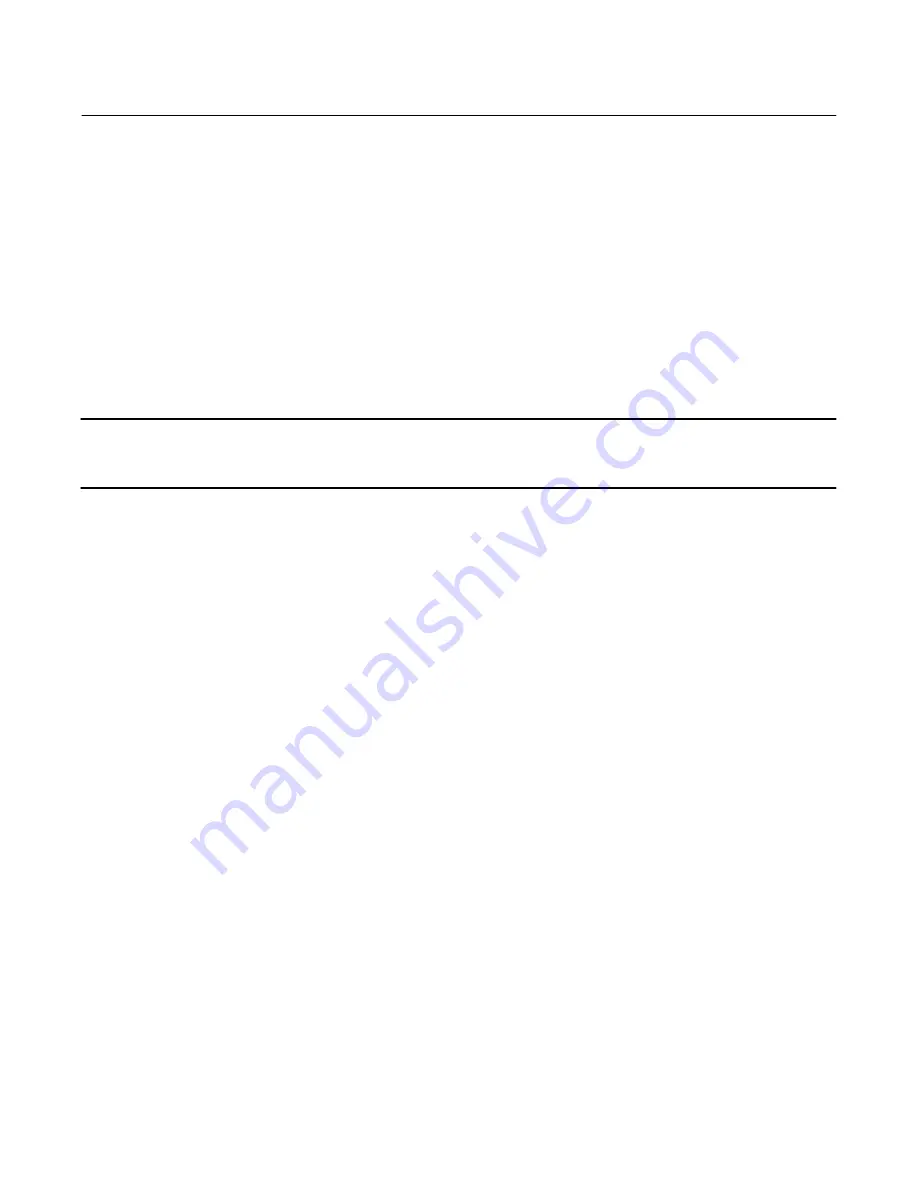
Instruction Manual
D200160X012
4195K Controllers
July 2018
22
9. Make sure the set point indicator is within
±
1 percent of the mid‐scale mark and if so, proceed to step 12. If the set
point indicator is not within 1 percent, but is within
±
2 percent of the mid‐scale mark, then proceed with step 10. If
the set point indicator is not within
±
2 percent, proceed to the remote set point calibration procedure in the
Maintenance section.
10. Loosen the remote set point zero adjustment locking screw and adjust the remote set point zero adjustment screw
to correct for half the error at mid‐scale. Tighten the zero adjustment locking screw.
11. Apply remote set point pressure equal to the lower and upper range limits and make sure the set point indicator is
within
±
1 percent.
12. If necessary, perform the process indicator zero and span calibration procedure in this section. Otherwise, perform
the flapper alignment procedure in this section.
Flapper Alignment
Note
Perform the process indicator zero and span calibration procedure and, for controllers with remote set point (suffix letter M), the
remote set point zero and span calibration procedure before the flapper alignment.
Flapper leveling screw numbers and adjustments are shown in figure 3‐3. Key number locations are shown in figure
7‐1.
Provide a means of measuring the controller output pressure by connecting the controller output to a pressure gauge
(open‐loop conditions must exist). Provide a regulated supply pressure to the controller. Do not exceed the normal
operating pressure in table 1‐6. After performing the flapper alignment procedure, go to the startup procedure.
1. For a controller with manual set point, move the set point indicator to the mid‐scale mark on the process scale. For
a controller with remote set point (suffix letter M), adjust the remote set point pressure until the set point indicator
is at the mid‐scale mark on the process scale.
2. Apply process pressure equal to the mid‐scale value of the process scale span. If pressure is not available to pressure
the input element to the mid‐scale value, an alternate method is to disconnect link number 1 at the input element
and tape the process pointer at the mid‐scale mark on the process scale. If the controller has a capsular input
element, note the hole from which link number 1 was removed for proper replacement. This method should only be
used if pressure is not available to pressure the input element to the mid‐scale value.
3. Remove the two machine screws (key 6) and lift off the proportional band indicator cover (key 36).
4. Adjust the proportional band between DIRECT and REVERSE.
5. The controller output should be 0.62
±
0.007 bar (9
±
0.10 psig) for a 0.2 to 1.0 bar (3 to 15 psig) output or 1.2
±
0.01
bar (18
±
0.2 psig) for a 0.4 to 2.0 bar (6 to 30 psig) output. If not, adjust flapper leveling screw 2 (the screw nearest
the nozzle) until the output is within tolerance.
6. Set the proportional band to 30 percent DIRECT.
7. The controller output should be 0.62
±
0.02 bar (9
±
0.25 psig) or 1.2
±
0.04 bar (18
±
0.5 psig). If not, adjust flapper
leveling screw 3 (the screw nearest the nozzle).
8. Set the proportional band to 30 percent REVERSE.
9. The controller output should be 0.62
±
0.02 bar (9
±
0.25 psig) or 1.2
±
0.04 bar (18
±
0.5 psig). If not, adjust flapper
leveling screw 1 (the screw nearest the nozzle).
adjustments.
11. If link 1 was disconnected, remove the tape and reconnect link 1 to the input element.