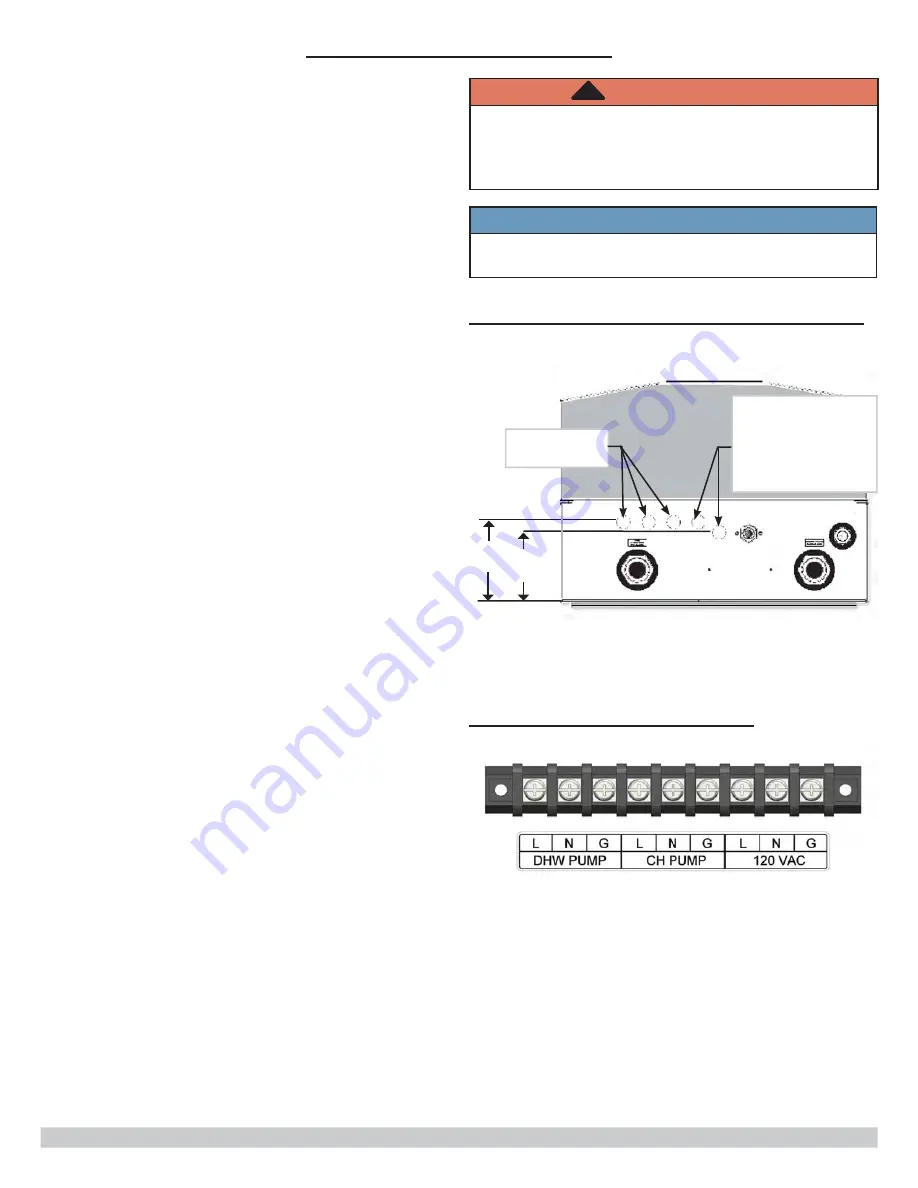
27
8.1 General
Electrically bond boiler to ground in accordance with
requirements of authority having jurisdiction. Refer to:
USA- National Electrical Code, ANSI/NFPA 70.
•
Canada - Canadian Electrical Code, Part I, CSA C22.1:
•
Safety Standard for Electrical Installations.
8.2 Electric Knockouts (Figure 8-1)
Five knockouts located on bottom of chassis.
•
Three knockouts located under junction box are
A.
reserved for high voltage wires. Choose connectors
using total diameter of wire bundles.
Two knockouts located to right of high voltage
B.
knockouts (outside of junction box) are reserved
for low voltage wiring. Use supplied grommets
when using these knockouts.
8.3 Line Voltage Connections (Figure 8-2)
Boiler
•
Provide individual 120V, 15 amp circuit
A.
(recommended) with fused disconnect or service
switch as required by authority having jurisdiction.
Open High Voltage Junction Box (see fi gure 3-4) to
B.
access line voltage terminal strip.
Connect 120 VAC circuit to line voltage terminal
C.
strip 120 VAC L,N,G.
Central Heating Pump, if used.
•
Isolate pump from control module if pump FLA (Full
A.
Load Amps) exceeds 2 amps (or 1 amp if external
DHW pump is used).
Connect pump to line voltage terminal strip CH
B.
PUMP L,N,G.
Domestic Hot Water Pump, if used.
•
Isolate pump from control module if pump FLA
A.
exceeds 1.0 amp.
Connect pump to line voltage terminal strip DHW
B.
PUMP L,N,G.
8.4 External Connections
(Figure 8-3)
User Interface Terminals
•
Factory wired to USER INTERFACE terminals
A.
Optional - Remote mount user interface for
B.
improved access. Use low voltage knockout.
Maximum wire length is 100 ft (30m) for 22 ga.
C.
wire, or 150 ft (45m) for 18 ga. wire.
WARNING
Electrical shock hazard. Turn OFF electrical power
supply at service panel before making electrical
connections. Failure to do so could result in death
or serious injury.
!
8 - ELECTRICAL CONNECTIONS
8-2 LINE VOLTAGE CONNECTIONS
NOTICE
Wiring diagrams can be found in Section 14 of this
Manual
.
8-1 ELECTRIC KNOCKOUTS BOTTOM OF BOILER
4½"
(1.4m)
5"
(1.6m)
High Voltage
Knockouts
Low Voltage
Knockouts
(Use supplied
grommets when using
these knockouts)
Front of Boiler
Back of Boiler
Summary of Contents for SSC Olsen OLSSC-050
Page 46: ...46 13 TROUBLE SHOOTING ...
Page 53: ...53 14 WIRING DIAGRAM 14 1 Connection Diagram ...
Page 54: ...54 14 WIRING DIAGRAM 14 2 Schematic Diagram of Ladder Form ...
Page 71: ...71 Date Service Performed Company Name Tech Initials Company Address Phone ...
Page 72: ...ECR International Inc 2201 Dwyer Avenue Utica NY 13504 4729 web site www ecrinternational com ...