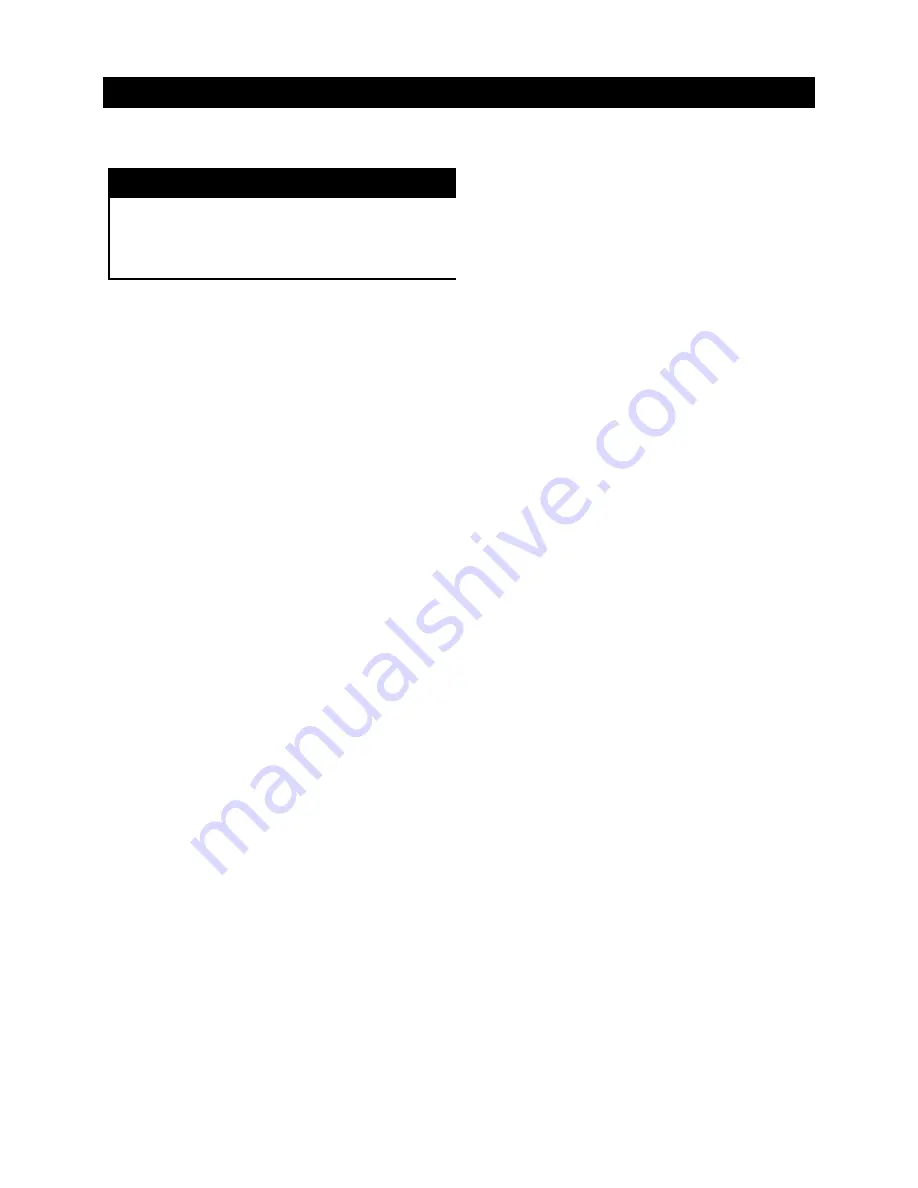
36
PULSE MIG OPERATION
The Single Pulse MIG function has 3 basic parts of the pulse. When
judged by itself, each pulse control function has a specific effect on the
weld. But each pulse function can also have an overlapping effect of
another pulse function. This depends upon how the individual pulse
function is adjusted relative to the other two remaining functions. Due to
the complexities and endless combinations of the pulse settings, the
unit is programmed with an algorithm that has been determined to offer
the best range of control and remove settings that would be unproduc-
tive and non
-
workable. Though this may sound confusing at first, a little
practice will make sense out of it. Even those these functions are con-
trolled by the synergic programming and are out of the user
’
s control,
the two main purposes in discussing the components of that make up a
pulse cycle is to make the user aware of the complexities surrounding
Pulse and to give better understanding of the mechanics of the pulse.
Although these settings are factory
“
optimized
”
by an algorithm, that
does not mean that the settings are going to be perfect for every indi-
vidual or every application. To further fine tune the pulse after you input
values for wire type, wire diameter and metal thickness (Amps), you
can use the Voltage Offset feature. The range of adjustment is from –
5
to +5. This Offset feature is also known as Trim. The Voltage Offset
simply skews the factory settings for the Pulse voltages up or down,
effectively changing arc length, heat, and puddle fluidity.
Due to the different gases, operator styles and welding positions used,
the Offset can be used to
“
tune
”
the welder to the best operating set-
tings. As a
“
best
-
practice
”
policy, start low in the range, around –
4
to –
3 and increasing one whole number at a time until the operation is
improved. After a
“
close
”
setting is found, further tune in .1 increments.
