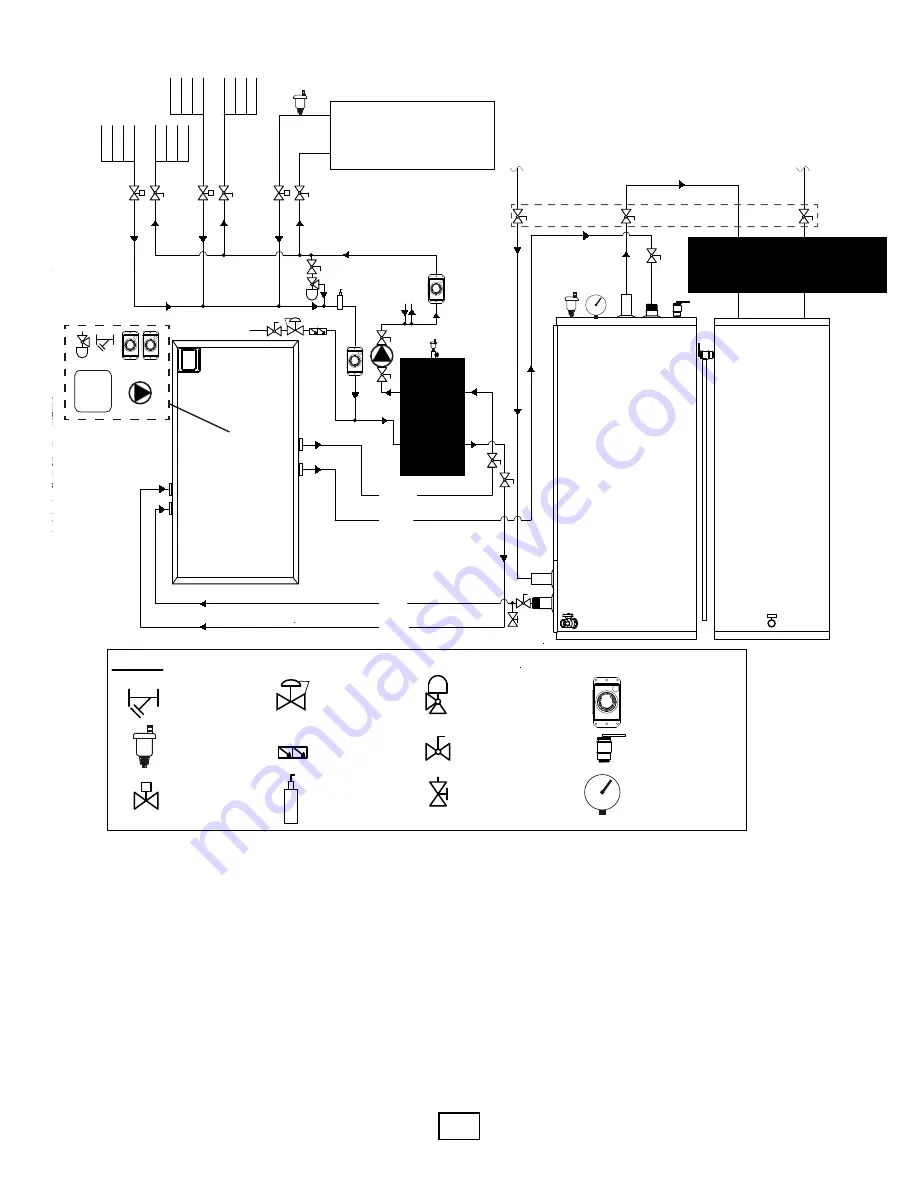
Enertech Global
36
EAV - EME/EMD Rev. A Models
Installation and Operations Manual
WV Installation: Heat & Cool-with Hot Water
OPTIONAL
NON-PRESSURIZED
FLOW CENTER
TO
LOOP
FIELD
FROM
LOOP
FIELD
SOURCE IN
SOURCE OUT
P/T
P/T
P/T
SOURCE IN
SOURCE OUT
TO
LOOP
FIELD
FROM
LOOP
FIELD
FLUSH
VALVE
Type
XXXX
XX-XX XXX
XXXV
~
XX/XXHz
GFXXX
EuP Ready
I1/1
(A)
P1(W)
X.XX
X.XX
XX
XX
Max.
Min.
P/N:XX
XXXXX
PC:XXXX
XX
IP XX
TF XX
Max.
