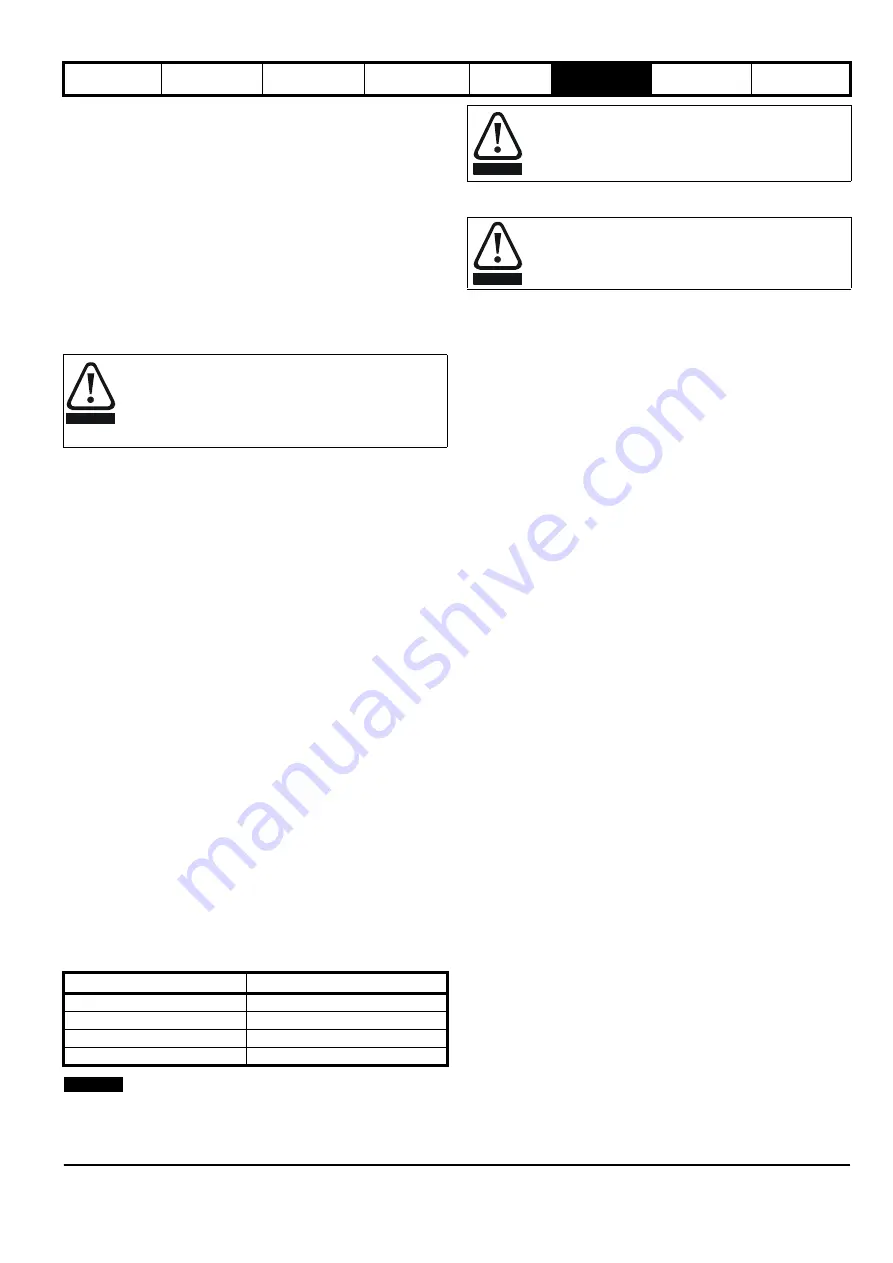
Unidrive M / Unidrive HS Modular Installation Guide
105
Issue Number: 5
6.10.5
Υ
/
Δ
motor operation
The voltage rating for
Υ
and
Δ
connections of the motor should always
be checked before attempting to run the motor.
The default setting of the motor rated voltage parameter is the same as
the drive rated voltage, i.e.
400 V drive 400 V rated voltage
A typical 3 phase motor would be connected in
Υ
for 400 V operation or
Δ
for 200 V operation, however, variations on this are common e.g.
Υ
690 V
Δ
400 V
Incorrect connection of the windings will cause severe under or over
fluxing of the motor, leading to a very poor output torque or motor
saturation and overheating respectively.
6.10.6 Output contactor
A contactor is sometimes required to be installed between the drive and
motor for safety purposes.
The recommended motor contactor is the AC3 type.
Switching of an output contactor should only occur when the output of
the drive is disabled.
Opening or closing of the contactor with the drive enabled will lead to:
1.
OI.AC trips (which cannot be reset for 10 seconds)
2. High levels of radio frequency noise emission
3. Increased contactor wear and tear
The Drive Enable (terminal 31 on
Unidrive M700 / M701 / HS70 / HS71
and terminal 11 and 13 on
Unidrive M702 / HS72
) when opened
provides a Safe Torque Off function. This can in many cases replace
output contactors. For further information see the
Control User Guide.
6.11 Braking
Braking occurs when the drive is decelerating the motor, or is preventing
the motor from gaining speed due to mechanical influences. During
braking, energy is returned to the drive from the motor.
When the motor is being braked by the drive, the maximum regenerated
power that the drive can absorb is equal to the power dissipation
(losses) of the drive.
When the regenerated power is likely to exceed these losses, the DC
bus voltage of the drive increases. Under default conditions, the drive
brakes the motor under PI control, which extends the deceleration time
as necessary in order to prevent the DC bus voltage from rising above a
user defined set-point.
If the drive is expected to rapidly decelerate a load, or to hold back an
overhauling load, a braking resistor must be installed.
Table 6-20 shows the DC voltage level at which the drive turns on the
braking transistor.
Table 6-20 Braking transistor turn on voltage
N
When a braking resistor is used, Pr
00.015
should be set to FASt ramp
mode.
6.11.1 External braking resistor
When a braking resistor is to be mounted outside the enclosure, ensure
that it is mounted in a ventilated metal housing that will perform the
following functions:
•
Prevent inadvertent contact with the resistor
•
Allow adequate ventilation for the resistor
When compliance with EMC emission standards is required, external
connection requires the cable to be armored or shielded, since it is not
fully contained in a metal enclosure. See section 6.13.4
on page 113 for further details.
Internal connection does not require the cable to be armored or
shielded.
If the cable between the drive and the motor is to be
interrupted by a contactor or circuit breaker, ensure that the
drive is disabled before the contactor or circuit breaker is
opened or closed. Severe arcing may occur if this circuit is
interrupted with the motor running at high current and low
speed.
Drive voltage rating
DC bus voltage level
200 V
390 V
400 V
780 V
575 V
930 V
690 V
1120 V
WARNING
WARNING
NOTE
High temperatures
Braking resistors can reach high temperatures. Locate
braking resistors so that damage cannot result. Use cable
having insulation capable of withstanding high temperatures.
Overload protection
When an external braking resistor is used, it is essential that
an overload protection device is incorporated in the braking
resistor circuit; this is described in Figure 6-21 on page 106.
WARNING
WARNING
WARNING
WARNING
Summary of Contents for unidrive m
Page 157: ......
Page 158: ...0478 0141 05 ...