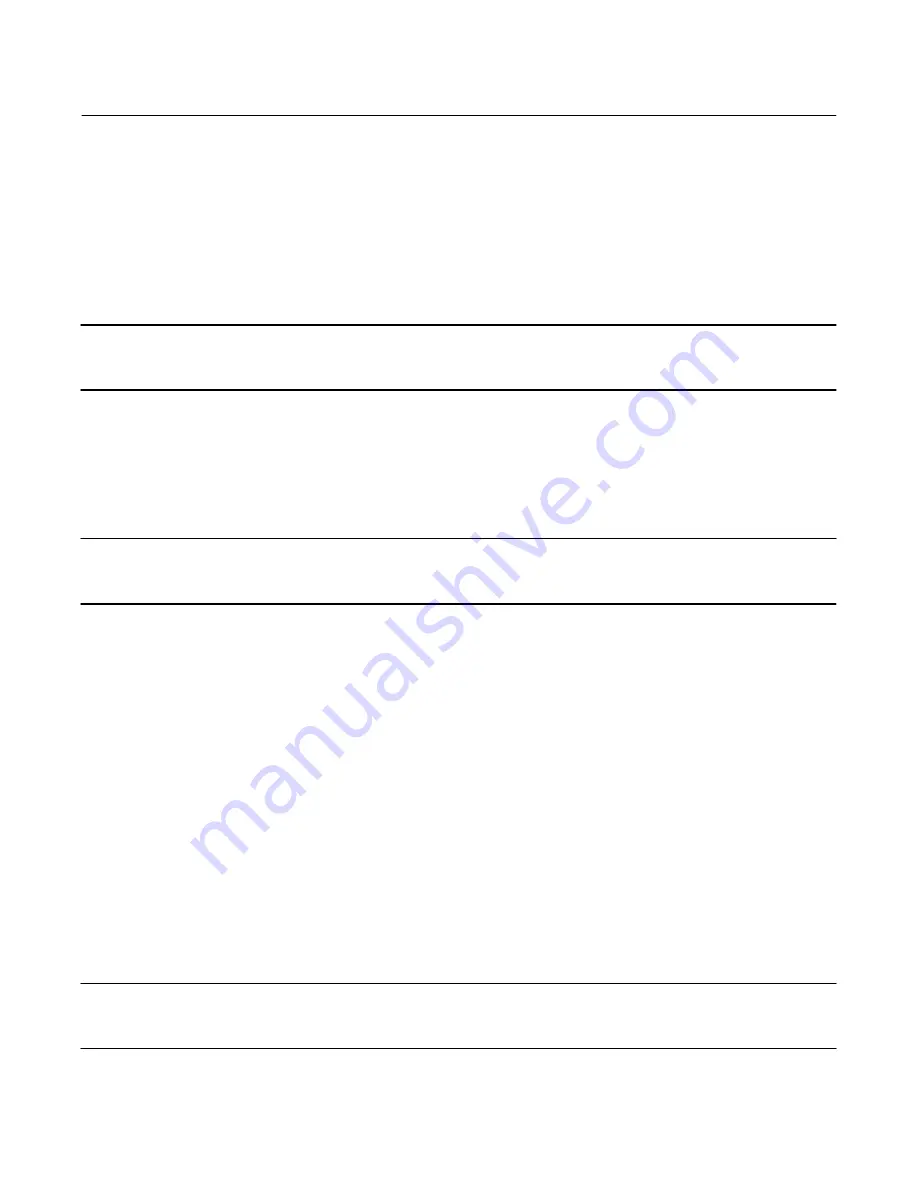
Instruction Manual
D200160X012
4195K Controllers
July 2018
33
10. Loosen the remote set point zero adjustment locking screw and adjust the remote set point zero adjustment screw
to correct for half the error at mid scale. Tighten the zero adjustment locking screw.
11. Apply remote set point pressure equal to the lower and upper range limits and make sure the set point indicator is
within
±
1 percent.
12. If necessary, perform the process indicator zero and span calibration procedure in this section. Otherwise, perform
the flapper alignment procedure in this section.
Flapper Alignment
Note
Perform the process indicator zero and span calibration procedure and, for controllers with remote set point (suffix letter M), the
remote set point zero and span calibration procedure before the flapper alignment.
Flapper leveling screw numbers and adjustments are shown in figure 4‐3. Key number locations are shown in
figure 7‐1.
Provide a means of measuring the controller output pressure by connecting the controller output to a pressure gauge
(open‐loop conditions must exist). Do not apply supply pressure at this time.
Note
4195KB and KC controllers with anti‐reset windup (suffix letter F) are supplied with two O‐rings (key 52), valve cover (key 51), and
two machine screws (key 53). Use these parts in the next step.
1. For controllers with anti‐reset windup (suffix letter F), record the direction of the arrow on the anti‐reset windup
relief valve (key 55). Remove the relief valve and install the two O‐rings (key 52) and valve cover (key 51) supplied
with the controller. Secure the valve cover with the two machine screws (key 53) provided.
2. If necessary, remove the two machine screws (key 6) and lift off the proportional band indicator cover (key 36).
3. If the controller has the external feedback option (available with the 4195KB only), connect the controller output to
4. Provide regulated supply pressure to the controller. Do not exceed the normal operating pressure in table 1‐6.
5. For a controller with manual set point, move the set point indicator to the mid‐scale mark on the process scale. For
a controller with remote set point (suffix letter M), adjust the remote set point pressure until the set point indicator
is at the mid‐scale mark on the process scale.
6. Set the reset adjustment to 0.01 minutes per repeat.
7. If the controller has rate (4195KC controllers), turn the rate adjustment to OFF.
8. Apply process pressure equal to the mid‐scale value of the process scale span. If pressure is not available to pressure
the input element to mid‐scale value, an alternate method is to disconnect link number 1 at the input element and
tape the process pointer at mid‐scale mark on the process scale. If the controller has a capsular input element, note
the hole where link number 1 is connected to the input element, then disconnect link 1. This method should only be
used if pressure is not available to pressure the input element to the mid‐scale value.
Note
Because of the high controller gain, the controller output will not remain stable in steps 9 through 13. The controller output gauge
is adequate to check the output pressure during this procedure.