X.XMPa
A
High
Effi
cienc
y
XX
EEI<0.23
NOTE 5
RADIANT
FLOOR
HEATING
ZONE 2
RADIANT
FLOOR
HEATING
ZONE 3
HYDRONIC
AIR HANDLER
ZONE 1
DHW OUT
ΔP
LOAD OUT
NOTE 4
NOTE 7
NOTE 6
TURBOMAX
WATER HEATER
DOMESTIC
HOT
WATER
DOMESTIC
COLD
WATER
HOT
HOT
COLD
COLD
LOAD
IN
LOAD
OUT
BACKUP
ELECTRIC OR GAS
WATER HEATER
(RECOMMENDED)
AUTOMATIC
AIR VENT
3-WAY FLUSH
VALVE
PRESSURE
RELIEF VALVE
PRESSURE
GAUGE
ΔP
LEGEND
WYE STRAINER
ACTUATED
ZONE VALVE
PRESSURE
REDUCING VLV
BACK-FLOW
PREVENTER
AIR ELIMINATOR
DIF. PRESSURE
BYPASS VALVE
ISOLATION BALL
VALVE
BOILER DRAIN
NOTES:
1. INSTALLATION DIAGRAM SHOWN ABOVE IS AN EXAMPLE OF A TYPICAL (RECOMMENDED) INSTALL. ADDITIONAL
ZONES ARE ALLOWED, AS WELL AS ALTERNATE PIPING LAYOUTS.
2. UNIT CONFIGURATION/MODEL INCLUDES INDIRECT DHW TANK.
3.
4.
5.
6.
9.
CLOSELY SPACED TEES FOR CONNECTION TO BACKUP BOILER. SEE FIGURE
15d
FOR DETAILS.
ALWAYS CHECK LOCAL CODE REQUIREMENTS TO ENSURE THAT THE INSTALLATION MEETS CURRENT
REGULATORY STANDARDS.
7. AT HIGHEST POINT IN SYSTEM.
8.
A HOSE KIT HAS BEEN PROVIDED WITH THE UNIT AND SHOULD BE INSTALLED AT THE OUTDOOR UNIT.
AN AUTOMATIC AIR VENT AND AIR SEPARATOR ARE SUPPLIED AS FIELD INSTALLED COMPONENTS.
ALL PIPING MUST BE “HOME RUN” STYLE. ALL RADIANT MANIFOLDS AND AIR HANDLER UNIT ZONE VALVES
SHOULD BE LOCATED IN THE MECHANICAL TO FACILITATE FLUSHING/PURGING OF AIR FROM SYSTEM.
BYPASS VALVE (REQUIRED) IS USED TO AVOID DEAD-HEADING PUMP IF ALL ZONE VALVES ARE CLOSED.
SEE FIGURE
14
FOR DETAILS.
FIELD PROVIDED.
NOTE 6
NOTE 6
NOTE 6
HCT-R4-000-NM
40 GAL.
COMPOSITE
BUFFER TANK
(NOT DRAWN
TO SCALE)
SYSTEM
PUMP
NOTE 8
MAKE-UP
WATER
NOTE 6
BUFFER TANK
REQUIRED IF ANY
FAN COIL/AIR
HANDLER ZONES
ARE SMALLER
THAN 2 TONS.
NOTE 6
NOTE 6
HYDRONIC
AIR HANDLER
ZONE 1
LOAD IN
DHW IN
NOTE 6
ΔP
Expan.
Tank
FACTORY INSTALLED
INTERNAL TO UNIT
INDOOR UNIT
NOTE 6
WV Installation: Heat & Cool-with Hot Water
OPTIONAL
NON-PRESSURIZED
FLOW CENTER
TO
LOOP
FIELD
FROM
LOOP
FIELD
SOURCE IN
SOURCE OUT
P/T
P/T
P/T
SOURCE IN
SOURCE OUT
TO
LOOP
FIELD
FROM
LOOP
FIELD
FLUSH
VALVE
Type
XXXX
XX-XX XXX
XXXV
~
XX/XXHz
GFXXX
EuP Ready
I
1/1
(A)
P
1
(W)
X.XX
X.XX
XX
XX
Max.
Min.
P/N:XX
XXXXX
PC:XXXX
XX
IP XX
TF XX
Max.
