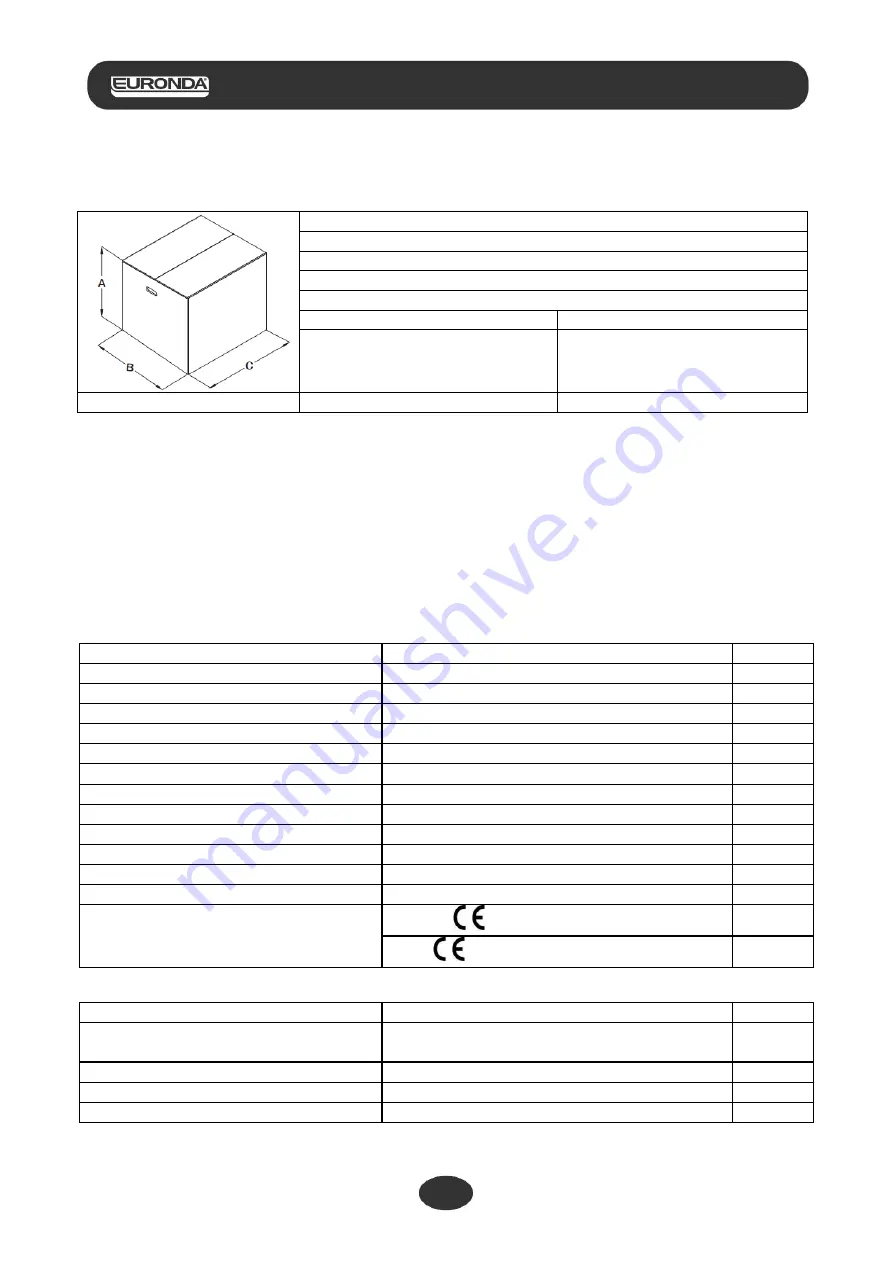
Aquafilter
E9_Next_Ing_rev03 – 10/10/2018
12
E9 NEXT
CHAPTER 4
4.1
WEIGHT AND DIMENSIONS OF PACKAGING
Overall dimensions of packaging:
A = 545 mm
B = 560 mm
C = 745 mm
Total weight of packaging:
E9 NEXT 18L
E9 NEXT 24L
50 kg
54 kg
Fig. 4.1-1
4.2
RECEIPT AND HANDLING
On receipt of the machine, check that the packaging is intact (keep it for future despatches).
Open the packaging and check that:
- the supply meets the technical specifications (chap. 4.3 “Description of contents”);
- there are no obvious signs of damage.
If any damage or missing parts are discovered, inform the hauler, wholesaler or Euronda S.p.A immediately,
providing all details.
Handle the packed unit as described in chap. 6.1 “Work environment: positioning” (Fig. 6.1-1).
4.3
DESCRIPTION OF CONTENTS
Description
Specifications
Quantity
Steam sterilizer E9 NEXT
Steriliser 18L - Steriliser 24L
1
Tray
Anodized aluminium perforated tray
5
Tray carrier
Support with 5 compartments in stainless steel
1
Extractor pincer
Pincers for extracting trays
1
Door adjustment lever
Stainless steel lever for adjusting the door gasket
1
Water drainage tube
Transparent PVC tube with quick fit attachment
1
Overfill draining tube
Transparent PVC tube
1
Instructions manual
This manual
1
Warranty certificate
1
Quick start sheet
1
Installation sheet
1
Test Report
1
Declaration of conformity
Steriliser:
0051
1
Boiler:
0497
1
4.3.1 Optional devices (also see Appendix 10)
Description
Specifications
Quantity
Aquafilter
External deioniser for the automatic supply of
water
1
Integrated printer
Thermal paper printer
1
Integrated printer
Label Printer
1
External printer
Label Printer
1