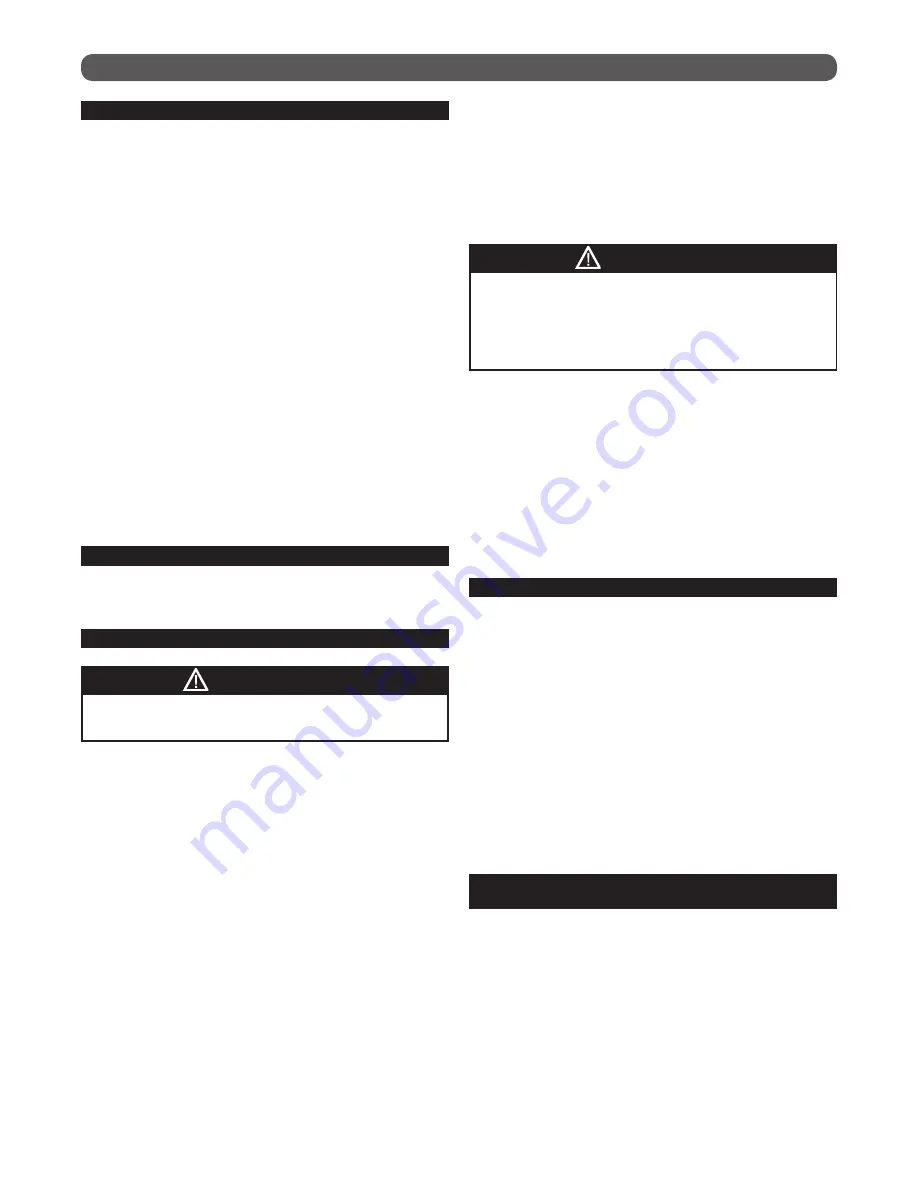
54
MAINTENANCE
A. GENERAL (WITH BOILER IN USE)
General boiler observation can be performed by the owner.
If any potential problems are found, a qualified installer or
service technician/agency must be notified.
1. Remove any combustible materials, gasoline and other
flammable liquids and substances that generate flammable
vapors from the area where the boiler is contained.
2. Observe general boiler conditions (unusual noises,
vibrations, etc.)
3. Observe operating temperature and pressure on the
combination gauge located in the supply piping on the left
side of the boiler. Boiler pressure should never be higher
than 5 psi below the rating shown on the safety relief valve
(25 psig maximum for a 30 psig rating). Boiler temperature
should never be higher than 240° F.
