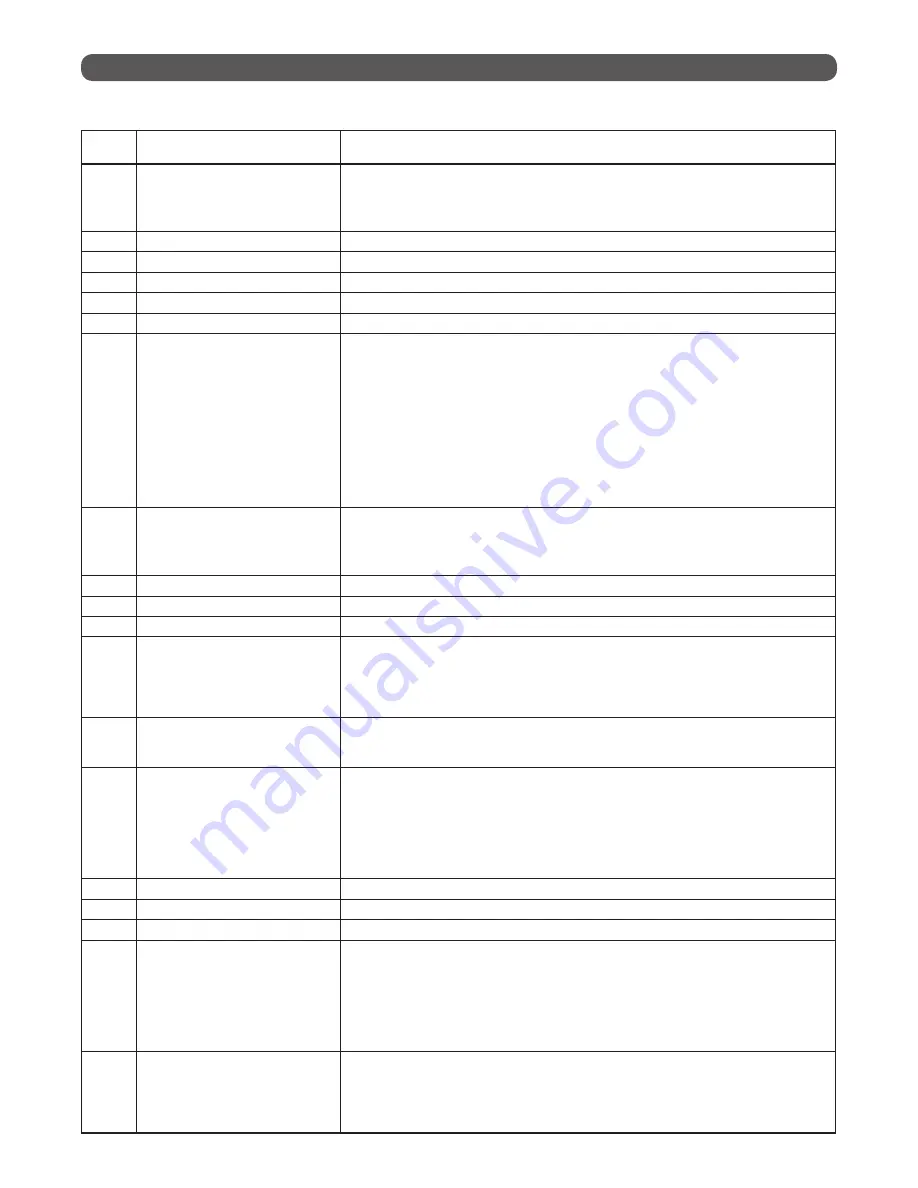
50
TROUBLESHOOTING
Table 10.1 (cont.): Lockout Codes
Error
Number
Error Display
Corrective Action
7
FAN_ERROR_TOO_FAST
Fan runs to fast for more than 60 seconds
– Check for continuity through blower control harness, 5 pin connector to J4
connector on control board. If continuity is not found, replace harness.
– Replace control if other actions do not correct issue.
8
RAM_ERROR
Internal software error. Replace Control.
9
WRONG_EEPROM_SIGNATURE
Contents of E2prom is not up to date. Replace Control.
10
E2PROM_ERROR
Wrong safety parameters in E2prom. Replace Control.
11
STATE_ERROR
Internal software error. Replace Control.
