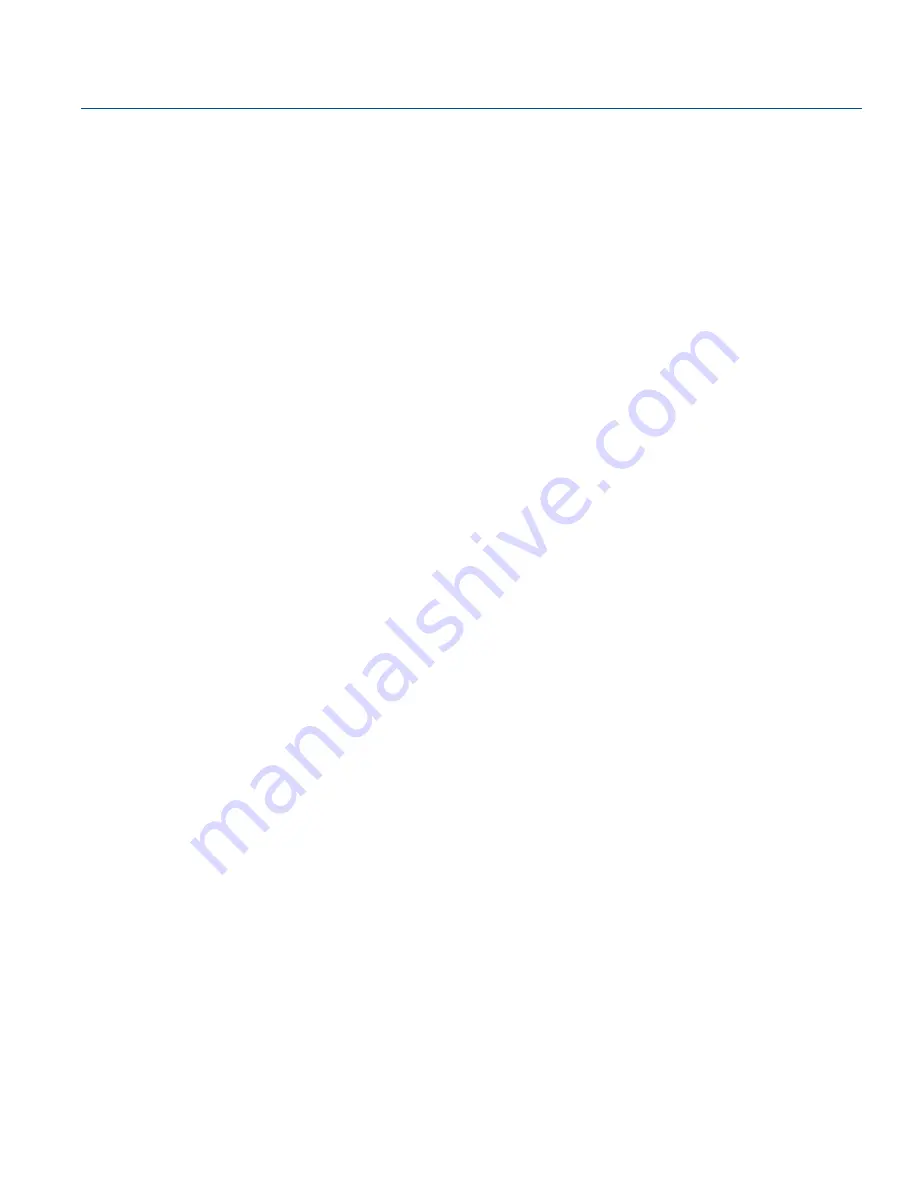
22
Reference Manual
00809-0100-4808, Rev DA
Transmitter Functions
October 2016
Transmitter Functions
2.12.12
Compensating Rosemount 3051N Range 4 and 5 Differential
Transmitters for line pressure
Rosemount 3051N Range 4 and Range 5 Pressure Transmitters require a special calibration procedure
when used in differential pressure applications. The purpose of this procedure is to optimize transmitter
performance by reducing the effect of static line pressure (P
s
) in these applications. Rosemount 3051N
Differential Pressure Transmitter ranges 0, 1, 2, and 3 do not require this procedure because the
optimization occurs in the sensor. See
“Static pressure effect” on page 43
for additional details.
Applying high static pressure to Rosemount 3051N Range 4 and Range 5 Pressure Transmitters causes a
systematic shift in the output. This shift is linear with static pressure; correct it by performing the
“Full
trim” on page 19
, after determining the corrected input values as noted below.
The following specifications show the static pressure effect for Rosemount 3051N Range 4 and Range 5
Transmitters used in differential pressure applications:
Zero effect
±0.1% of the upper range limit per 1000 psi (6,9 MPa) for line pressures (P
s
) from 0 to 2000 psi (0 to
13,8 MPa)
±[0.2 + 0.2 (P
s
-2000) / 1000]% of the upper range limit per 1000 psi (6,9 MPa) for line pressures above
2000 psi (13,8 MPa) and
3626 psi (25 MPa)
Span effect
Correctable to ±0.2% of reading per 1000 psi for line pressures from 0 to 3626 psi.
The systematic span shift caused by the application of static line pressure is –1.00% of input reading per
1000 psi for Rosemount 3051N Range 4 transmitters, and –1.25% of reading per 1000 psi for Range 5
transmitters.
Use the following example to compute corrected input values.
Example
A Rosemount 3051ND4 Transmitter will be used in a differential pressure application where the static
line pressure is 1200 psi. The transmitter is ranged so the output is 4 mA at 500 inH
2
O and 20 mA at
1500 inH
2
O.
To correct for systematic error caused by high static line pressure, first use the following formulas to
determine corrected values for the low trim and high trim.
LT
c
= LRV + S (LRV) P
s
HT
c
= URV + S (URV) P
s
Where:
LT
c
=
Corrected Low Trim Value
LRV =
Lower Range Value
S =
–(Systematic Span shift per specification)
P
s
=
Static Line Pressure
Where:
HT
c
=
Corrected High Trim Value
URV =
Upper Range Value
S =
–(Span shift per specification)
P
s
=
Static Line Pressure