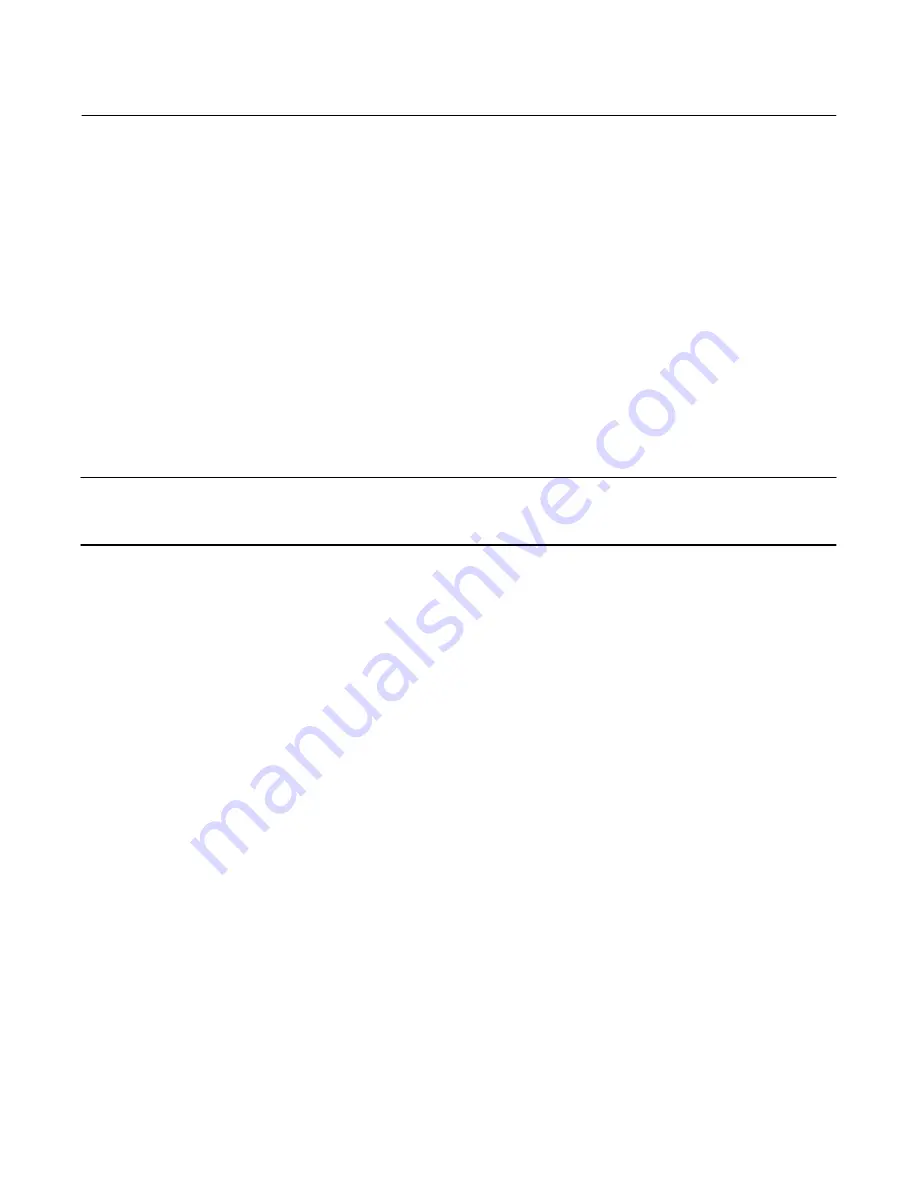
Instruction Manual
D200160X012
4195K Controllers
July 2018
62
16. At the frame manifold (key 135), tighten the nut that secures the tubing from the relay nozzle tubing assembly
(key 18). Apply full supply pressure with the nozzle capped and check for leaks. Remove supply pressure.
17. Install the set point beam bias spring (key 28) into the frame bore and onto the spring seat on the set point beam
assembly.
18. Attach link 3 to the set point beam shoe as shown in figure 6‐3.
19. For controllers with reset or rate adjustment (4195KB or 4195KC controllers), turn the reset adjustment to the
CLOSED (4195KB) or OFF (4195KC) position. Set the rate adjustment to the OFF position.
The controller output must be 0 bar (0 psig). To be sure the controller output is 0 bar (0 psig ), remove supply
pressure, set the reset adjustment to 0.01 minutes per repeat and wait 30 seconds; then, turn the reset adjustment
to the CLOSED position (4195KB) or to the OFF position (4195KC).
the controller output pressure.
21. Perform the appropriate process indicator zero and span calibration procedure and, if necessary, the remote set
Note
The following procedure (steps 22 through 28) matches the process pointer motion to the set point indicator motion so the
controller will control at set point at all positions on the process scale.
22. Set the proportional band to 40 percent in REVERSE or DIRECT depending on the desired controller action.
23. Adjust the set point to the lower limit on the process scale.
24. Disconnect link 1 from the input element, noting the hole from which it is removed, for capsular input elements,
and tape the process pointer to the lower limit on the process scale. The output pressure may be anywhere
between 0.2 to 1.0 bar (3 to 15 psig) for a 0.2 to 1.0 bar (3 to 15 psig) output signal range or between 0.4 to 2.0 bar
(6 to 30 psig) for a 0.4 to 2.0 bar (6 to 30 psig) output signal range. If the output is not within the specified range,
adjust the flapper leveling screw nearest the nozzle until the output is within the range specified. Record the
controller output pressure.
25. Adjust the set point to the upper limit on the process scale.
Note the process pressure indication.
27. The process pressure indication should be within
±
2 percent of the upper limit on the process scale.
If the process pressure indication in step 26 is greater than the upper limit of the process scale by 2 percent, loosen
the shoe adjustment screws (key 30), shown in figure 6‐3, and move the set point beam shoe (key 29) slightly away
from the center of the flapper assembly.
If the process pressure indication in step 26 is less than the upper limit of the process scale by 2 percent, loosen the
shoe adjustment screws (key 30), shown in figure 6‐3, and move the set point beam shoe (key 29) slightly toward
the center of the flapper assembly.
process scale.
29. Remove the tape from the process pointer and reconnect link 1 to the input element. If the controller has a capsular
input element, be sure to reconnect link 1 in the same hole noted in step 24.
30. Position the controller assembly in the case and start, but do not tighten the nine mounting screws. Slide the
controller assembly down to assure an O‐ring seal at the pressure connections along the bottom of the case. Hold
the controller assembly in place while tightening the nine mounting screws.