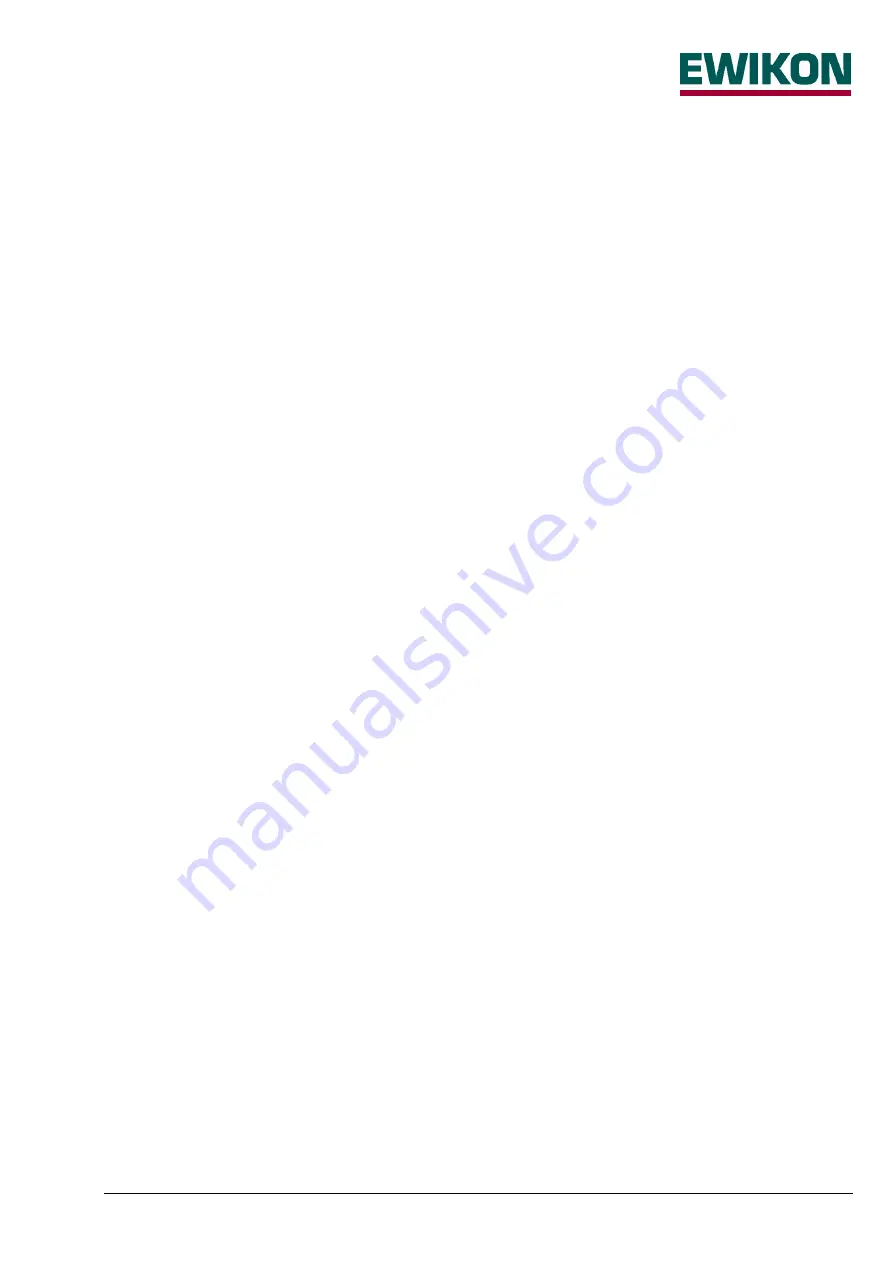
HPS-C - TS operating instructions
Page 7 / 32
The figures on the page on the left show an example of a 24-fold controller 230V with external control panel.
The PC control is connected analogous to the control panel, irrespective of whether it is realised as a controller
rack or wall-mounted device.
To avoid problems, the following procedure should be followed to start up the control system:
•
Before connecting the equipment to the electricity supply the touchscreen monitor (TS) must be fixed to the swivelling
arm supplied. Depending on the model, this is mounted on the controller or must be installed in a suitable place on the
injection moulding machine. The grounding stud on the TS housing must be connected to ground with the PE
conductor cable on the unit's swivelling arm or via a separate PE conductor cable.
•
Connect the communication cable at the TS and at the controller. Ensure that the connector at the second CAN
interface of the controller is fitted with terminating resistance (Art. No. 18096 with socket insert).
•
Connect signal cable 24V DC to the controller and the injection moulding machine controls, if unit group functions
(decrease, fault messages, ...) are required.
•
If necessary, connect addition signalling device 230V to the controller connector provided.
•
Insert the controller's mains plug. Ensure that the power supply matches the data given on the controller's rating plate!
•
Connect connection cable 230V to the rear of the unit and the mould or connection cable 5V to the front of the unit and
the mould. For 5V operation, also connect the ground cable to the mould and the controller, the assignment is
described in greater detail in the chapter "connector pin and terminal assignment“.
•
Connect thermo cable at the rear panel of the unit and the mould.
•
Switch on the unit switch on the rear panel of the unit (in several models also on the side panel).
•
After switching on the Windows operating system starts first on the TS. Then the application program for operating the
HPS-C controllers is automatically loaded and run.
•
After being switched on the TS checks the system configuration connected to the system bus and displays it. The last
used settings are then loaded. This process can take 1 to 2 minutes, depending on the number of control zones. After
the system has successfully started up the TS starts in the "Display" menu, depending on the system configuration, the
display is roughly as shown on page 5.
If problems occur while importing the system configuration, the following measures should be taken:
•
If several controllers are connected to a touchscreen, the address switch of the controllers must be set (from 0 to 3).
The zones are consecutively assigned in the TS starting with unit "0". Maximum 4 controllers can be connected to a
TS; up to 160 zones are supported.
•
Check whether the terminating resistor connector is fitted at the end of the communication cable (last unit).
•
Check for secure fit of the interface cable at all connections and the condition of the cable (pinching along cable layout,
damage ...).
Further operation of the system and value inputs as described on the following pages.