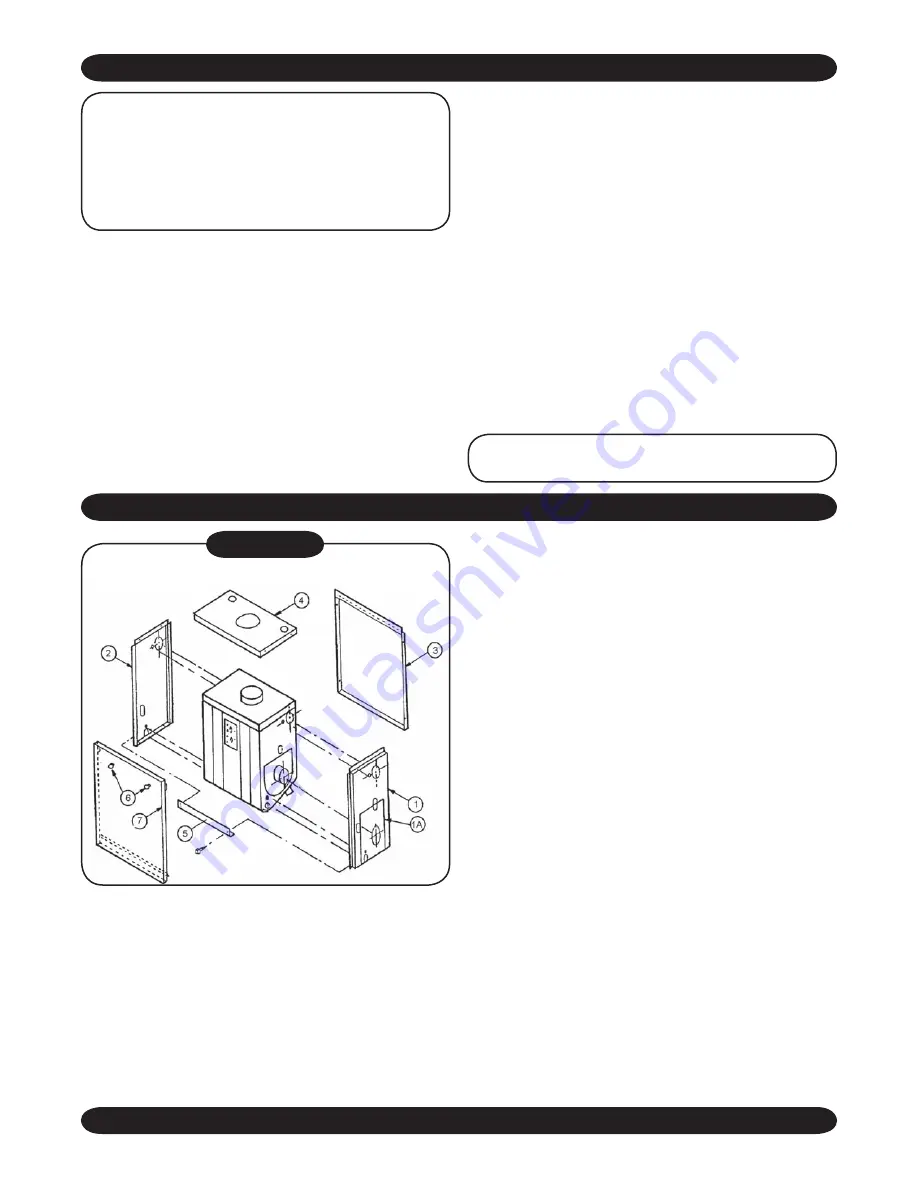
13
LOCATING THE BOILER
1. Place boiler at a location as centralized to the
piping system and as close to the chimney or vent
terminal as possible to minimize condensation.
At input rates up to 1.75 gph (245,000 Btu/hr),
the supply and return from radiation may be
piped on the same end of the boiler. At higher
rates, it is recommended that the supply be
piped from the rear of the boiler and the return
be piped from the front of the boiler. Coordinate
jacket installation with piping.
See
“Jacket
Assembly Instructions”
and
“Piping Diagrams”
in this manual for more information.
2. See
Figure #4
for installation on combustible
flooring. If necessary, place metal shims beneath
feet to ensure a level unit.
3. Accessibility clearances must take precedence
over fire protection clearances. Allow at least
24” for servicing at the tankless and burner
sides of the unit. Allow at least 18” at a side
where passage is required for access to
another side for servicing. A 6” clearance from
combustible material on all sides and the top
is recommended. 18” clearance is necessary
between smoke pipe and nearest combustible
material. See NFPA 31, latest revision, for safe
methods to reduce clearances where necessary.
NFPA publications are available at Battery Park,
Quincy, MA 02269.
CONSULT FIRE AUTHORITIES
FOR LOCAL REQUIREMENTS
JACKET ASSEMBLY
(Indoor Boilers)
JACKET ASSEMBLY
(INDOOR BOILERS)
1. See
Figure #5
(above) for reference. Note that
all sheet metal screws are #10 unless specified
otherwise.
2. See hardware package in boiler accessory kit for
stand-off bolts, studs, acorn nuts, washers, and
⅛” pipe plug. Note that the sight glass assembly
is also found in the boiler accessory kit.
3. Screw double end stand-off bolts into castings
next to upper supply and lower return tappings
in both ends of the boiler. Screw three
5
/
16
” studs
finger-tight into burner mounting.
4. Hold panels 1 and 1A against burner end of
boiler and insert necessary piping through
jacket openings into boiler casting.
5. Screw acorn nuts onto stand-off bolts.
6. Screw 1” nipple and sight glass holder into hole
above burner.
7. Screw the ⅛” plug into tapping on upper left of
burner mounting.
8. Install panel 2 on opposite side of boiler in same
manner as panel 1.
9. Install panel 3 by attaching it with four sheet
metal screws to panels 1 and 2 (already in
position).
10. Install temperature/pressure gauge into either of
the two ¾” tappings on top of the casting. Using
a ¾” x 4½” nipple, install relief valve in second
top tapping. Install jacket top panel (#4) by
attaching it with four sheet metal screws to the
three jacket side panels already in position.
To permit easy disassembly of overflow pipe in
order to raise jacket top panel for annual cleaning,
screw hand tight a ¾” nipple into the relief valve.
Attach a ¾” elbow to the nipple and an overflow
NOTE:
Please see the separate Venting
Instruction for flue size limitation and other
information on venting. For direct exhaust
systems, the total run of horizontal flue pipe
must not exceed 6’ and the total run of vertical
flue pipe must not exceed 10’.
Figure #5
Summary of Contents for ULTIMATE PF Series
Page 2: ......
Page 16: ...16 BURNER WIRING RIELLO BURNER WIRING...
Page 17: ...17 MULTI ZONE SYSTEM WIRING AND PIPING...
Page 18: ...18 MULTI ZONE SYSTEM WIRING AND PIPING...
Page 19: ...19 PIPING WITH CIRCULATORS MULTI ZONE SYSTEM WIRING AND PIPING...
Page 20: ...20 MULTI ZONE SYSTEM WIRING AND PIPING...
Page 38: ...38 BOILER PARTS...
Page 44: ......