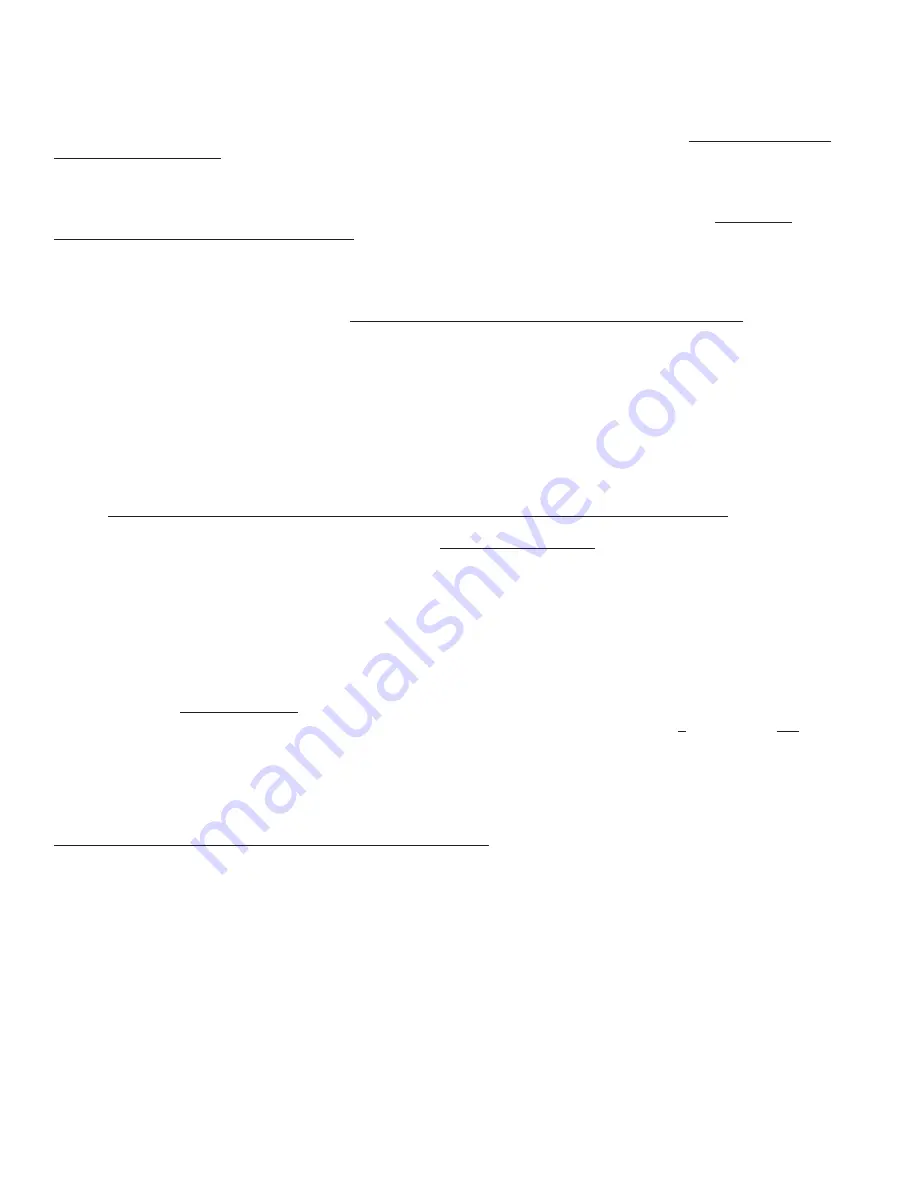
M1XSP Installation Manual
Page 14
UPB
is a PLC or Powerline Communications lighting technology. There are 2 methods for interfacing UPB to M1. First is an
ELK-M1XSP connected to a UPB PIM 'S" (RS232 Serial Program Interface Module). Second is a new product called the
ELKM1PCSPIM (or PCSPIM 'E'). This product looks like an ordinary PIM but actually contains both a PIM and M1XSP processor
module. It connects directly to the M1 Data Bus and eliminates the RS232 cord/connection. NOTE: The M1PCSPIM is internally
fixed to M1 Bus Address #7, meaning that no other M1XSP's on the bus may be set to that address. Regardless of the type of
connection, M1 supports up to 192 UPB individual addresses (dimmers, switches) and 64 UPB Links (scenes).
