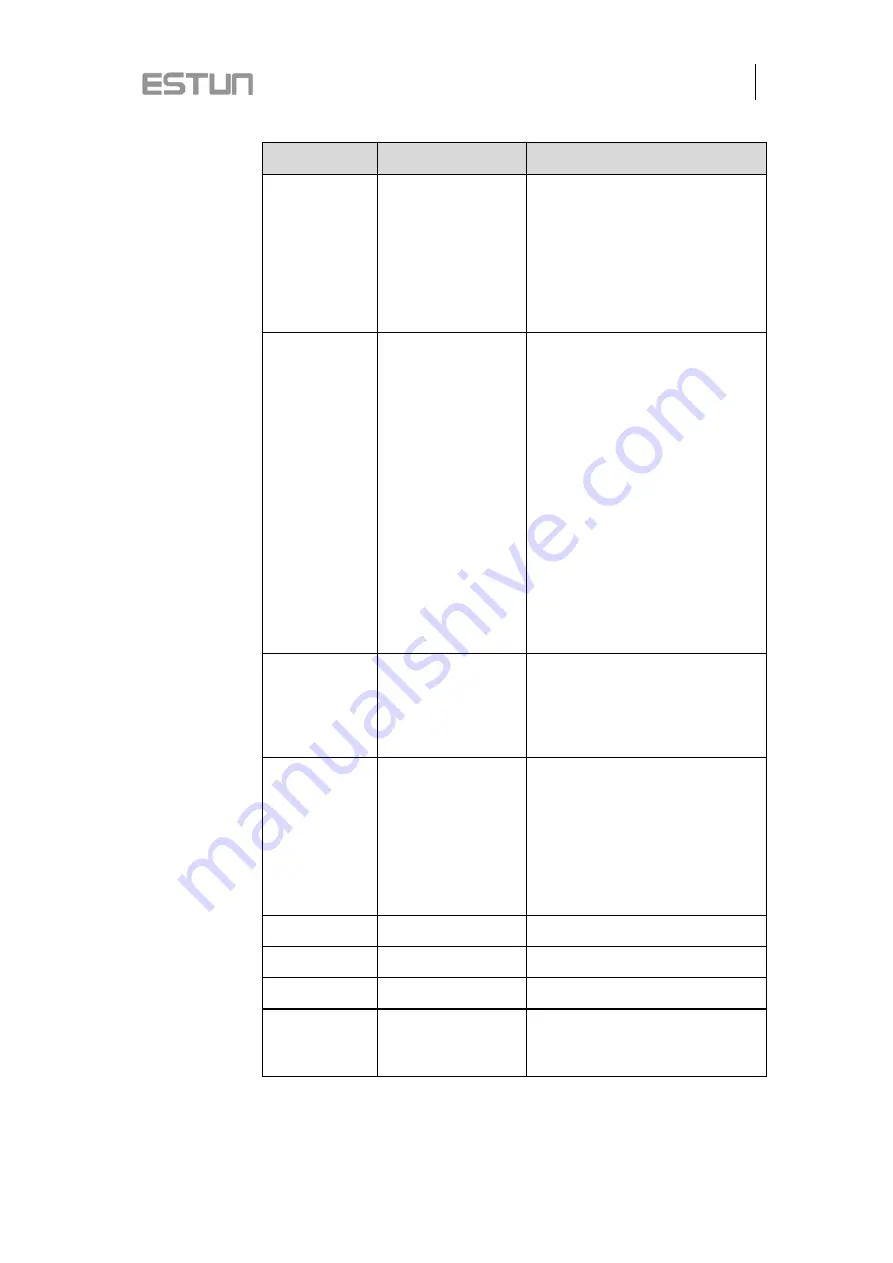
Page 16 of 41
Table 2-3
Definition of external output terminal
Terminal No. Signal
Description
1 START
Step change signal, DC +24V
signal input, connect to upper dead
point signal generally, beam return
to upper dead point, +24V signal is
connected, system receive step
change signal, system callout the
next program and execute the
program.
2 PRESS
Back gauge retraction, signal, DC
+24V signal input, avoid
interfering work piece by gauge
device during work. System X axle
positioning is finished, and slider
gets away from upper dead point.
When slide just press against sheet,
retraction signal is connected.
Back gauge will yield some
distance to direction of up counting
(yield distance is determined by
program retraction value), avoid
interference by back gauge and
work piece. When bending is
finished and slide return, back
gauge will return from yield
position.
3 X-EOT
X-axle reference point signal, DC
+24V signal input, connect to rear
limit signal generally. When gauge
touches reference point switch,
+24V signal is connected.
5 COUNT
Piece counting signal, input
DC+24V signal, and connect to
upper dead point signal generally.
Slider return to upper dead point,
+24V signal is connected, one
count is completed. Then signal
must be connected, otherwise the
system will not operate normally.
6 NC1 Retain
7 MRDY Retain
8 NC2 Retain
9 COM1
Common port of system input
signal must be connected to 0V of
I/O power.
Summary of Contents for E21S
Page 2: ......
Page 4: ......
Page 30: ...Page 30 of 41 Figure 5 8 LCD diagnosis page...
Page 34: ......
Page 41: ...Page 41 of 41 Figure 7 4 Demonstration of AC asynchronism motor wiring...