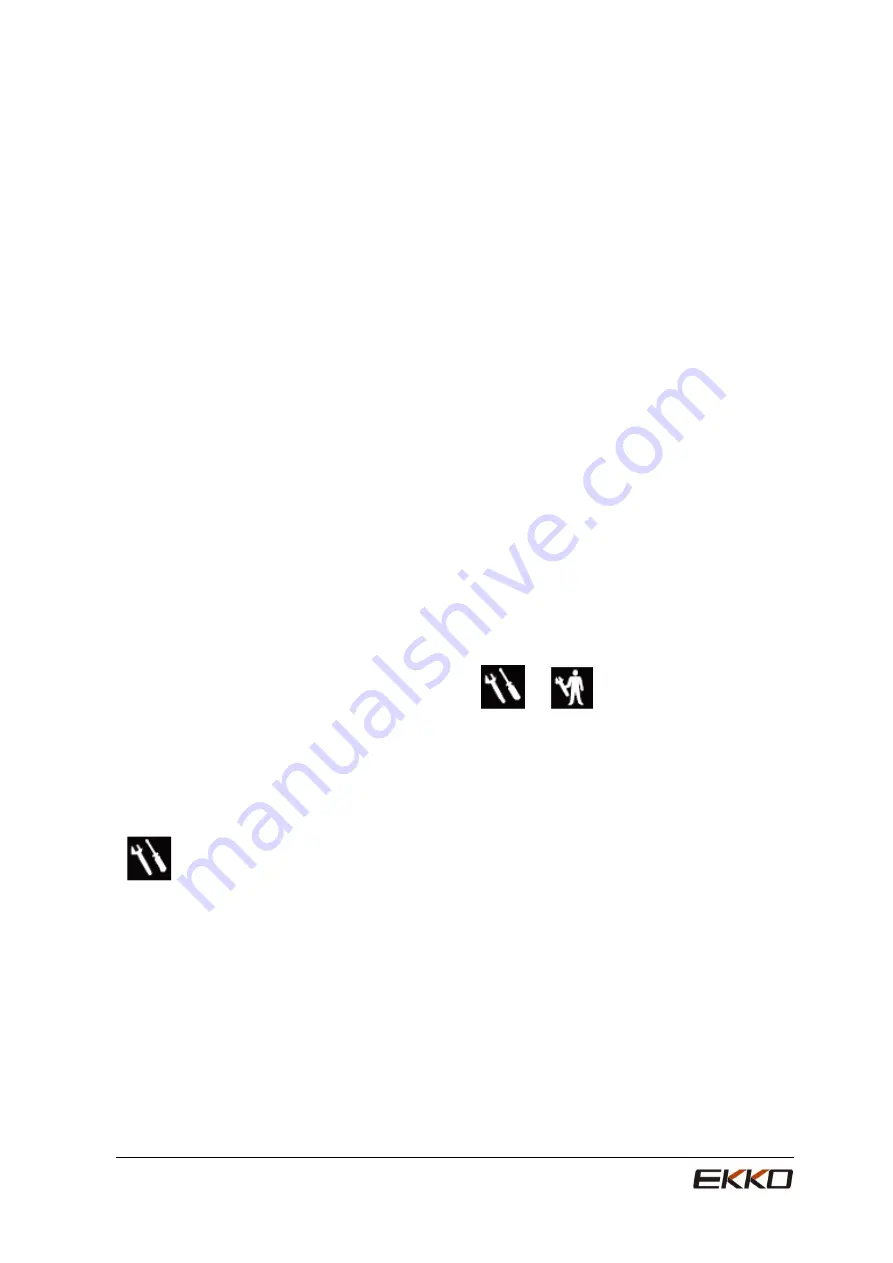
Maintenance
52
sounds and the platform will lift to 2m or
beyond. The machine is function properly.
¤
Result: The pothole guard contacts the
block and does not fully deploy. The
diagnostic LCD does not display "18". The
alarm does not sound and the machine will
continue to lift the platform. Adjust or replace
the pothole limit switch.
34. Press and hold the drive/steer function
enable switch on the control handle.
Attempt to drive and steer the machine.
⊙
Result: The diagnostic LCD displays "18".
The alarm sounds, and the machine will not
steer or drive. The machine is functioning
properly.
¤
Result: The diagnostic LCD does not
display "18". The alarm does not sound and
the steer and drive functions operate. Adjust
or replace the pothole limit switch.
35. Lower the platform to the stowed position
and remove the block under the right
pothole guard.
36. Repeat this procedure beginning with
step 31~34 for the left pothole guard.
37. Lower the platform to the stowed position,
remove the block under the left pothole
guard.
38. Turn off the machine.
B-15
Test the Up Limit Switch (if equipped)
This procedure should be performed every
250 hours or quarterly, whichever comes first.
Maintaining the limit switches is essential to
safe
operation
and
good
machine
performance. Operating the machine with a
faulty limit switch could result in reduced
machine performance and a potentially unsafe
operating condition.
Perform this procedure with the machine on a
firm, level surface that is free of obstructions.
1. Turn the key switch to ground control and
raise the platform approximately 2.5 m
from the ground.
2. While raising the platform from the ground
controls, push the arm of the up-limit
switch.
⊙
Result: The platform stop raising, and the
machine is functioning properly.
¤
Result: The platform continues to rise.
Adjust or replace the maximum drive height
limit switch.
Checklist C
C-1
Calibrate the Platform Overload
System
(
if equipped)
This procedure should be performed every
500 hours or six months, whichever comes
first OR when the machine fails to lift the
maximum rated load.
Testing the platform overload system regularly
is essential to safe machine operation.
Continued use of an improperly operating
could result in the system not sensing an
overloaded platform condition. Machine
stability could be compromised resulting in the
machine tipping over.
The platform overload system is designed to
prevent machine operation in the event the
platform is overloaded. It provided with two
control components: the overload pressure
transducer and the scissors angle sensor.
The overload pressure transducer is used to
determine the pressure of the cylinder and
feedback to the platform overload system with
analog signal. When the pressure is too high,
ECU will compare with the value of Angle
Summary of Contents for ES100E
Page 5: ...Decals 3 ...
Page 7: ...Decals 5 ...
Page 9: ...Decals 7 ...
Page 59: ...Electrical Schematic Diagram 57 ES40E ...
Page 60: ...Electrical Schematic Diagram 58 ES60E ES80E ES100E ES120E ...
Page 62: ...Hydraulic Schematic Diagram 60 ES80E Y7 Y7 G1 4 19 Y1 Y1 Y2 Y2 Y3 Y3 Y4 Y4 Y5 Y5 Y6 Y6 ...
Page 64: ...Hydraulic Schematic Diagram 62 Maintenance Record Date Note ...
Page 65: ......