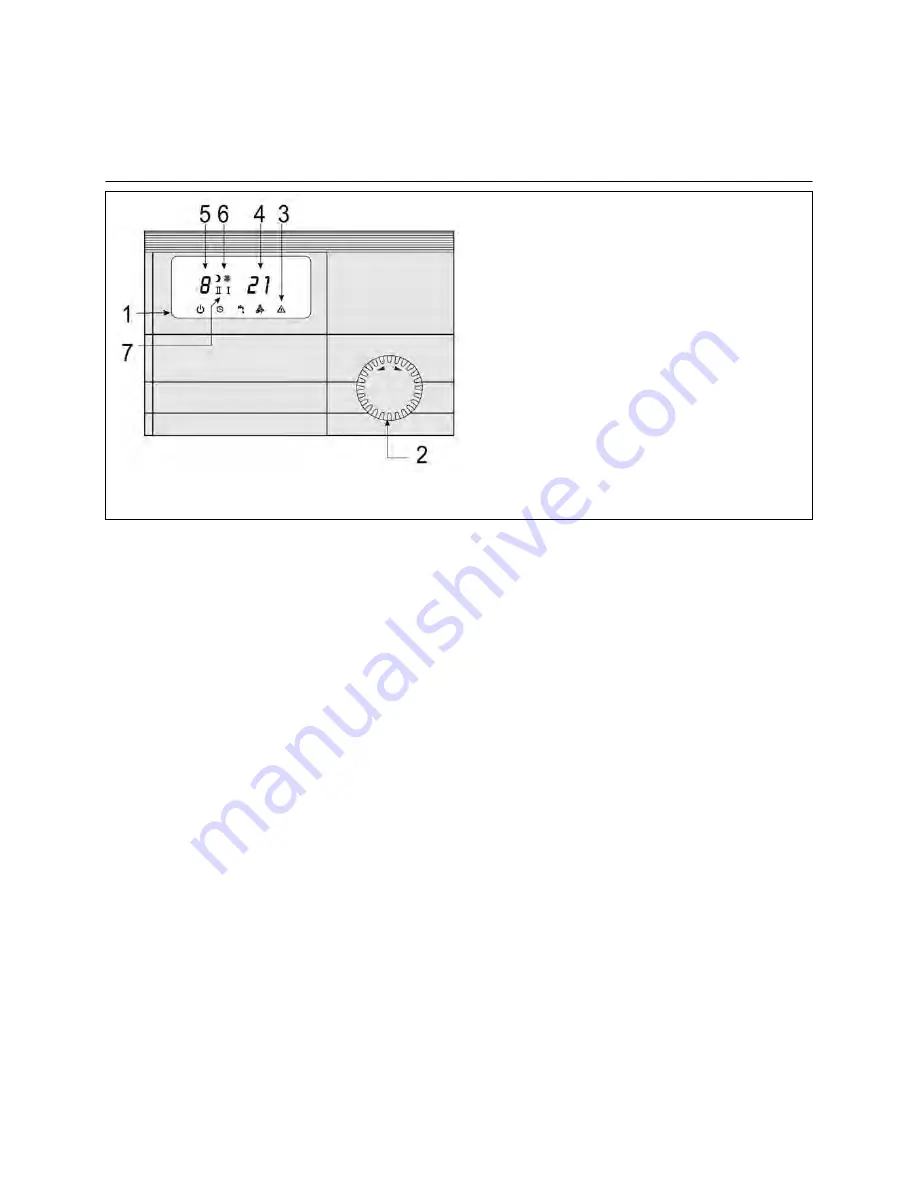
Set up
Switch field with operating field KM628
Operating functions (flap closed)
When the flap is closed, the desired
operating status can be selected by
turning the knob (2) left or right.
i
Standby
Boiler
not
in
use,
frost
protection
active
q
Automatic operation
Boiler in use for heating and hot water user
F
Summer operation
Boiler in summer operation (only hot water use)
j
I Chimney sweep operation, minimum load
Boiler in use, minimum load
j
II Chimney sweep operation, maximum load
Boiler in use, maximum load
20
1 Operating
type
i
Standby
q
Automatic
operation
F
Summer
operation
j
Chimney sweep operation
2
Operating type selector
3 Fault
display
E
4 Lead
temperature
5 Fault
code
(blinking)
6 Heating
circuit
status
C
Night
operation
B
Day
operation
(Blinking) Burner on
7 Service
status
j
I Service status minimum burner
output
j
II Service status maximum burner
output
Summary of Contents for RENDAMAX 30
Page 26: ...26 Notes ...
Page 27: ...Notes 27 ...