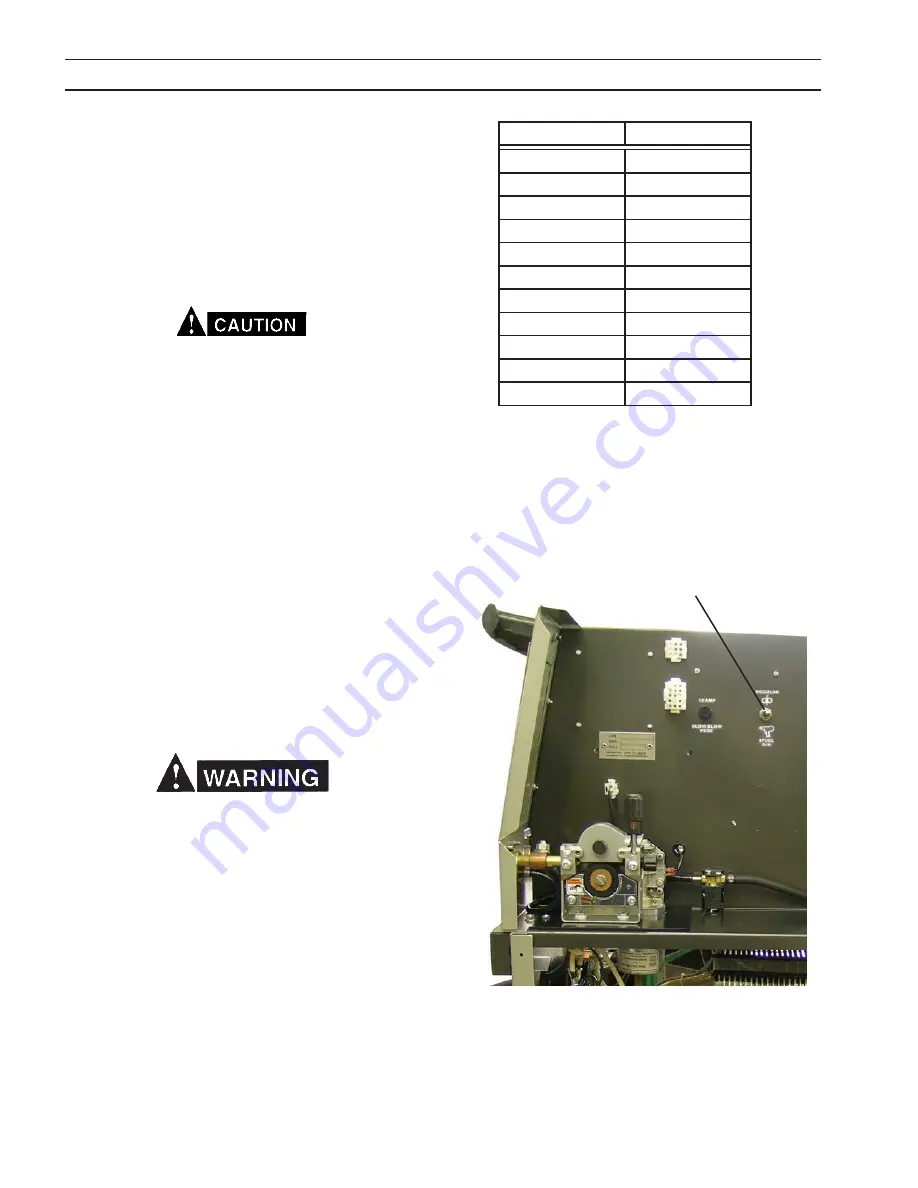
30
The fIne Voltage aDJustMent selector is an eight-
position switch for selecting the exact amount of arc volt-
age (or heat) to be applied to the weld arc. This allows for
fine tuning of the voltage required to stabilze the arc. The
Fine Voltage Selector switch also has an "open" detent at
the six o'clock position. Placing the switch in this position
allows operation of the torch trigger to feed electrode wire
without the wire being electrically "hot". This switch must
not be switched under load.
these tap switches carry several hundred amperes
while welding, and must not be switched under load,
as this will cause the contacts of the switches to arc.
4.1.3 seconDarY WelDIng connectIons
A solid state secondary contactor is used to energize the
welding curcuit. This contactor is activated with the torch
trigger and is energized when the trigger is pulled. The gas
solenoid is energized at the same time. When the trigger
switch is released, the contactor opens and disconnects the
load. The gas valve shuts off when the contactor opens.
The secondary output welding terminals, POS.(+) and NEG(-
), are located on the front panel and are used to set the
welding polarity (D.C.R.P. or D.C.S.P.) (see Fig. 4.1). TORCH
fitting is connected to Positive, and WORK cable/clamp
is connected to Negative output). To weld using D.C.S.P.,
simply mount the WORK cable to the Positive output and
the TORCH fitting cable to the Negative output terminal.
Because of the charged capacitor bank in the second-
ary circuit, the output voltage will take a few seconds
before falling to zero volts.
4.1.4 WIre feeD speeD control
Wire feed speed is controlled by the wire speed potentiom-
eter knob on the front panel. The solid state control allows
for infinitely variable speeds up to 750 IPM.
This wire speed pot is used to set the speed at which the
welding wire is fed out from the torch and hence the welding
amperage. The panel-face numbers on the dial (0-10) are
used for reference and do not directly indicate wire feed
speed; the higher the number, the faster the speed. Table
4.1 show the relationship of wire speed vs. potentiometer
setting.