Using a wider adjustment increment than this will often cause you to
skip past a ideal parameter setting without giving you an indication that
you may be nearing the
“
sweet spot
”
for the setting. As you adjust this
setting, you will notice a change in arc quality and in sound. This is
normal. Resist the temptation to go too far toward the positive end of
the scale or burn
-
burn back and tip melting will become an issue. This
unit is programmed for using Standard shielding gases designed for
use with Pulse MIG. Different gas mixes may be used however. Each
gas blend will result in a different setting of the Voltage Offset feature.
As more CO2 is used in the shielding gas (always use 20% or less),
you will need to increase the value of Voltage Offet. Lower concentra-
tions require less Voltage Offset.
Remember, the pulse feature is intended to be used to control heat
input and improve out of position welding capability without creating
large sacrifices in travel speed or penetration. Even before attempting to
set the voltage offset, begin by setting wire speed feed/amps to match
metal thickness. Usually this is 1 amp per
.001”
of thickness. This is an
old rule of thumb and is not accurate in every case. You will notice that
when pulsing the unit actually deviates from the settings selected be-
cause it is averaging the pulsed values to compensate. This is not a
defect. With synergic Single Pulse, keep in mind that the Amps control
penetration and too many amps can produce burn through. If in doubt,
use the wire manufacturer
’
s suggested settings found on the packaging
or in their published materials. In the absence of these references, if
you do not know an approximate setting for Amps, you can use the
formulas suggested earlier in this manual to determine the approximate
wire feed speed/amp value. After initially set, Amps should only be
adjusted again after no workable setting for the Voltage Offset or Induct-
ance has been found. Avoid radical changes in Amps. A space of 3 or
4 Amps can yield a much different level of performance.
Below you will find the three Single Pulse parameters that are syner-
gically controlled. and their basic effects on the weld identified along
with additional features affecting the performance of the single
-
pulse
feature of this unit.
Double Pulse Explanation.
The double
-
pulse features more manual
control over the weld cycle than the Single Pulse does. However, it is
still considered to be synergic in function. This is because the Double
-
Pulse relies upon the Synergically adjusted Single Pulse. The Double
-
Pulse is simply two separate settings of Single Pulse, which alternate
from .1 to 9.9 times a second. The Peak Pulse value for the Double
Pulse is set just as you would with the Single Pulse. Both Amps and
the Voltage offset can be adjusted. The Base Pulse Value for the Dou-
ble Pulse is set identically. The programming of the machine sets each
half of the pulse cycle synergically. This
“
layering
”
of the pulse creates a
heating phase and a cooling phase during one cycle of the Pulse. The
Heating stage (notated on the machine as Peak LED) provides the pri-
mary melting and advancement of the weld puddle. The Cooling stage,
or the base (notated as the welding LED on the machine) keeps the arc
going, but the puddle is discernably cooler and the metal begins to
solidify, creating a single ripple. Do not try to set the base as the higher
value. Set the Peak as the higher value and the Welding setting as the
lower, base value. Doing so may confuse the operator and the pro-
gramming of the machine, resulting in poor weld performance.
To set Amps properly in the Double Pulse, first set Peak Pulse amps as
you would for welding in Single Pulse normally, and up to 20% higher if
desired. Begin to set the Base amps (Welding LED) with an Amp set-
ting that is 50 to 75% of the Peak Amps. Do not change or adjust the
Volt Offset unless needed. Keep the Volt Offset value the same in both
Peak and Base portions.
The Frequency of the Double Pulse results in regulating the spacing of
the ripples in the weld. A slow frequency will yield large, coarse ripples,
while the faster frequency will begin to refine and tighten up spacing
between the ripples. To achieve TIG like results, try setting the Pulse to
1 to 3 Hz. A steady travel speed and a close watch on the puddle will
give good results initially. With practice, the results can be improved by
manipulating the torch in time with each double pulse cycle. This is
accomplished moving forward followed by a brief pause timed to coin-
cide with the up and down cycles of the weld.
The Pulse Time
-
On is similar to the Pulse
-
Time On featured in the
example on page 36. However, you are simply skewing the time the
pulse spends welding in the high stage of single pulse setting against
the time the pulse spends welding at the low pulse setting. Increasing
the Pulse Time
-
On increases the heat put into the weld an reduces the
freezing action if the pulse hertz. Penetration will be deeper. Decreas-
ing the Pulse Time
-
On increases the cooling effect, and definition but
may also reduce penetration and travel speed. For balanced, even look
without sacrificing travel speed, consider setting Pulse Time on to 40 to
60% as an initial setting range.
Pulse MIG and Inductance. Whether in Single Pulse Mode or Double
Section 2 Setup Guide
IMPORTANT:
Keep in mind that while these functions are discussed, they are auto-
matically set by the Unit
’
s programming based off of the User inputs of
Wire diameter, Wire Type and Metal Thickness (Amps). These are
discussed only to help further the understanding of what the single
pulse function is and does.
Summary of Contents for Power i-MIG 353DPi
Page 47: ...47...