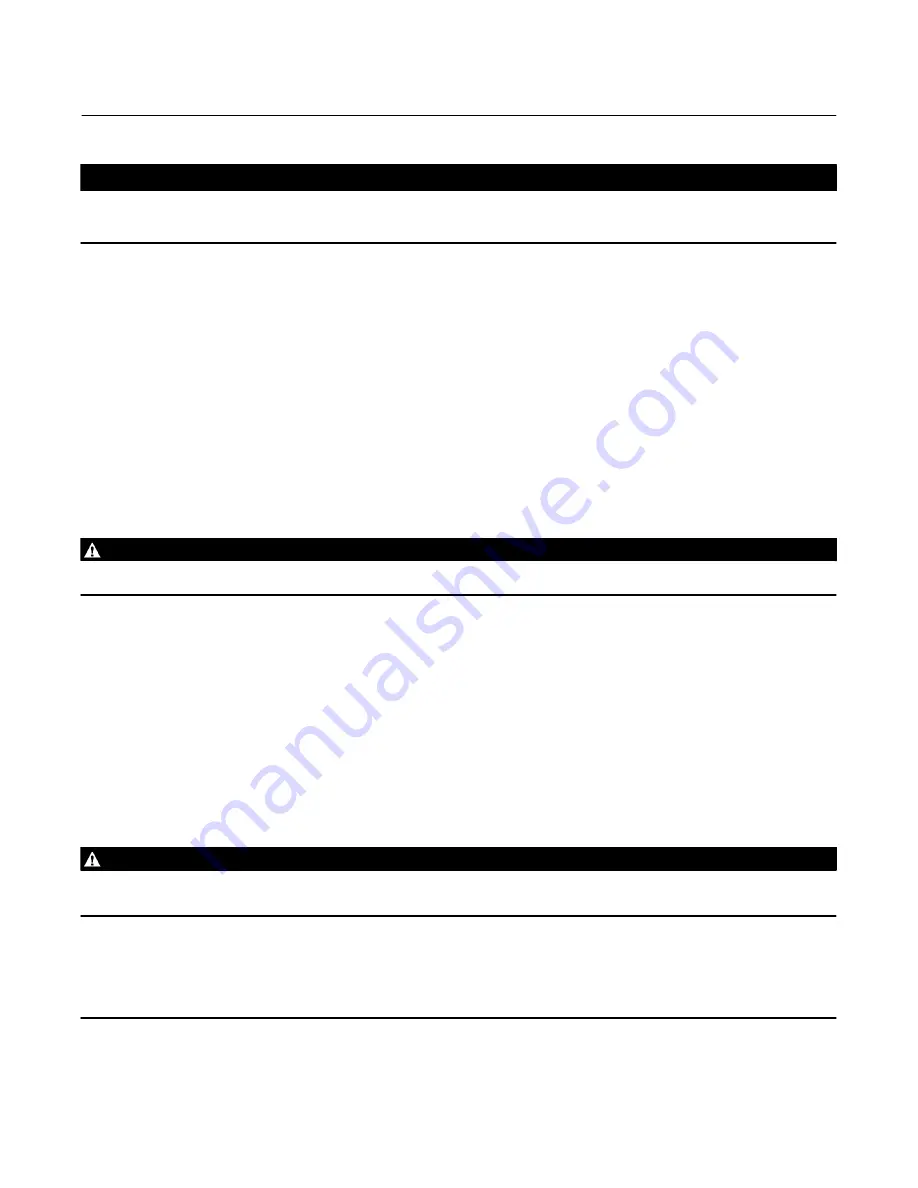
Instruction Manual
D200160X012
4195K Controllers
July 2018
98
CAUTION
Make sure the loose travel stop nut does not bind on the diaphragm capsule extension (key 134) when pressurizing the
capsules (key 80). Damage to the capsules may result.
2.
Full span stop
—Adjust the remote set point pressure to 2‐1/2 percent of span greater than the remote set point
input range upper limit.
Loosen the two screws (keys 139 and 140) that secure the travel stop (key 83) to the mounting plate (key 111). Slide
the travel stop until it is just touching the end of the capsule stack. Tighten the travel stop mounting screws to lock it
into position.
3.
Zero Stop
—Adjust the remote set point pressure to 2‐1/2 percent of span less than the remote set point input range
lower limit.
Slide the travel stop nut (key 86), along the diaphragm capsule extension (key 134) until it is just touching the travel
stop (key 83). Tighten the set screw (key 87) to lock the travel stop nut in position.
Aligning the Linkage
WARNING
Refer to the Maintenance WARNING on page 51.
1. Adjust the remote set point pressure to 50 percent of the remote set point input range.
2. Set the linearity adjustment screw in the center of the slot on the lever arm of pivot clevis assembly B (key 115). See
figure 6‐23 for the linearity adjustment location.
3. Set the length of link A (key 116) so the lever arms of pivot assembly A and pivot assembly B are parallel and link A is
perpendicular to them.
4. Set the length of link B (key 126) so the set point indicator indicates mid‐scale on the process scale span.
5. Replace the tie bar (key 106) and install the two screws (key 103).
Remote Set Point Zero and Span Adjustment
WARNING
Refer to the Maintenance WARNING on page 51.
Note
For routine remote set point zero and span calibration, refer to the appropriate procedures in Section 3, 4, or 5. Use the following
maintenance remote set point zero and span adjustment procedures only if difficulty is encountered with the routine procedure or
nonlinearity occurs.
Refer to figures 6‐19 and 6‐23 for adjustment locations.