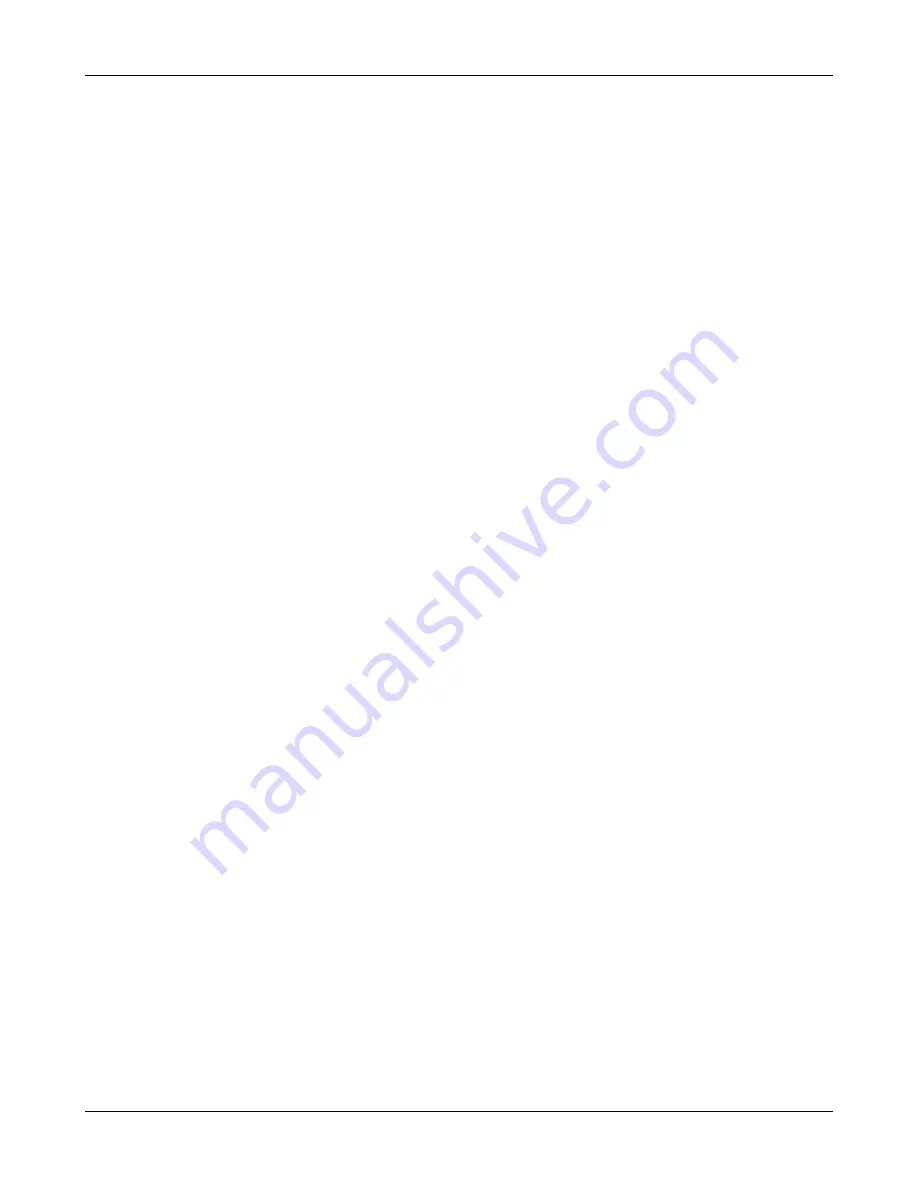
Chapter 8 - Appendices
8 - 2
584S Frequency Inverter
Synchronous Motors
Although intended primarily for use with induction (asynchronous) motors, inverters can also be used for speed control of
synchronous motors. Synchronous motors can offer economic solutions in applications where tight control of speed is
required together with the low maintenance characteristics of an AC motor.
The two most common types of synchronous AC motor are permanent magnet and wound rotor. In contrast to induction
motors, synchronous motors run at synchronous speed whether on no load or full load. Synchronous speed is set by the
frequency of the supply applied to the stator. The stator flux can be kept constant by keeping the stator volts/frequency ratio
constant as with an induction motor.
Torque is produced in the motor by a increase in load angle between the stator and rotor fluxes. Maximum torque occurs
when the load angle approaches 90
°
. If the load angle exceeds this value then torque drops and the motor will stall. Systems
involving synchronous motors need careful design to ensure that the motor can accelerate the load and handle transient load
changes without stalling.
Brake Motors
Brake motors are used in applications requiring a mechanical brake for safety or other operational reasons. The motor can
be a standard induction motor fitted with an electromechanical brake or it could be a special conical rotor machine. In the
case of a conical rotor machine the spring-loaded brake is controlled by the motor terminal voltage as follows:
a)
At rest the motor is braked;
b)
When the motor is energised an axial component of the magnetic field, due to the conical air-gap, overcomes the force
of the brake spring and draws the rotor into the stator. This axial displacement releases the brake and allows the motor
to accelerate like a normal induction motor;
c)
When the motor is de-energised the magnetic field collapses and the brake spring displaces the rotor, pushing the brake
disc against the braking surface.
d)
Inverters can be used to control the speed of conical rotor brake motors since the linear V/F characteristic maintains the
motor magnetic field constant over the speed range. It will be necessary to set the
FIXED BOOST
parameter to
overcome motor losses at low speed.
Using Line Chokes
Line chokes are not required to limit input current to Eurotherm Drives inverters. Controllers from 5.5kW ( 400v) or
2.2kW ( 230v) upwards are fitted with DC link chokes to limit the ripple current seen by the DC link capacitors and thus
prolong their life.
Line chokes may be used to reduce the harmonic content of the supply current where this a particular requirement of the
application or where greater protection from mains borne transients is required.
Using Output Contactors
The use of output contactors is permitted. It is recommended that this type of operation be limited to emergency use only or
in a system where the drive can be inhibited before closing or opening this contactor.
This manual was downloaded on www.sdsdrives.com
+44 (0)117 938 1800 - [email protected]
Summary of Contents for 584S
Page 122: ...This manual was downloaded on www sdsdrives com 44 0 117 938 1800 info sdsdrives com ...
Page 173: ...This manual was downloaded on www sdsdrives com 44 0 117 938 1800 info sdsdrives com ...
Page 174: ...This manual was downloaded on www sdsdrives com 44 0 117 938 1800 info sdsdrives com ...
Page 175: ...This manual was downloaded on www sdsdrives com 44 0 117 938 1800 info sdsdrives com ...