The fIne Voltage aDJustMent selector is an eight-
position switch for selecting the exact amount of arc volt-
age (or heat) to be applied to the weld arc. This allows for
fine tuning of the voltage required to stabilze the arc. The
Fine Voltage Selector switch also has an "open" detent at
the six o'clock position. Placing the switch in this position
allows operation of the torch trigger to feed electrode wire
without the wire being electrically "hot". This switch must
not be switched under load.
these tap switches carry several hundred amperes
while welding, and must not be switched under load,
as this will cause the contacts of the switches to arc.
4.1.3 seconDarY WelDIng connectIons
A solid state secondary contactor is used to energize the
welding curcuit. This contactor is activated with the torch
trigger and is energized when the trigger is pulled. The gas
solenoid is energized at the same time. When the trigger
switch is released, the contactor opens and disconnects the
load. The gas valve shuts off when the contactor opens.
The secondary output welding terminals, POS.(+) and NEG(-
), are located on the front panel and are used to set the
welding polarity (D.C.R.P. or D.C.S.P.) (see Fig. 4.1). TORCH
fitting is connected to Positive, and WORK cable/clamp
is connected to Negative output). To weld using D.C.S.P.,
simply mount the WORK cable to the Positive output and
the TORCH fitting cable to the Negative output terminal.
Because of the charged capacitor bank in the second-
ary circuit, the output voltage will take a few seconds
before falling to zero volts.
4.1.4 WIre feeD speeD control
Wire feed speed is controlled by the wire speed potentiom-
eter knob on the front panel. The solid state control allows
for infinitely variable speeds up to 750 IPM.
This wire speed pot is used to set the speed at which the
welding wire is fed out from the torch and hence the welding
amperage. The panel-face numbers on the dial (0-10) are
used for reference and do not directly indicate wire feed
speed; the higher the number, the faster the speed. Table
4.1 show the relationship of wire speed vs. potentiometer
setting.
The fIne Voltage aDJustMent selector is an eight-
position switch for selecting the exact amount of arc volt-
age (or heat) to be applied to the weld arc. This allows for
fine tuning of the voltage required to stabilze the arc. The
Fine Voltage Selector switch also has an "open" detent at
the six o'clock position. Placing the switch in this position
allows operation of the torch trigger to feed electrode wire
without the wire being electrically "hot". This switch must
not be switched under load.
these tap switches carry several hundred amperes
while welding, and must not be switched under load,
as this will cause the contacts of the switches to arc.
4.1.3 seconDarY WelDIng connectIons
A solid state secondary contactor is used to energize the
welding curcuit. This contactor is activated with the torch
trigger and is energized when the trigger is pulled. The gas
solenoid is energized at the same time. When the trigger
switch is released, the contactor opens and disconnects the
load. The gas valve shuts off when the contactor opens.
The secondary output welding terminals, POS.(+) and NEG(-
), are located on the front panel and are used to set the
welding polarity (D.C.R.P. or D.C.S.P.) (see Fig. 4.1). TORCH
fitting is connected to Positive, and WORK cable/clamp
is connected to Negative output). To weld using D.C.S.P.,
simply mount the WORK cable to the Positive output and
the TORCH fitting cable to the Negative output terminal.
Because of the charged capacitor bank in the second-
ary circuit, the output voltage will take a few seconds
before falling to zero volts.
4.1.4 WIre feeD speeD control
Wire feed speed is controlled by the wire speed potentiom-
eter knob on the front panel. The solid state control allows
for infinitely variable speeds up to 750 IPM.
This wire speed pot is used to set the speed at which the
welding wire is fed out from the torch and hence the welding
amperage. The panel-face numbers on the dial (0-10) are
used for reference and do not directly indicate wire feed
speed; the higher the number, the faster the speed. Table
4.1 show the relationship of wire speed vs. potentiometer
setting.
Dial setting
Wire speed IpM
0
0
1
30
2
115
3
200
4
300
5
380
6
455
7
525
8
615
9
703
10
760
4.1.5 stanDarD/spool gun selector
This two-position toggle switch is used to select standard
metal inert gas welding (MIG) with the GUNMASTER 250, or
welding with the MT-250SG/ST-23A spool guns.
Dial setting
Wire speed IpM
0
0
1
30
2
115
3
200
4
300
5
380
6
455
7
525
8
615
9
703
10
760
4.1.5 stanDarD/spool gun selector
This two-position toggle switch is used to select standard
metal inert gas welding (MIG) with the GUNMASTER 250, or
welding with the MT-250SG/ST-23A spool guns.
sectIon 4
operatIon
figure 4.2 standard/spool gun selector
Standard / Spool Gun Select Switch
table 4.1 relationship of
wire speed vs. potentiometer setting
Summary of Contents for Migmaster 275
Page 4: ...4 TABLE OF CONTENT ...
Page 20: ...20 section 2 INTRODUCTION ...
Page 28: ...28 section 3 INSTALLATION ...
Page 42: ...42 section 5 SERVICE ...
Page 46: ...46 section 6 REPLACEMENT PARTS ...
Page 48: ......
Page 49: ......
Page 50: ......
Page 51: ......
Page 52: ......
Page 53: ......
Page 54: ......
Page 55: ......
Page 56: ......
Page 57: ......