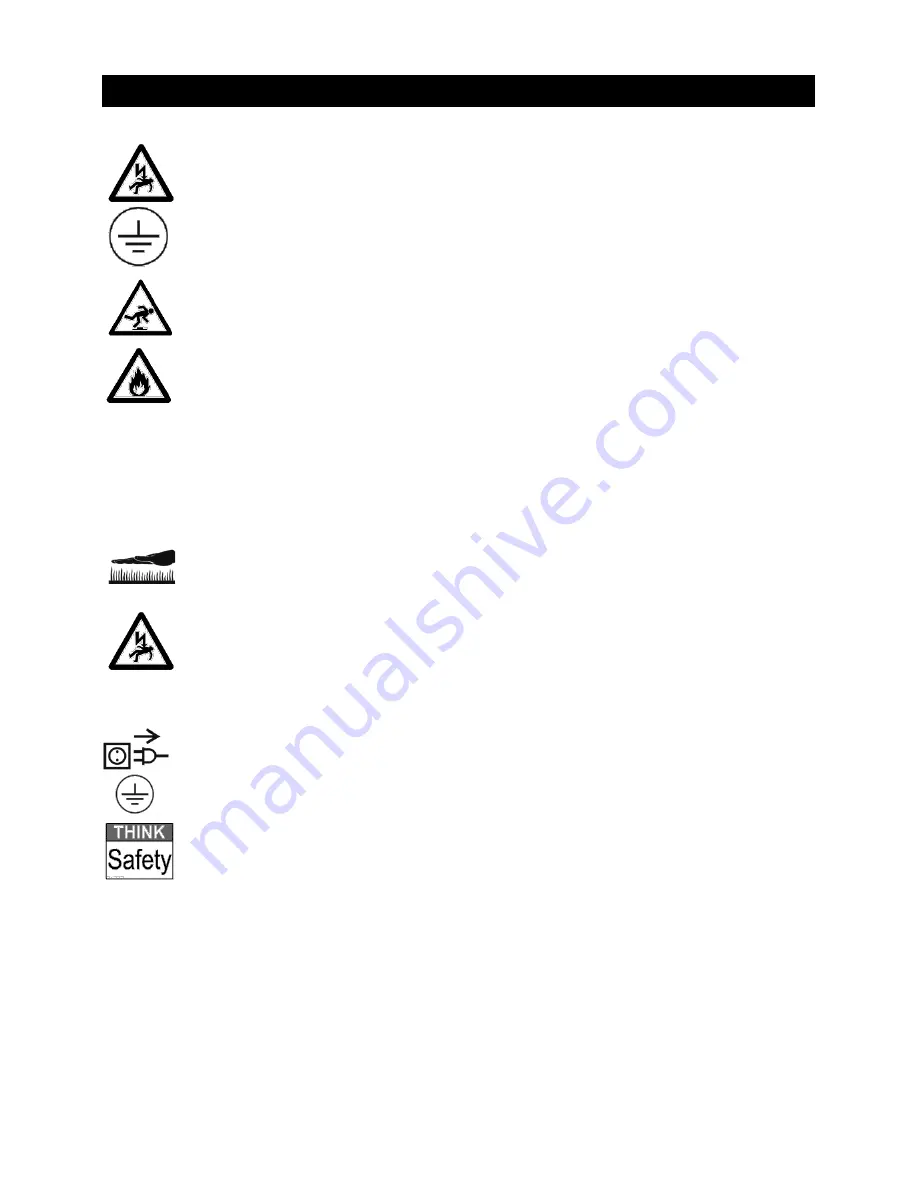
8
Safety Precautions
WARNING! Electrical shock can kill. Make sure all electrical equipment is properly grounded. Do not use frayed, cut
or otherwise damaged cables and leads. Do not stand, lean or rest on ground clamp. Do not stand in water or damp
areas while welding or cutting. Keep work surface dry. Do not use welder or plasma cutter in the rain or in extremely
humid conditions. Use dry rubber soled shoes and dry gloves when welding or cutting to insulate against electrical
shock. Turn machine on or off only with gloved hand. Keep all parts of the body insulated from work, and work tables.
Keep away from direct contact with skin against work. If tight or close quarters necessitates standing or resting on
work piece, insulate with dry boards and rubber mats designed to insulate the body from direct contact.
All work cables, leads, and hoses pose trip hazards. Be aware of their location and make sure all personnel in area are
advised of their location. Taping or securing cables with appropriate restraints can help reduce trips and falls.
WARNING! Fire and explosions are real risks while welding or cutting. Always keep fire extinguishers close by and
additionally a water hose or bucket of sand. Periodically check work area for smoldering embers or smoke. It is a good
idea to have someone help watch for possible fires while you are welding. Sparks and hot metal may travel a long dis-
tance. They may go into cracks in walls and floors and start a fire that would not be immediately visible. Here are
some things you can do to reduce the possibility of fire or explosion:
•
Keep all combustible materials including rags and spare clothing away from area.
•
Keep all flammable fuels and liquids stored separately from work area.
•
Visually inspect work area when job is completed for the slightest traces of smoke or embers.
•
If welding or cutting outside, make sure you are in a cleared off area, free from dry tender and debris that might start
a forest or grass fire.
•
Do not weld on tanks, drums or barrels that are closed, pressurized or anything that held flammable liquid or material.
Metal is hot after welding or cutting! Always use gloves and or tongs when handling hot pieces of metal. Remember to
place hot metal on fire
-
proof surfaces after handling. Serious burns and injury can result if material is improperly han-
dled.
WARNING! Faulty or poorly maintained equipment can cause injury or death. Proper maintenance is your responsibil-
ity. Make sure all equipment is properly maintained and serviced by qualified personnel. Do not abuse or misuse
equipment. Remove any faulty cords, plugs or electrical equipment from service or access.
Keep all covers in place. A faulty machine may shoot sparks or may have exploding parts. Touching uncovered parts
inside machine can cause discharge of high amounts of electricity. Do not allow employees to operate poorly serviced
equipment. Always check condition of equipment thoroughly before start up.
Disconnect unit from power source before any service attempt is made and for long term storage or electrical storms.
If operating on a generator: Always switch off and disconnect the unit before shutting the unit down. Never start the
generator with the unit switched on or connected. Failure to do so may result in damage to the unit. This damage is
not covered under warranty. Make sure that any required generator grounding is performed properly and to the manu-
facturer
’
s recommendations.
Further information can be obtained from The American Welding Society (AWS) that relates directly to safe welding
and plasma cutting. Additionally, your local welding supply company may have additional pamphlets available concern-
ing their products. Do not operate machinery until your are comfortable with proper operation and are able to assume
inherent risks of cutting or welding
.
Summary of Contents for Power i-MIG 353DPi
Page 47: ...47...