4. Check for water leaks in boiler and system piping.
5. Smell around the appliance area for gas. If you smell
gas, follow the procedure listed in the Lighting Operating
Instructions to shut down appliance in Section 9, Start-Up
Procedure Part B.
B. WEEKLY (WITH BOILER IN USE)
Flush float-type low-water cut-off (if used) to remove sediment
from the float bowl as stated in the manufacturer’s instructions.
C. ANNUALLY (BEFORE START OF HEATING SEASON)
1. Check boiler room floor drains for proper functioning.
2. Check function of the safety relief valve by performing the
following test:
a. Check valve piping to determine that it is properly
installed and supported.
b. Check boiler operating temperature and pressure.
c. Lift the try lever on the safety relief valve to the full
open position and hold it for at least five seconds or
until clean water is discharged.
d. Release the try lever and allow the valve to close. If the
valve leaks, operate the lever two or three times to clear
the valve seat of foreign matter. It may take some time
to determine if the valve has shut completely.
e. If the valve continues to leak, it must be replaced before
the boiler is returned to operation.
f. Check that operating pressure and temperature have
returned to normal.
g. Check again to confirm that valve has closed completely
and is not leaking.
3. Test low-water cut-off (if used) as described by the
manufacturer.
4. Test limit as described in Section 9, Part D,
“Check Operation”.
5. Test function of ignition system safety shut-off features as
described in Section 9, Part D, “Check Operation”.
6. Remove the top/front jacket panel and inspect for any foreign
debris that may have entered through air intake vent.
7. Inspect burner for deterioration. Replace if necessary.
8. With boiler in operation check that condensate is dripping
from condensate tubing. Check for any restriction in
condensate drain line.
D. CONDENSATE CLEANING INSTRUCTIONS
1. Check trap for blockages and that the check ball is free
floating. Remove the screw bottom of the condensate trap
to allow any sediment to clear the trap. The check ball can
be removed and cleaned with a small brush. Replace ball
and secure bottom cap once done.
2. Check the condition of any condensate pumps that are
installed. Impellers can deteriorate over time do to exposure
to the acidic condensate.
3. Check the condition of any neutralization systems installed.
Replace neutralizing agent if needed.
4. Check that the pressure switch tap has not been blocked or
clogged with debris.
E. INSPECTION AND CLEANING OF
COMBUSTION CHAMBER COILS
Before beginning this procedure, you must have on hand the
following items:
– a nylon or brass brush (not steel)
– “Rydlyme” (recommended for best results) (available
online www.rydlyme.com) or “CLR” (available at most
hardware stores)
1. Shut the boiler down and access the heat exchanger using
the following steps:
a. Close the manual gas shutoff valve and wait for the unit
to be cool to the touch.
CAUTION
The following annual inspection must be performed
by a qualified service technician.
DANGER
When servicing or replacing components, be absolutely
certain that the following conditions are met:
• Water, gas and electricity are off.
• The boiler is at room temperature.
• There is no pressure in the boiler.
Summary of Contents for Peak-40
Page 22: ...22 WATER PIPING AND CONTROLS Figure 4 6 Recommended Central Heat Piping ...
Page 24: ...24 WATER PIPING AND CONTROLS Figure 4 8 Recommended Domestic Hot Water Piping ...
Page 33: ...33 ELECTRICAL CONNECTIONS Figure 7 4 Wiring Schematic and Connection ...
Page 47: ...47 START UP PROCEDURE E LIGHTING OPERATING PROCEDURES ...
Page 59: ...59 THIS PAGE INTENTIONALLY LEFT BLANK ...
Page 62: ...62 REPAIR PARTS Figure 13 2 Peak 40 LP Combustion Components ...
Page 64: ...64 REPAIR PARTS Figure 13 3 Peak 40 NG Combustion Components ...
Page 66: ...66 REPAIR PARTS Figure 13 4 CHB Parts Detail ...
Page 68: ...315 Oser Avenue Hauppauge NY 11788 Tel 631 694 1800 Fax 631 694 1832 www embassyind com ...