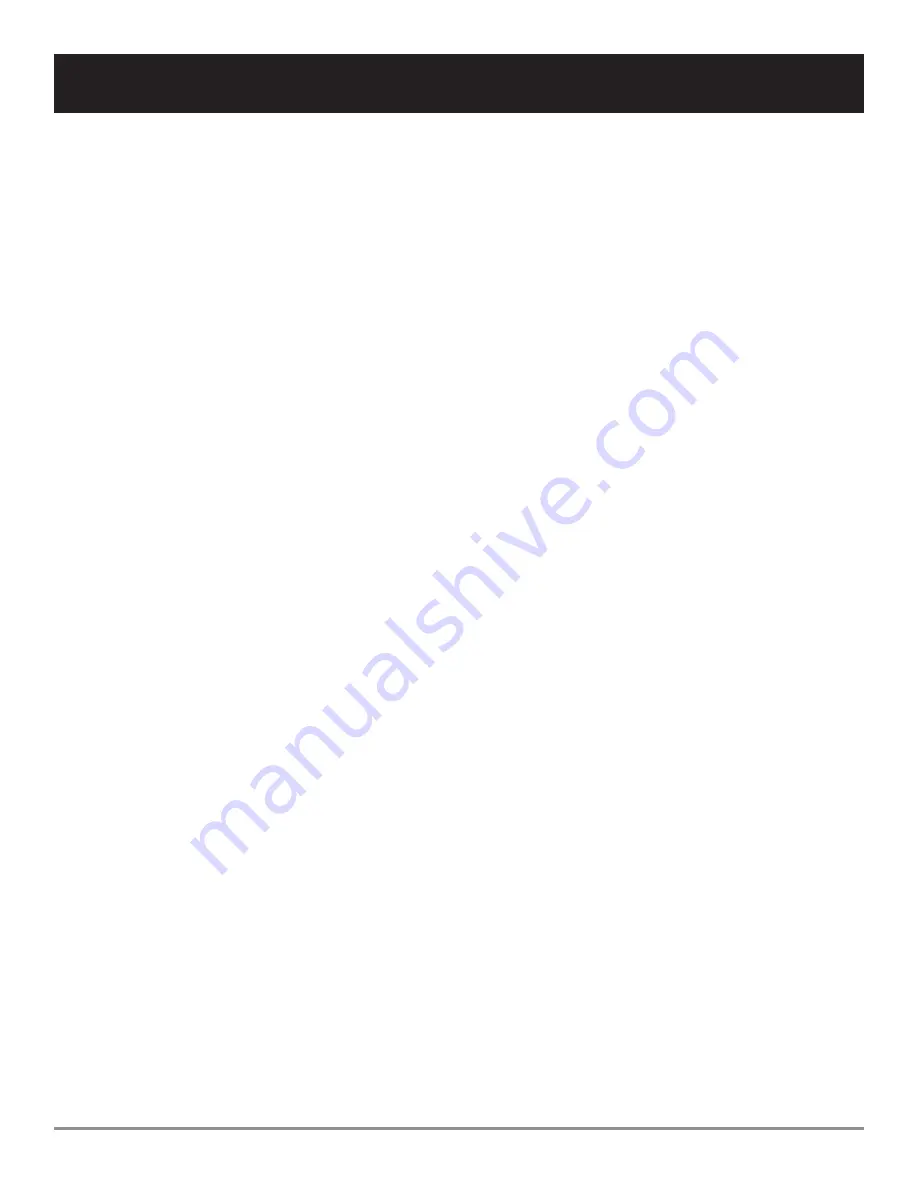
33858-1-0615
Page 23
If the gas quality is bad, your burner may not stay lit, the burners may produce soot and the fireplace may backfire when lit. If
the gas quality or pressure is low, contact your local gas supplier immediately.
1. When power button is pressed, there is no spark.
a. Ignitor electrode not connected to ignitor cable -
Reconnect ignitor cable.
b. Ignitor cable pinched or wet. Keep ignitor cable dry -
Free ignitor cable if pinched by any metal or tubing.
c. Broken ignitor cable - Replace ignitor cable.
d. Ignitor electrode positioned wrong - Replace ignitor.
e. Ignitor electrode is broken - Replace ignitor.
2. Appliance produces odors.
a. Appliance burning vapors from paint, hair spray, glues,
etc. - Ventilate area. Stop using odor-causing products
while fireplace is running.
b. Gas leak - Locate and correct all leaks.
3. Appliance shuts off during use.
a. Low batteries - Replace batteries in remote receiver.
b. Low line pressure - Check line pressure to the valve.
c. Defective sensor - Replace.
4. Gas odor even when control knob is in OFF position.
a. Gas leak - Locate and correct all leaks.
b. Control valve defective - Replace control valve.
5. When switch is "ON," there is spark, but no ignition.
a. Gas supply turned off or manual shutoff valve closed -
Turn on gas supply or open manual shutoff valve.
b. Control knob not in PILOT position - Turn control knob to
PILOT position. (Millivolt fireplaces)
c. Control knob not pressed in while in PILOT position -
Press in control knob while in PILOT position. (Millivolt
fireplaces)
d. Air in gas lines when installed - Continue holding down
control knob. Repeat ignition operation until air is
removed and pilot light ignites.
6. Burner flame goes out when control knob is released.
a. Control knob not fully pressed in - Press in control knob
fully.
b. Control knob not pressed in long enough - After pilot
lights, keep control knob pressed in 30 seconds.
c. Manual Shutoff valve not fully open - Fully open manual
shutoff valve.
d. Thermocouple connection loose at control valve - Hand
tighten until snug, then tighten with wrench 1/4 turn
more.
e. Pilot flame not touching thermocouple, which allows
thermocouple to cool, causing pilot flame to go out. This
problem could be caused by either low gas pressure
or dirty or partially clogged pilot - Contact local gas
company.
f. Thermocouple damaged - Replace thermocouple.
g. Control valve damaged - Replace control valve.
7. Burner does not light.
a. Burner orifice clogged - Clean burner or replace main
burner orifice.
b. Burner orifice diameter is too small - Replace burner
orifice.
c. Inlet gas pressure is too low - Contact qualified service
person.
d. Low batteries - replace batteries in remote receiver and
transmitter.
8. If burning at main burner orifice occurs (a loud, roaring
blow torch noise).
a. Turn off burner assembly and contact a qualified service
person.
b. Manifold pressure is too low - Contact local gas
company.
c. Burner orifice clogged - Clean burner or replace burner
orifice.
9. Logs appear to smoke after initial operation.
a. Vapors from paint or curing process of logs - Problem
will stop after a few hours of operation.
b. If problem persists turn off fireplace and call a qualified
service person.
10. Appliance whistles when main burner is lit.
a. Main burner is cold - Turn control knob to LOW and let
warm up for several minutes.
b. Air in gas line - Operate burner until air is removed from
line. Have gas line checked by local gas company.
c. Dirty or partially clogged burner orifice - Clean burner or
replace burner orifice.
11. Unit won't light due to damp or wet ignitor.
a. For damp or wet conditions, it may be necessary to dry
the ignitor. To do this push the HI and LO flame buttons
in and hold for two to three minutes then release. Light
the fireplace as usual.
12. Burner fluctuates between HI and LO at startup with no
command from the remote.
a. Set the burner to HI. After five minutes, set the burner to
LO.
Turn appliance OFF and allow to cool before servicing. Only a qualified service person should service and repair the fireplace.
TROUBLESHOOTING
SYMPTOMS - POSSIBLE CAUSES AND CORRECTIONS