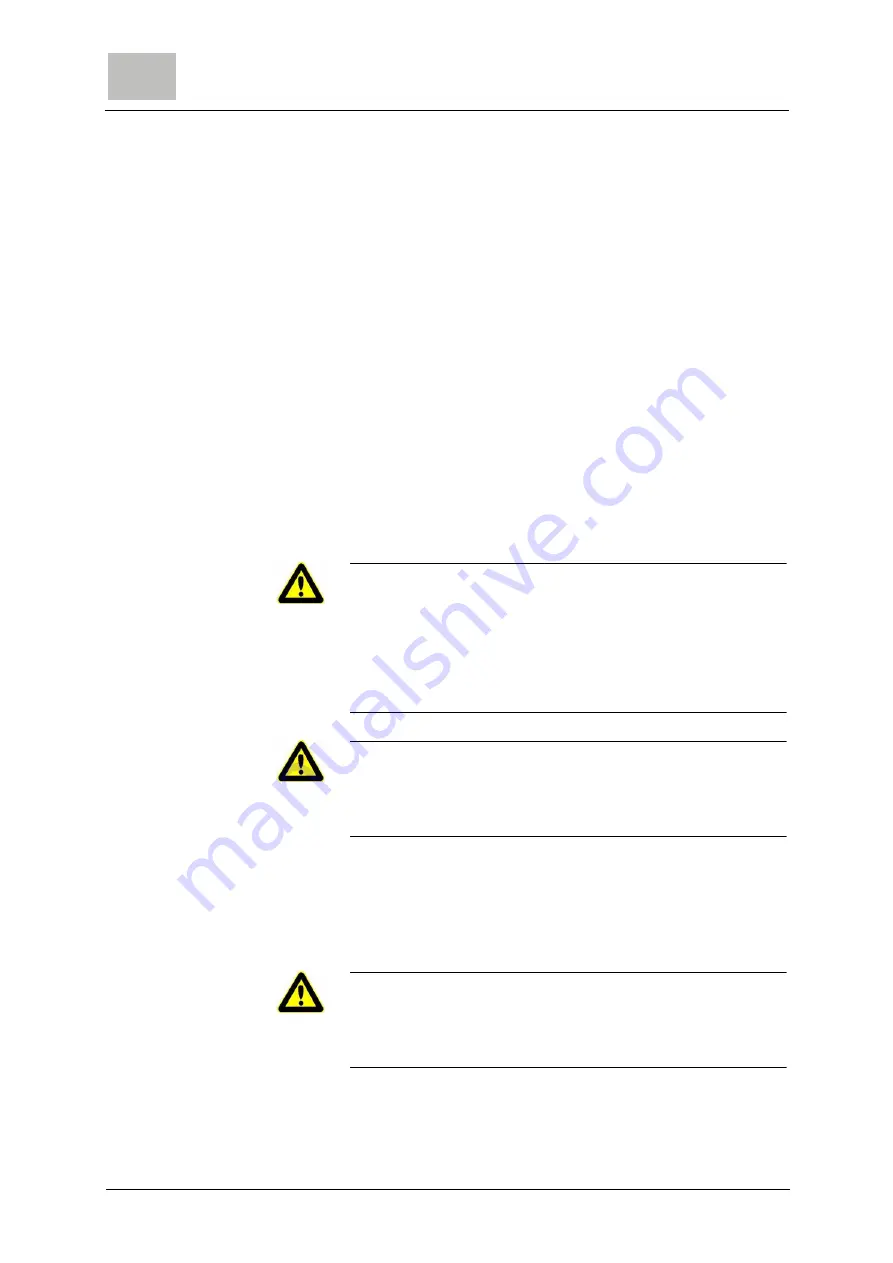
24
WT.025.200.000.DE.IM 0517
Installation
S10k
4.
In case of a CO2 dosing plant the vacuum demand valve is con-
nected to the pressure reducing valve via a pressure hose and
mounted to a wall.
Also refer to „Typical installations“.
•
Unauthorized persons must be excluded from the installation.
•
Adequate access should be available to permit ease of opera-
tion and maintenance of all plant items.
•
The flowmeter assembly should be mounted at eye's height.
•
The ambient temperature around the gas control unit should
be at least 0°C (install a heater if necessary) with a maximum
at 50°C (preferably 15 - 20°C).
•
The system shall be protected against direct exposure to sun
and moisture.
•
Gas containers are heavy and the location should be choosen
to give the shortest possible gas supply line, consistent with
safe handling of the containers.
•
Position and equipment of the chlorine storage and operation
room must correspond to the resp. regulations.
Warning!
To avoid personal injury by chlorine gas, install the equipment so
that in case of a fault chlorine gas may escape within the storage
room only. Those parts of the chlorine system that may be under
pressure (such as tanks, regulating valves, relief valve, relief line
and activated carbon filter) may be installed in the storage room
only. Refer to the national or regional regulations.
Caution!
When a heater is installed, take care that the temperature of the
gas cylinder doesn’t rise above ambient temperature. Otherwise
there is risc of reliquefaction of Cl2 and SO2.
4.3
Flowmeter assembly
Warning!
The flowmeter/plug assembly is designed to operate under vacu-
um only. To avoid possible severe personal injury or equipment
damage, do not connect it to a source of gas under pressure.
The flowmeter is mounted remote from the demand valve, on a
vertical surface (such as a wall or a column) at the height conveni-
ent for reading by the operator.
Summary of Contents for WALLACE & TIERNAN S10k
Page 1: ...WALLACE TIERNAN GAS FEEDER S10k INSTRUCTION MANUAL ...
Page 2: ...2 WT 025 200 000 DE IM 0517 S10k Please note Original manual ...
Page 6: ...6 WT 025 200 000 DE IM 0517 Contents S10k ...
Page 22: ...22 WT 025 200 000 DE IM 0517 Description S10k 3 ...
Page 90: ...90 WT 025 200 000 DE IM 0517 Drawings S10k 7 7 4 2 Anti syphon injector W3T171368 1 ...
Page 93: ...S10k Drawings 7 93 ...
Page 94: ...94 WT 025 200 000 DE IM 0517 Drawings S10k 7 7 4 3 Injector W3T171369 3 4 ...
Page 96: ...96 WT 025 200 000 DE IM 0517 Drawings S10k 7 7 4 4 Antisyphon Injektor W3T171370 3 4 ...
Page 99: ...S10k Manufacturer declaration 8 99 8 Manufacturer declaration ...
Page 100: ...100 WT 025 200 000 DE IM 0517 Manufacturer declaration S10k 8 ...