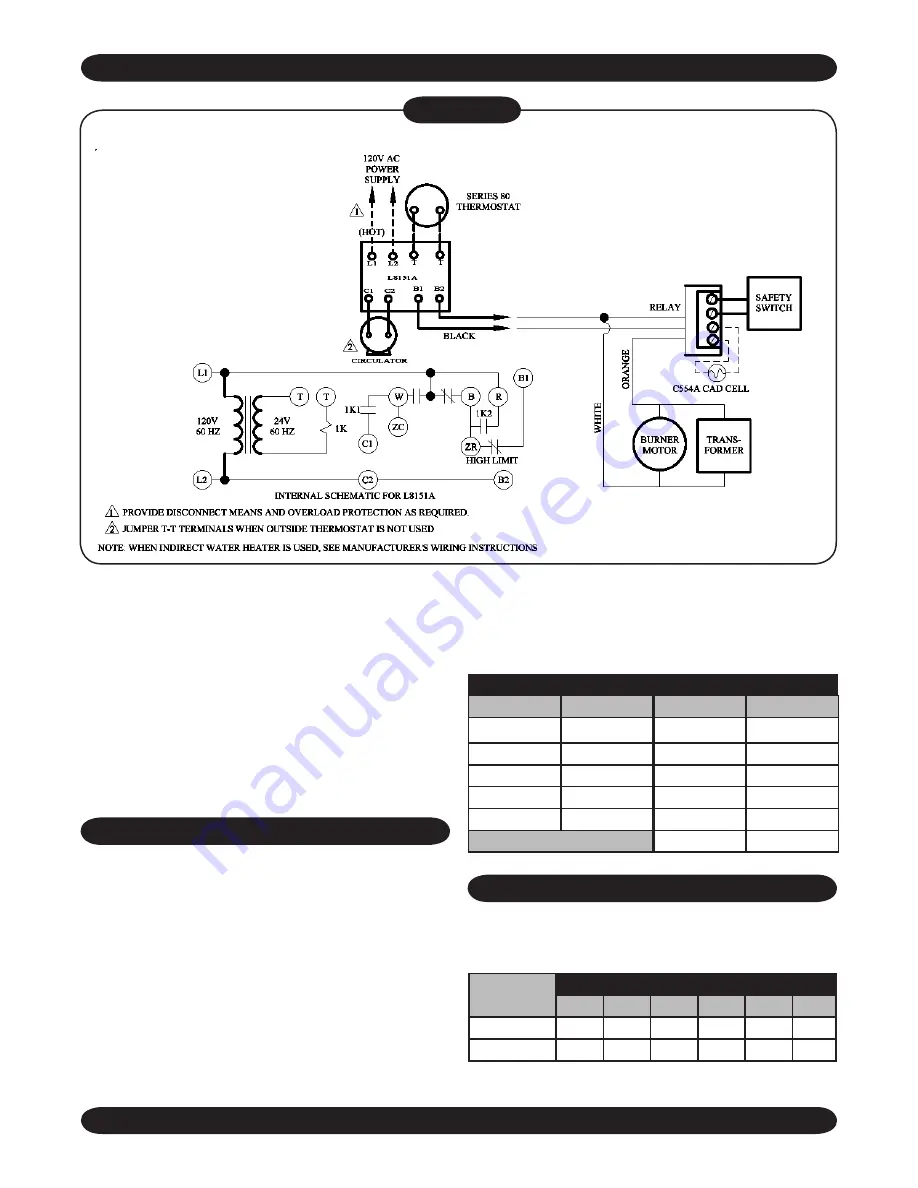
29
18. Referring again to
Figure #10
, fasten front jacket
panel (#9) in position with sheet metal screws and
install jacket top (#5).
19. Install exhaust assembly with parts 6, 7, and
8. The exhaust cap is made to spring inside the
short length of smoke pipe. A tourniquet made of
wire or a large hose clamp may be used to reduce
the diameter so that it will fit inside the pipe. Two or
three hose clamps in series may be used when a
large one is not available.
ANTIFREEZE
1. Antifreeze added to boilers must be non-toxic and
must be of a type specifically intended for use in closed
hydronic heating systems. Under no circumstances
should automotive antifreeze be used.
2. Use of antifreeze in any boiler may reduce capacity
by 10% or more and increase fuel consumption.
Tankless coil performance will fall as concentration
of antifreeze is increased.
3. Because antifreeze forms slush rather than hard
ice, it is safe to protect only to 10 degrees above
coldest temperature anticipated provided slush
formed can move towards expansion tank.
WATERPROOF (OUTDOOR) BOILER ASSEMBLY AND PIPING
BECKETT BURNER WIRING DIAGRAM FOR WEATHERPROOF OIL-FIRED BOILER
(SPACE HEATING)
Figure #11
PIPE
MATERIAL
PIPE SIZE
½”
¾”
1”
1¼”
1½”
2”
COPPER
82.5
40.0
23.3
15.3
10.8
6.2
STEEL
63.5
36.0
22.2
12.8
9.5
5.8
WATER VOLUMES OF PF SERIES BOILERS
MODEL
VOL. (GAL.)
MODEL
VOL. (GAL.)
PF3
7
PF3T
10
PF4
9
PF4T
12
PF5
11
PF5T
14
PF7
15
PF6T
16
PF9
19
PF8T
20
PF7TT
21
PIPING VOLUMES
Divide total length of piping in feet by factor (below)
to determine water volume in gallons.
Summary of Contents for ULTIMATE PF Series
Page 2: ......
Page 16: ...16 BURNER WIRING RIELLO BURNER WIRING...
Page 17: ...17 MULTI ZONE SYSTEM WIRING AND PIPING...
Page 18: ...18 MULTI ZONE SYSTEM WIRING AND PIPING...
Page 19: ...19 PIPING WITH CIRCULATORS MULTI ZONE SYSTEM WIRING AND PIPING...
Page 20: ...20 MULTI ZONE SYSTEM WIRING AND PIPING...
Page 38: ...38 BOILER PARTS...
Page 44: ......