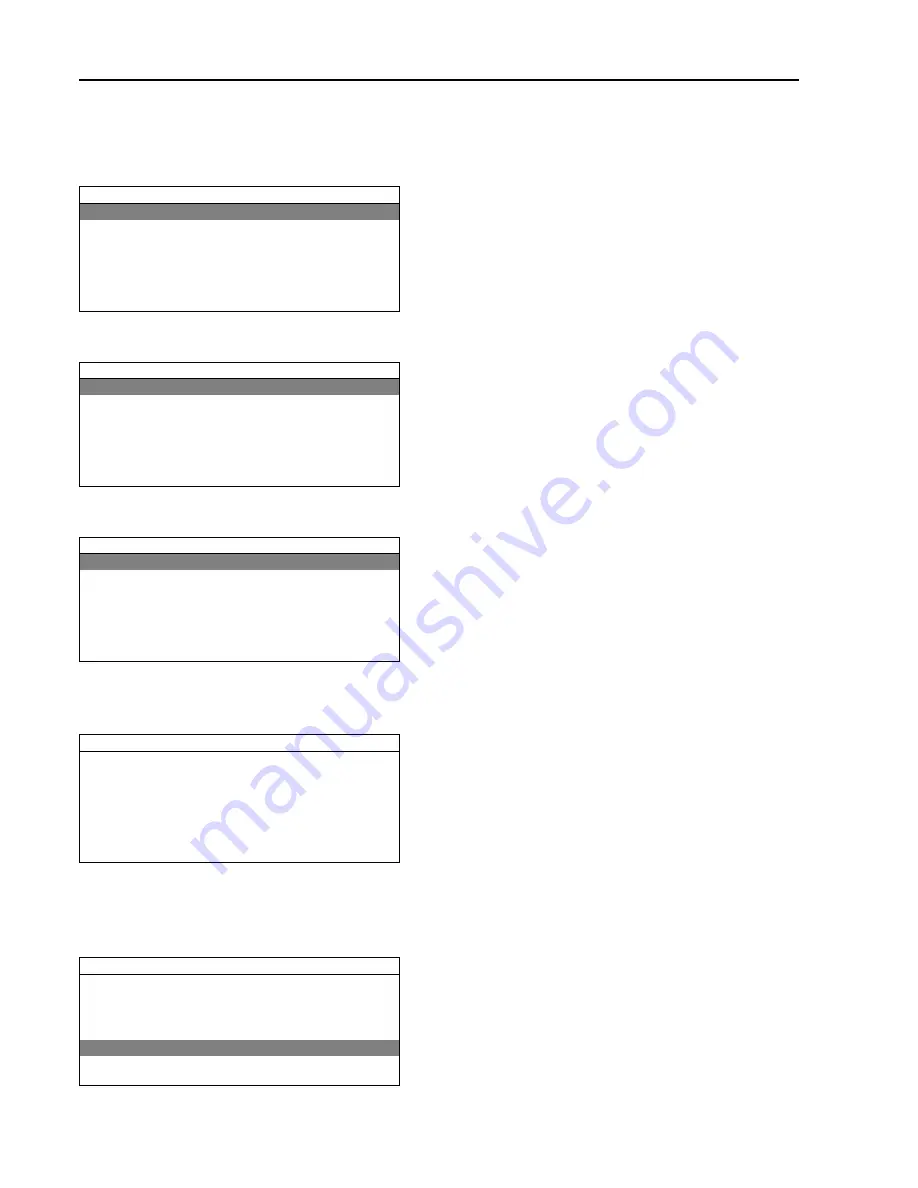
20
Installation manual
A password is needed to continue.
The default password is set to 01234.
When the password is set you will enter the
INSTALLER MENU
.
Activate the
INSTALLER SERVICE
menu.
INSTALLER MENU
INSTALLER SERVICE
INITIAL SYSTEM SETUP
PROGRAM FORMULAS
DATA TRANSFER
SET UNITS OF MEASURE
Activate the
SERVICE PUMPS
menu.
INSTALLER SERVICE
SERVICE PUMPS
VIEW LOAD COUNT
VIEW LOAD WEIGHT
VIEW AMOUNT PUMPED
CLEAR DATA LOG
Activate the
PRIME PUMP
menu.
SERVICE PUMPS
PRIME PUMP
PUMP CALIBRATION
NAME PUMPS
ENTER PRODUCT COSTS
DATE TUBE CHANGED
Select pump from the list to and press Enter to start and stop the pump.
The hose shall be filled all the way to the outlet of the hose.
SET PRIME PUMP
P1
P2
P3
P4
P5
P6
3.5 Calibrating the pumps
Make sure the pumps has been primed before calibrating.
Enter the
MAIN MENU
and activate the
INSTALLER MENU
.
MAIN MENU
EMERGENCY PUMP STOP
USER PRIME PUMPS
USER MANUAL FLUSH
MANAGER REPORTS
INSTALLER MENU
VIEW EFFICIENCY