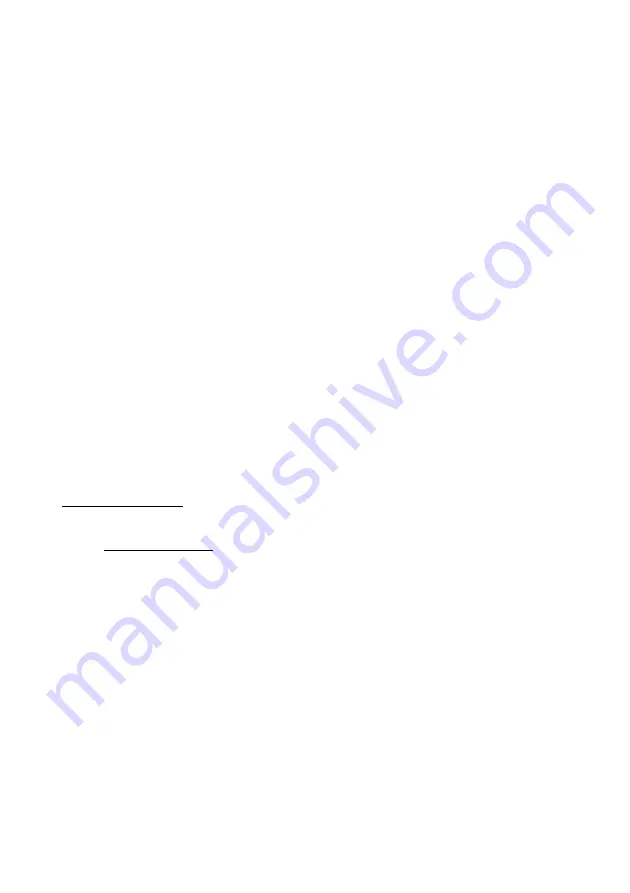
WARNING
ELECTRICAL SHOCK HAZARD
Installing cable connections and servicing this instrument require access to shock
hazard level voltages which can cause death or serious injury.
Disconnect separate or external power sources to relay contacts before
commencing any maintenance.
The electrical installation must be carried out in accordance with CE directions
and/or any other applicable national or local codes.
Unused cable conduit entries must be securely sealed by non-flammable blanking
plates or blind grommets to ensure complete enclosure integrity in compliance with
personal safety and environmental protection requirements.
To ensure safety and correct performance this instrument must be connected to a
properly grounded, three-wire power source.
Proper relay use and configuration is the responsibility of the user.
Do not operate this instrument without the front cover being secured. Refer any
installation, operation or servicing issues to qualified personnel.
Penko is an ETC Company
e-mail: [email protected]