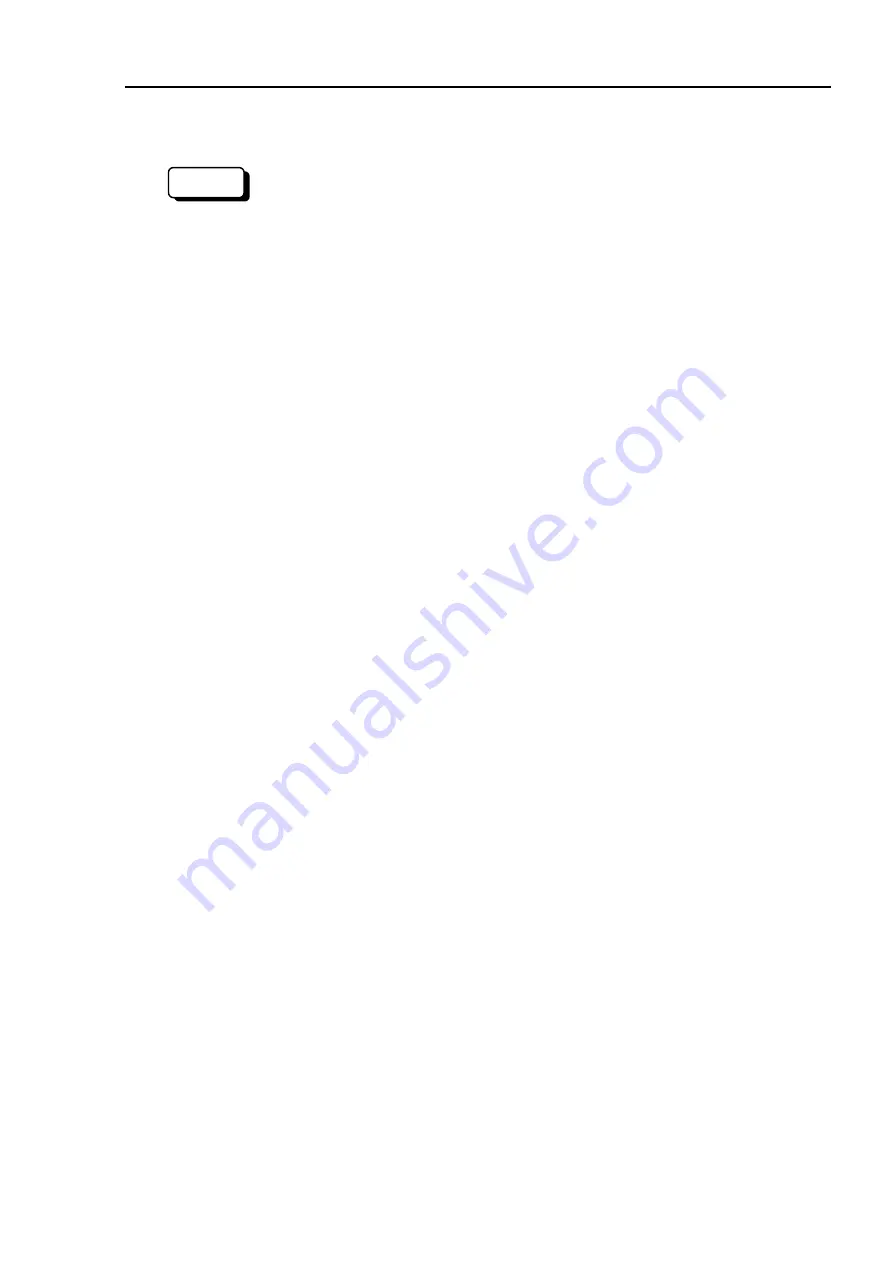
Part 2: Maintenance
11. Calibration
195
Calibrating Axes #1, #2, and #4
Axes #1, #2, and #4 are all calibrated by the same method. Calibrating two or more Axes
at the same time can affect accuracy. For best accuracy, calibrate each axis one at a time.
First, perform steps (1) to (10) in the
Common procedure for calibration
section.
(11) For each axis, select a current teach point that is easy to verify for accuracy, and move
to that point. Because of the error due to origin offset, the same position will not be
obtained. Although the error is less than one revolution of the motors, care should be
taken to avoid interference with surrounding machinery.
One revolution of Axis #1 motor:
±
4.5
°
One revolution of Axis #2 motor:
±
7.2
°
One revolution of Axis #4 motor:
±
22.5
°
We will use P1 in these steps. Move Axis #3 above this point using the JUMP
command.
<Example>
> JUMP P1:Z0
' Set Axis #3 high (Z0) to prevent interference
with surrounding machinery.
(12) Display the number of pulses in this position using the PULSE command and note the
four values.
<Example>
>
PULSE
16000
10000
' Axes #1 and #2 pulses.
0
-10
' Axes #3 and #4 pulses.
(13) Enter the numbers which were noted in step (12) using the CALPLS command.
<Example>
>
CALPLS 16000,10000,0,-10
(14) Use the SFREE command to free the axis being calibrated and Axis #3.
<Example>
> SFREE 1,3
' Axes #1 and #3 can now be moved manually.
(15) Manually move the axis to be calibrated, and determine the proper original position.
When moving Axis #3, move while pushing the brake release button for Axis #3.
(16) Execute the CALIB command for the axis to be calibrated.
<Example>
>
CALIB 1
' Axis #1 is calibrated.
300
Summary of Contents for EL Series
Page 1: ...ES EL series Rev 9 EM019R893F SCARA ROBOT MANIPULATOR MANUAL ...
Page 2: ...MANIPULATOR MANUAL ES EL series Rev 9 ...
Page 12: ...x ...
Page 14: ...2 ...
Page 16: ...1 Manipulator Part Names Part 1 Setup Operation 4 ...
Page 30: ...4 User Wires and Pneumatic Tubes Part 1 Setup Operation 18 ...
Page 42: ...5 End Effectors Part 1 Setup Operation 30 ...
Page 44: ...6 Attaching a Camera Valve and Other Devices Part 1 Setup Operation 32 ...
Page 68: ...8 Motion Range and Robot Coordinates Part 1 Setup Operation 56 ...
Page 70: ...9 Emergency Stop Part 1 Setup Operation 58 ...
Page 80: ...11 Clean Model Part 1 Setup Operation 68 ...
Page 92: ...80 ...
Page 94: ...Maintenance Safety Precautions Part 2 Maintenance 82 ...
Page 104: ...2 Opening the Covers Part 2 Maintenance 92 ...
Page 112: ...3 Replacing the Cable Unit Part 2 Maintenance 100 ...
Page 138: ...5 Replacing the Motors Part 2 Maintenance 126 ...
Page 162: ...6 Replacing the Reduction Gear Units Part 2 Maintenance 150 ...
Page 186: ...9 Replacing the Ball Screw Spline Unit Part 2 Maintenance 174 ...
Page 210: ...11 Calibration Part 2 Maintenance 198 ...
Page 214: ...12 Clean Model Maintenance Part 2 Maintenance 202 ...
Page 224: ...13 Protected Model Maintenance Part 2 Maintenance 212 13 6 Wiring Schematic 2 ...
Page 236: ...14 Maintenance Part Lists Part 2 Maintenance 224 ...