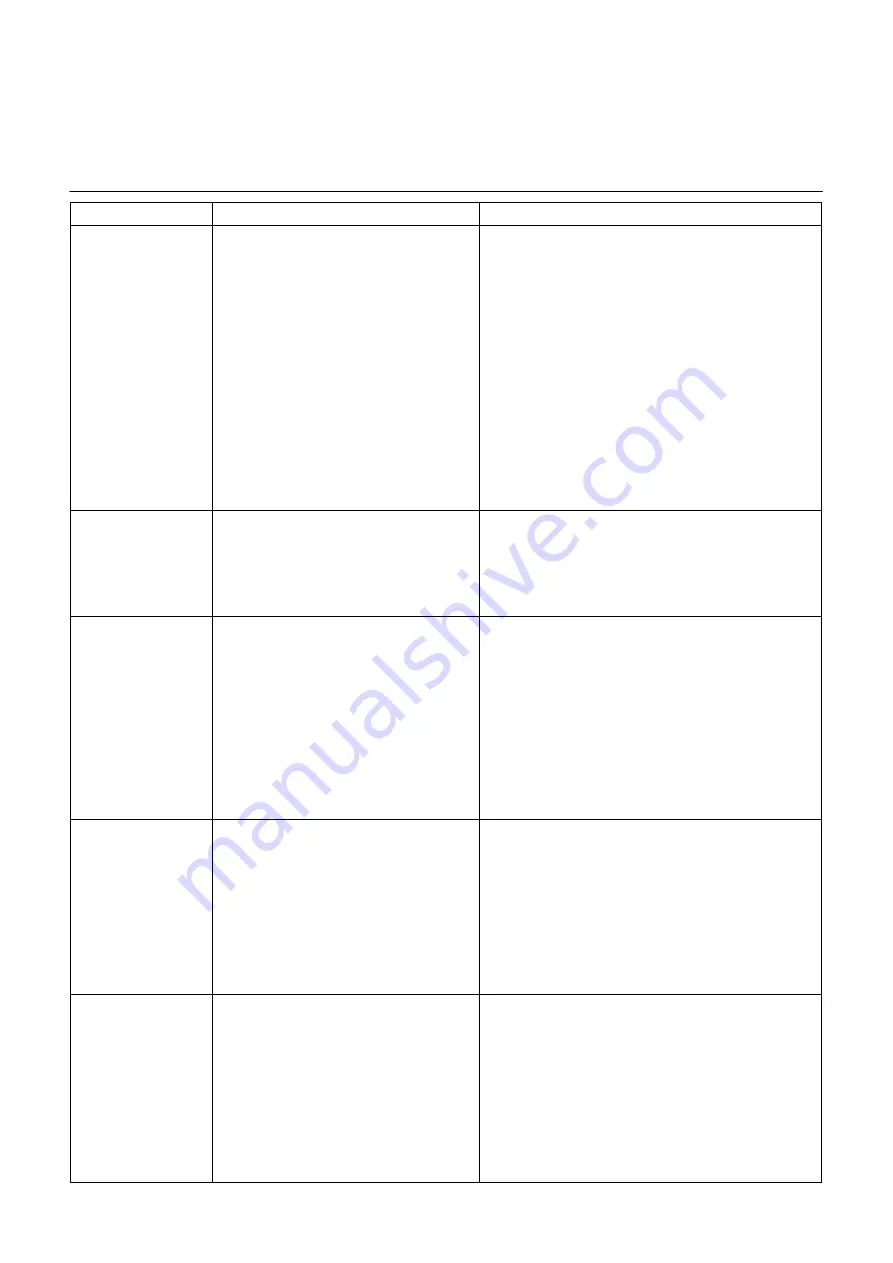
Problem
Cause
Remedy, Action
225: Low pressure
problem
Low pressure problem
Affects contact E9 at the LOGON B WP61.
Low pressure switch in the cooling circuit
triggered.
