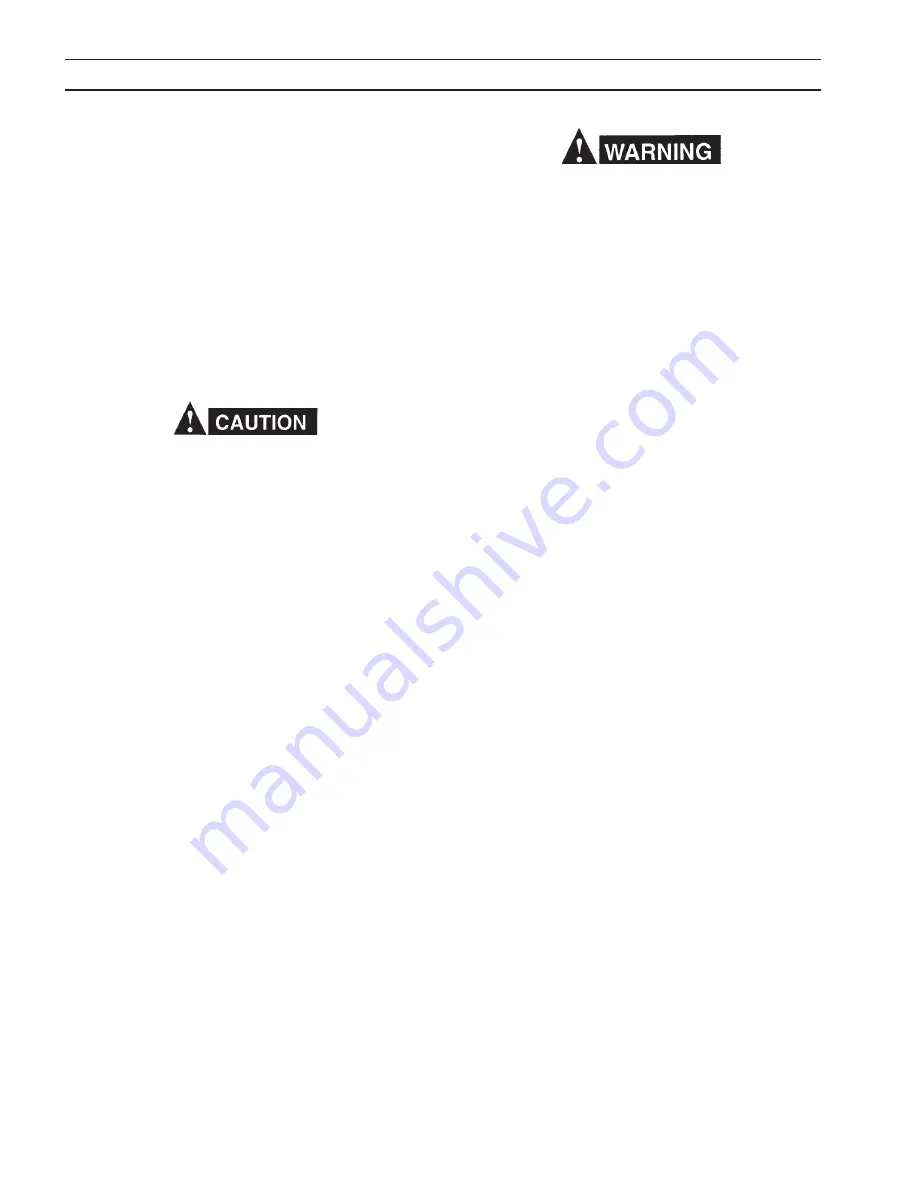
38
5.2.1c transforMer
Occasional blowing out of the dust and dirt from around
the transformer is recommended. This should be done
periodically depending upon the location of the unit and
the amount of dust and dirt in the atmosphere. The welding
machine case cover should be removed and a clean, dry air
stream should be used for this cleaning operation.
5.2.1d WIre feeDer anD control cIrcuIts
The 24-volts circuit is protected by a 10 amp fuse in a panel
mounted fuseholder, accessible from the wire feeder com-
partment. Failure of this fuse will shut off the contactor,
shielding gas and wire feeder.
If it should become necessary to replace this or any other
fuse in the welding machine, ensure that the proper size
fuse is used as a replacement.
5.2.1e oVer-teMperature protectIon
The machine is equipment with a thermostat. On contin-
ued high current application, if the thermostat reaches an
abnormally high temperature, it will deenergize the con-
tactor. This thermostat will reset itself automatically after
the transformer windings have cooled to a safe level. While
deenergized, neither the contactor, shielding gas nor wire
feeder can be operated. If the thermostat opens, allow the
equipment to idle with fan running for approximately 15-
min. before attempting to weld again.
5.2.2 WIre feeDer
When soft wire is fed, the drive rolls may pick up metal from
the wire surface. Accumulation on the rolls may score the wire
with resulting unwanted friction and improper feeding.
Inspect the rolls regularly and clean them with a fine-wire
power brush. Avoid roughening, or removing the hardness of
groove surfaces in grooved rolls. Any roughening may score
the wire, just as the accumulation being removed may do.
5.3 trouBleshootIng
If welding equipment doesn’t work right despite compliance
with checklist inspect as follows:
A. With all power controls ON and other operating
controls at required settings, visually check all
power cables and connections for evidence of
overheating or sparking.
to avoid shock, do not touch electrode wire or parts in
contact with it, or uninsulated cable or connections.
B. Check all gas (and water) hoses and connections,
flowmeters, and regulators for possible sources of
leakage, breakdown or intermittent failure.
C. Isolate trouble to one part of the welding installa-
tion: primary power supply, power source, Feeder or
wire guide train (casing, drive rolls, liners and contact
tip). If this inspection indicates trouble in the Feeder,
use Troubleshooting Guide, Table 5.1 and schematic
diagram.
5.3.1 If Motor Does not run:
A. Check for blown fuse. If blown, check that motor is
not binding before replacing fuse.
B. Check for continuity across speed potentiometer (POT)
and wiper contact. Voltage from center tap to MIN end
should vary from 0 to 5.4 VDC as pot- entiometer is
rotated clockwise.
C. Check wiring for continuity. Then turn power ON and
check for 30 volts d.c. across input terminals 8 and 9
on the feeder printed circuit board connector (PL1).
D. Press torch trigger, and check for voltage across motor
(Pins 4 to 7) of speed control board; should vary from
1 to 24 VDC as speed control potentiometer is rotated
clockwise.
5.3.2 DrIVe roll pressure aDJustMent
Adjust the drive roll pressure knob until no wire slippage
occurs. DO NOT OVERTIGHTEN - EXCESSIVE PRESSURE CAN
CAUSE WIRE FEEDING PROBLEMS.
general replacement
The exploded views in the Parts Section indicate generally,
in numbered parts sequence, the disassembly of the wire
drive and feeder parts.
Reassemble in reverse order.
sectIon 5
serVIce
Summary of Contents for Migmaster 275
Page 4: ...4 TABLE OF CONTENT ...
Page 20: ...20 section 2 INTRODUCTION ...
Page 28: ...28 section 3 INSTALLATION ...
Page 42: ...42 section 5 SERVICE ...
Page 46: ...46 section 6 REPLACEMENT PARTS ...
Page 48: ......
Page 49: ......
Page 50: ......
Page 51: ......
Page 52: ......
Page 53: ......
Page 54: ......
Page 55: ......
Page 56: ......
Page 57: ......