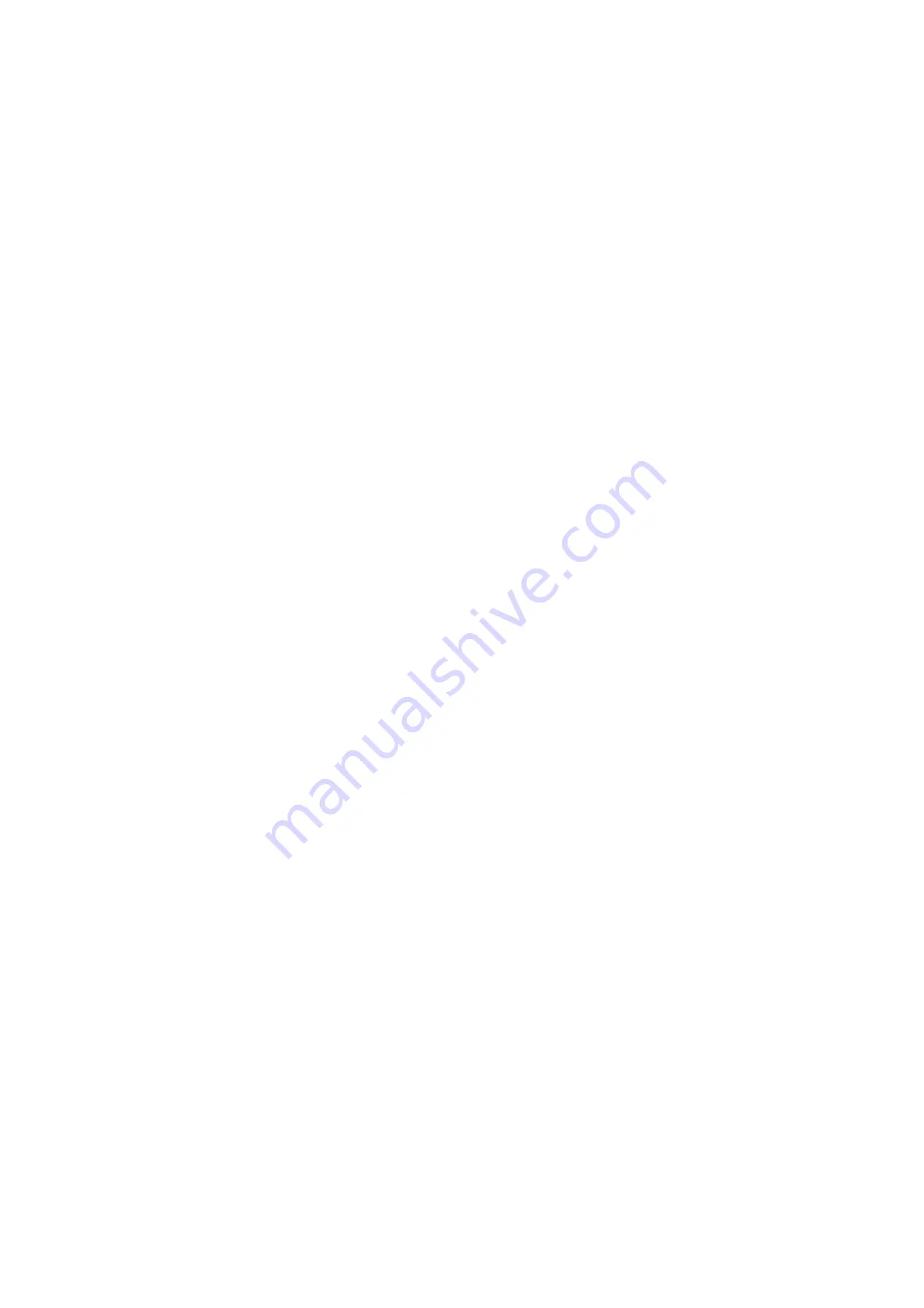
Confidential
Notice:
All rights reserved. No part of this manual may be reproduced, stored in a retrieval system, or transmitted in any form or
by any means, electronic, mechanical, photocopying, recording, or otherwise, without the prior written permission of
SEIKO EPSON CORPORATION.
All effort have been made to ensure the accuracy of the contents of this manual. However, should any errors be
detected, SEIKO EPSON would greatly appreciate being informed of them.
The contents of this manual are subject to change without notice.
The above not withstanding SEIKO EPSON CORPORATION can assume no responsibility for any errors in this
manual or the consequences thereof.
EPSON is a registered trademark of SEIKO EPSON CORPORATION.
Note :Other product names used herein are for identification purpose only and may be trademarks or registered
trademarks of their respective owners. EPSON disclaims any and all rights in those marks.
Copyright
2010
SEIKO EPSON CORPORATION
IJP CS Quality Assurance Department
Summary of Contents for Stylus Photo R3000 Series
Page 1: ...SERVICE MANUAL CONFIDENTIAL Color Inkjet Printer EpsonStylusPhotoR3000 SEMF10 002 ...
Page 8: ...Confidential CHAPTER 1 DISASSEMBLY REASSEMBLY ...
Page 32: ...Confidential CHAPTER 2 ADJUSTMENT ...
Page 64: ...Confidential CHAPTER 3 MAINTENANCE ...