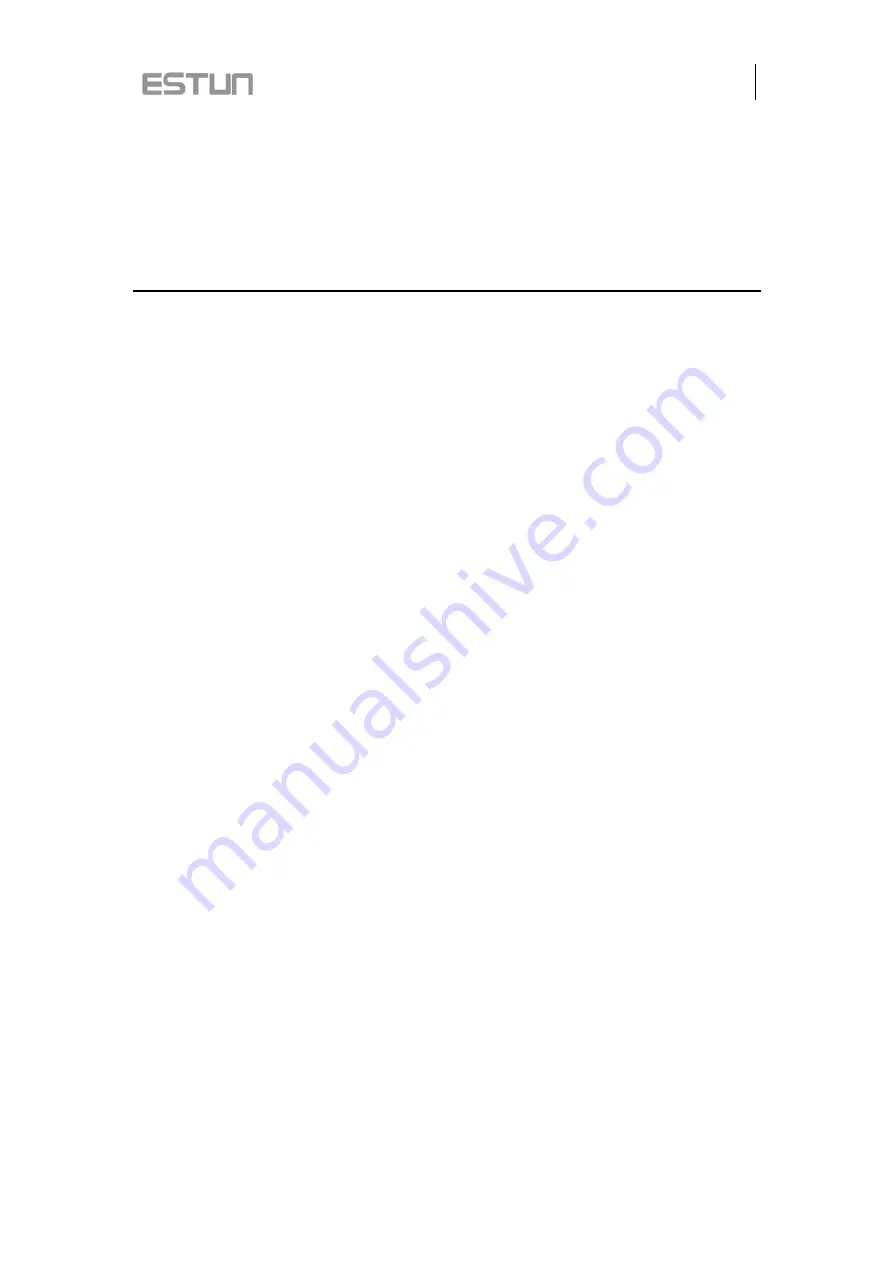
Page 23 of 41
4
Debugging
4.1 Preparation before debugging
Check E21S power line, ground wire, input/output signal wire and
encoder plug for reliable and accurate connection.
Check whether output voltage of 24V switch power is normal or not.
4.2 Debugging procedure
Step 1
Check power supply and ground wire before power on the system.
Step 2
Enter X axle parameter set page respectively, set parameter.
Step 3
Enter diagnostic interface, check system input signal. When there is input
signal, the corresponding input indication is filled; otherwise, input signal is
not connected.
Step 4
Enter diagnostic interface, check system output signal. When there is output
signal, the corresponding output indication is filled. If machine tool fails to
operate normally, check electrical parts of the machine tool.
----End
4.3 Debugging
Step 1
Set up E21S system parameters.
X axle parameter set (Refer to parameter specification for details)
X axle enable: 1 (axle enable is on)
Encoder direction: 1 (Decreasing counting direction)
Reference: 1 (X axle homing is on)
Reference point position: 10.00
Minimum: 10.00 (X axle minimum)
Maximum: 500.00 (X axle maximum, this value is determined by gauge
length)
Multiple factor: 40
Divide factor: 1
Advance stop time: 0.20
Summary of Contents for E21S
Page 2: ......
Page 4: ......
Page 30: ...Page 30 of 41 Figure 5 8 LCD diagnosis page...
Page 34: ......
Page 41: ...Page 41 of 41 Figure 7 4 Demonstration of AC asynchronism motor wiring...