12
ROM_ERROR
Internal software error. Replace Control.
15
MAX_TEMP_ERROR
Thermal Fuse in the main heat exchanger body has tripped. This fuse should only
open if extreme conditions have occurred within the unit.
– Replace Heat exchanger or entire boiler.
– Check all safety limits and sensors before resuming operation of the unit.
– Check target wall and burner door insulation for degradation on old heat
exchanger. Evidence of heavy recirculation.
– Check internal pump operation.
– The thermal fuse is located on the top right of the heat exchanger and is
connected to a set of pink/black wires. Ensure connection is secure.
– If error occurred during installation start-up, reset the control to clear error. If
error reoccurs, contact your Factory Representative.
16
FLUE_GAS_ERROR
Flue Temperature exceeded the maximum flue temperature limit (192.2°F (89°C)).
– Lower system setpoint to decrease flue temperature.
– Check temperature delta across the boiler supply and return. A low delta will
cause increased flue temperatures due to poor energy transfer.
17
STACK_ERROR
Internal software error. Replace Control.
18
INSTRUCTION_ERROR
Internal software error. Replace Control.
19
ION_CHECK_FAILED
Internal software error. Replace Control.
20
FLAME_OUT_TOO_LATE
Flame still present 10 seconds after closing the gas valve.
– Check flame sensor for a short to ground. Replace sensor, sensor gasket or
harness if short is found.
– Check solenoid on gas valve for operation. Gas valve might not be closing
properly. Replace gas valve.
21
FLAME_BEFORE_IGNIT
Flame is detected before ignition.
– Check flame sensor for a short to ground. Replace sensor, sensor gasket or
harness if short is found.
22
TOO_MANY_FLAME_LOSS
Flame signal was lost 3 times during a single demand cycle.
– Remove flame sensor and check for white build-up. Clean sensor, re-install and
attempt ignition. If ignition still fails perform other actions listed here. Replace
sensor. If sensor appears cracked or bent, replace sensor.
– Confirm fuel pressure at the valve inlet when the valve is open. Low gas pressure
can cause flame failures. If another appliance is connected to the gas line,
confirm gas pressure at the gas valve when both appliances are in operation.
23
CORRUPTED_ERROR_NR
Error code RAM byte was corrupted to an unknown error codes. Replace control
29
PSM_ERROR
Internal software error. Replace control.
30
REGISTER_ERROR
Internal software error. Repl;ace control.
33
LWCO_1_ERROR
Low water cut off error.
– If using LWCO probe kit, check system for leaks and filling valve for operation.
Check wiring to LWCO probe and that the connector to the probe is securely
attached. Check grounding to piping where the LWCO probe is installed. Ensure
that the probe is installed in a location that is not collecting air.
– If not using the LWCO probe kit, check the jumper across terminal 5 and 6 on
the low voltage terminal block. If broken replace with a 15 k
Ω
or similar resistor.
38
FLUE_PRESSURE_LOCKING
More than 3 Blocked Flue/ Condensate Switch in 24 hours.
– Check for blockages in the vent pipe or heat exchanger.
– Check for blockages in the condensate system inside or after the condensate
trap. A slow drainage of condensate could cause condensate back up that will trip
this switch under certain conditions.
Summary of Contents for Peak-40
Page 22: ...22 WATER PIPING AND CONTROLS Figure 4 6 Recommended Central Heat Piping ...
Page 24: ...24 WATER PIPING AND CONTROLS Figure 4 8 Recommended Domestic Hot Water Piping ...
Page 33: ...33 ELECTRICAL CONNECTIONS Figure 7 4 Wiring Schematic and Connection ...
Page 47: ...47 START UP PROCEDURE E LIGHTING OPERATING PROCEDURES ...
Page 59: ...59 THIS PAGE INTENTIONALLY LEFT BLANK ...
Page 62: ...62 REPAIR PARTS Figure 13 2 Peak 40 LP Combustion Components ...
Page 64: ...64 REPAIR PARTS Figure 13 3 Peak 40 NG Combustion Components ...
Page 66: ...66 REPAIR PARTS Figure 13 4 CHB Parts Detail ...
Page 68: ...315 Oser Avenue Hauppauge NY 11788 Tel 631 694 1800 Fax 631 694 1832 www embassyind com ...