A
Insufficient flow of air through evaporator
A1 Ice formation
A2 Evaporator dirty
A3 Grating dirty
A4 Fan not running or not running enough
B
Leak in cooling circuit
C
Injection valve defective, frozen or clogged
D
Incorrect amount of coolant
E
Leak in cooling circuit
A1 Check thawing function (check sensor)
A2 Clean evaporator
A3 Clean grating
A4 Check speed, adjust, check voltage
If everything in A can be excluded:
B
Measure temperature difference between filter dryer input
and output (
∆
T max 3 K)
C
Check, set or replace injection valve
D
Empty and refill in accordance with type plate
E
Oil residue in the unit is another indication of a leak in
the cooling circuit.
The refrigerant technician must be called in such cases.
226: Winding protection
compressor
Affects contact E11 at the LOGON B WP61.
A
Phase interruption (compressor gets hot)
B
Phase reverse (incorrect rotary field)
C
Phase loss
D
Phase asymmetry
E
Short circuit
A
Check all three phases (wait until the winding protection
has cooled, can take several hours).
B
Check electrical connection.
C
Check whether oil sump heater is working.
D
Make sure the rotation is right.
E
Eliminate short circuit
247: Thawing problem
After the fourth thawing attempt, the evaporator
sensor on the cooling circuit (B84) still has not
reached the evaporator temperature
(Para. 2954) set at the LOGON B WP61.
A
Sensor B91 positioned incorrectly
B
Sensor B84 defective/no longer in the
required position
C
Not enough energy for thawing
(water temperature in heating circuit too
low)
D
Flow rate to the condenser too low
A
Position sensor properly, replace sensor if defective
B
Check sensor position. Check function (measure actual
temperature in all injection pipes and compare with
B84 value)
C
Switch on electric heating element until the minimum
water temperature is reached. Close part of heating circuit.
D
Check pumps for functions, check return and switch valves
358: Soft starter
Actions in relation to the LOGON B WP61’s E25
(EX5) contact.
The soft starter signals an alarm via the auxiliary
relay. The alarms envisaged may be:
- Incorrect phases sequence
- Line voltage off the scale
- Frequency outside the range
- Jammed rotor
- Start-up ramp > 1 s
- Over-temperature
- Excess current (during the bypass)
- Supply voltage imbalance
Carry out the failure reset (HMI) and check the following:
A Check the sequence of the 3 input phases on the soft starter
B Measure the voltage of the 3 phases
C Check the electrical connections
D Check that the magnetic field is rotating clockwise
(check the sequence of the 3 phases in the compressor ter
minal block)
E Measure the current absorption
F In the event of the load being lightened, integrate an addi-
tional relay;
see the discharger info.
12: PWW charge temp.
HP too low
The controller stores the potable water tempera-
ture at which the charging with the heat pump
was last interrupted when the heat pump
reached the high pressure, hot gas or maximum
switch-off temperature limit.
If the value is lower than the setting “PWH
charge temp HP minimum" (control line 7092),
the service symbol will appear in the display
and details of the service in the info line.
This parameter cannot be reset. If the minimum PWW charging
temperature is exceeded again the next time potable water is
charged, the service function will also be reversed. If it is still
not reached, the service message will remain.
1.
Check placement of the of the B3 sensor
2.
Setpoint too high for PWW temp.
3.
Charging type activated with B3 and B31, switch to B3
only
4.
Temperature transmission to PWW sensor
poor, improve with spring clamp
5.
In the mother/child storage the PWW charge should
occur at different levels via a three-way valve.
6.
Heat exchange area of the storage is too small
Maintenance
Troubleshooting
51
Summary of Contents for AEROTOP G
Page 28: ...Installation Delivery to installation site 2 3 1 n 17 4x 8x M10 4x 4x 28...
Page 29: ...Installation Delivery to installation site 29...
Page 31: ...Installation Hydraulic connections assembly instructions 3 1 n 3 1 4 2x n 46 1 x 2 1 4 10 x 31...
Page 32: ...Installation Hydraulic connections assembly instructions 4 7 5 8 4x 1 4 6 2 x 32...
Page 36: ...Installation Instruction for the installation of control unit black wire CL 5 4 36...
Page 57: ...Notes 57...
Page 58: ...Service www elco net...