X.XMPa
A
High
Effi
cienc
y
XX
EEI<0.23
NOTE 5
RADIANT
FLOOR
HEATING
ZONE 2
RADIANT
FLOOR
HEATING
ZONE 3
HYDRONIC
AIR HANDLER
ZONE 1
DHW OUT
ΔP
LOAD OUT
NOTE 4
NOTE 7
NOTE 6
TURBOMAX
WATER HEATER
DOMESTIC
HOT
WATER
DOMESTIC
COLD
WATER
HOT
HOT
COLD
COLD
LOAD
IN
LOAD
OUT
BACKUP
ELECTRIC OR GAS
WATER HEATER
(RECOMMENDED)
AUTOMATIC
AIR VENT
3-WAY FLUSH
VALVE
PRESSURE
RELIEF VALVE
PRESSURE
GAUGE
ΔP
LEGEND
WYE STRAINER
ACTUATED
ZONE VALVE
PRESSURE
REDUCING VLV
BACK-FLOW
PREVENTER
AIR ELIMINATOR
DIF. PRESSURE
BYPASS VALVE
ISOLATION BALL
VALVE
BOILER DRAIN
NOTES:
1. INSTALLATION DIAGRAM SHOWN ABOVE IS AN EXAMPLE OF A TYPICAL (RECOMMENDED) INSTALL. ADDITIONAL
ZONES ARE ALLOWED, AS WELL AS ALTERNATE PIPING LAYOUTS.
2. UNIT CONFIGURATION/MODEL INCLUDES INDIRECT DHW TANK.
3.
4.
5.
6.
9.
CLOSELY SPACED TEES FOR CONNECTION TO BACKUP BOILER. SEE FIGURE
15d
FOR DETAILS.
ALWAYS CHECK LOCAL CODE REQUIREMENTS TO ENSURE THAT THE INSTALLATION MEETS CURRENT
REGULATORY STANDARDS.
7. AT HIGHEST POINT IN SYSTEM.
8.
A HOSE KIT HAS BEEN PROVIDED WITH THE UNIT AND SHOULD BE INSTALLED AT THE OUTDOOR UNIT.
AN AUTOMATIC AIR VENT AND AIR SEPARATOR ARE SUPPLIED AS FIELD INSTALLED COMPONENTS.
ALL PIPING MUST BE “HOME RUN” STYLE. ALL RADIANT MANIFOLDS AND AIR HANDLER UNIT ZONE VALVES
SHOULD BE LOCATED IN THE MECHANICAL TO FACILITATE FLUSHING/PURGING OF AIR FROM SYSTEM.
BYPASS VALVE (REQUIRED) IS USED TO AVOID DEAD-HEADING PUMP IF ALL ZONE VALVES ARE CLOSED.
SEE FIGURE
14
FOR DETAILS.
FIELD PROVIDED.
NOTE 6
NOTE 6
NOTE 6
HCT-R4-000-NM
40 GAL.
COMPOSITE
BUFFER TANK
(NOT DRAWN
TO SCALE)
SYSTEM
PUMP
NOTE 8
MAKE-UP
WATER
NOTE 6
BUFFER TANK
REQUIRED IF ANY
FAN COIL/AIR
HANDLER ZONES
ARE SMALLER
THAN 2 TONS.
NOTE 6
NOTE 6
HYDRONIC
AIR HANDLER
ZONE 1
LOAD IN
DHW IN
NOTE 6
ΔP
Expan.
Tank
FACTORY INSTALLED
INTERNAL TO UNIT
INDOOR UNIT
NOTE 6
Figure 12c: Piping Diagram - Indoor Module with Buffer Tank
1.
Installation diagram shown above is n example of a typical (recommended) install. Additional zones are allowed, as well as
alternative piping layouts.
2.
Unit configurations/model includes indirect DHW tank.
3.
A flex tubing kit has been provided with the unit and should be installed at the outdoor unit. An automatic air vent and air
separator are supplied as field installed components.
4.
All piping must be “Home Run” style. All radiant manifolds and air handler unit zones valves should be located in the mechanical
room to facilitate flushing/purging of air from system.
5.
Bypass valve (required) is used to avoid dead-heading pump if all zone valves are closed. See
Figure 11
for details.
6.
Field Provided
7.
At highest point in the system.
8.
Closely spaced tees for connection to backup boiler. See
Figure 12d
for details
9.
Always check local code requirements to ensure that the installation meets current regulatory standards.
Piping Diagram - Indoor Module with Buffer Tank
Section 6: Unit Piping Installation
BACKUP ELECTRIC OR
GAS WATER HEATER
(STRONGLY
RECOMMENDED
FOR RESIDENTIAL
APPLICATIONS)
TURBOMAX
WATER HEATER
⚠
WARNING
⚠
SEE FIGURE 12E FOR
PIPING PRECAUTIONS