Integration is accomplished by "mapping" the UPB addresses and operation to M1 Lighting device entities. UPB device
addresses 1-192 map to M1 Lighting devices 1-192. UPB Links 1-64 map to M1 Lighting devices 193-256. NOTE: Links
require M1XSP firmware version 1.0.14 or higher. The chart on the next page shows the M1 Light devices and UPB mappinig.
Components required for UPB integration:
-
ELK-M1 or ELK-M1EZ8 Controller and the ElkRP Programming Software.
-
ELK-M1XSP Serial Port Expander. Firmware updating may be required and may be downloaded from the ELK Web site.
-
UPB PIM (Programming Interface Module) { or ELKM1PCSPIM which is internally fixed to M1 Bus Address #7}
-
One or more UPB Lighting devices plus the UPB PC Programming Software called "UPStart."
Setting up to communicate with UPB { Skip steps 1 - 4 if you are using the new ELKM1PCSPIM }
1.
Install the ELK-M1XSP per the instructions on page 3. Be sure to enroll the device into the M1.
2.
Connect the female end of the supplied 9-pin serial cable to the M1XSP and the male end to the UPB PIM Module.
3.
Set the
MODE
Jumpers on the M1XSP as follows:
S4*="1" (UP), S5="1" (UP), S6="1" (UP), S7="0" (DN), S8="1" (UP).
NOTE: Some units do not have jumper S4.
4.
Set the M1XSP Jumper
JP3="232"
. Set
JP5
to
ON
. The position of BAUD jumpers S1,S2,S3 does not matter.
5.
Power up all the devices.
6.
Using the ElkRP software, open the "Globals" folder. Then go to the "G29-G42 Special" tab and program the same unique
UPB NETWORK ID into the M1 that is stored in the UPB switches.
DO NOT USE NETWORK ID 0 OR 255 AS THESE ID HAVE SPECIAL PURPOSE RESERVED BY UPB.
7.
In the ElkRP software open the Automation > Lighting folder and program the M1 Lighting devices. Only the devices
specifically for UPB use will need to be programmed. For UPB individual addresses program M1 Lighting devices:
1-192
as: Format=Serial Expander, Type= Dimmer (or "On/Off Switch" if the device isn't dimmable)
. For UPB link addresses
program M1 Lighting devices:
193-256 as: Format= Serial Expander, Type=On/Off Switch.
When an M1 Light device is activated from a rule or from the M1 Keypad "Automation" menu, the corresponding device com-
mand will be sent onto the powerline network to the UPB Devices.
Programming the UPB devices:
The UPB UPStart Software must be used to program each UPB module with an address, a network ID, and any other options.
IMPORTANT:
The UPB NETWORK ID programmed into the UPB switches MUST MATCH the UPB NETWORK ID programming
into the ElkRP software. [ElkRP Globals folder > G29-G42 Special tab. DO NOT USE NETWORK ID 0 or Network ID 255.
UPB Device Status:
In order to receive "Load Status" changes from the UPB devices, make sure to program their option bit "Transmit Changes".
LIMITATIONS - CURRENT STATUS FROM UPB MODULES
Status reports resulting from manual rocker (pushbutton) changes. - UPB devices may be optionally programmed to
broadcast (report) their individual status whenever a manual change occurs via the rocker (pushbutton) switch. This
option requires UPStart PC Software and each device must be individually programmed. Go to tab labeled "Rocker
Switch". On this tab place a checkmark in the box option labeled "Report light level after rocker switch is pressed."
Status reports resulting from UPB LINK commands. - UPB devices DO NOT and CANNOT be programmed to broad-
cast (report) their status when changed by a LINK command. Because a LINK can affect anywhere from 1 to 255
devices simultaneously, the communications protocol does not permit status reports because the entire performance of
the UPB network could be adversly affected. For this reason, the status displayed by M1 Controller may not always
match the true status of UPB devices when devices are controlled by a Link command. This is a UPB protocol issue
and there is nothing (NO WORKAROUND) that Elk can do to resolve this issue.
PC based software packages with access to lots of memory are able to memorize which UPB switches belong to each
LINK along with their programmed (expected) response to each LINK. From this they are able to either anticipate the
expected status OR poll only each affected device in order to obtain their status report. But even this is not practical
when large numbers of devices are involved in a LINK. Simply put, it can take up to 5 minutes to poll all 255 potential
UPB devices, during which network traffic and device communications would be totally swamped and messages lost.
UPB - (Individual Lighting Loads and Links)