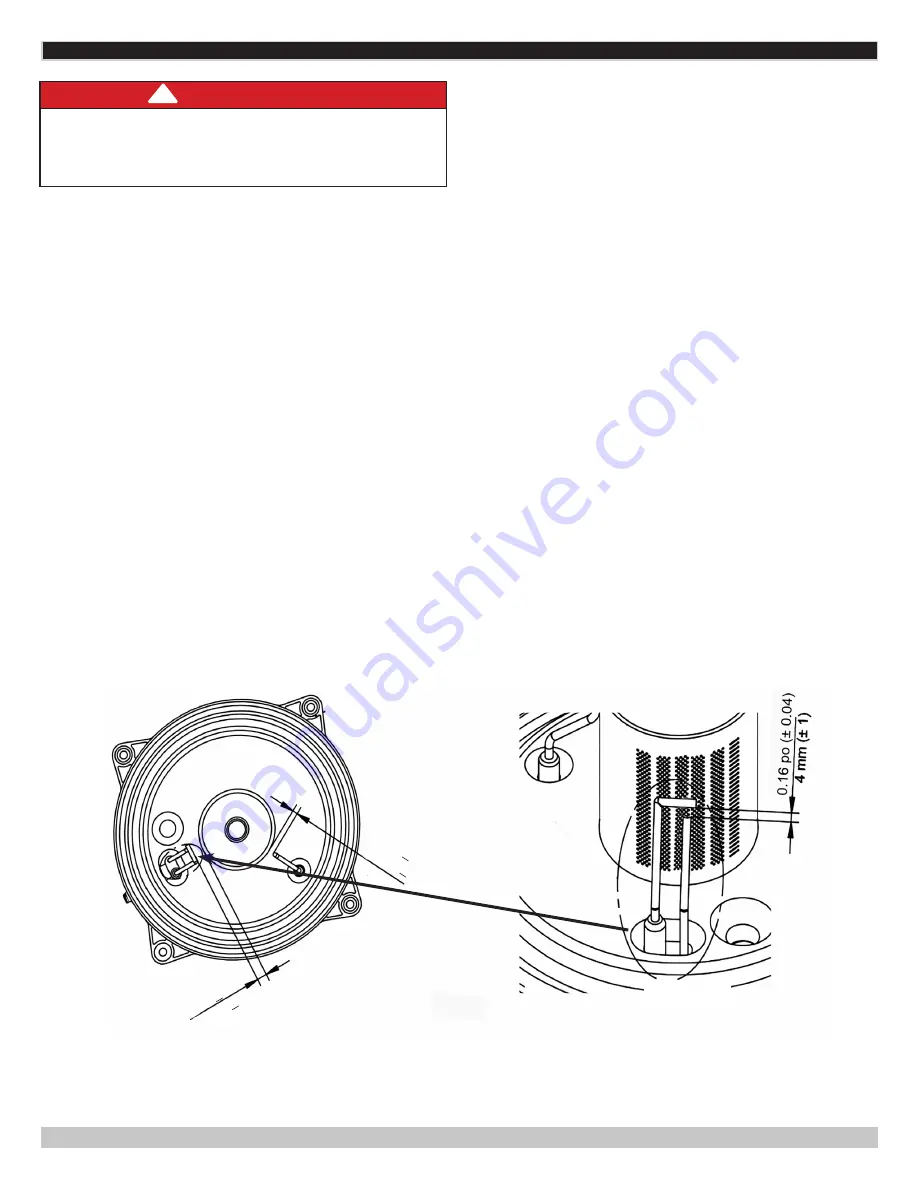
81
11.3 Component Replacement And Cleaning
1.
Remove any deposits from heat exchanger using suitable
soft brush.
Do not
use brush with metallic bristles.
2.
Check the condition of the combustion chamber insulation
panels. Any damaged panels must be replaced.
3.
Check the condition of the burner on the manifold,
carefully clean it with a soft brush if necessary.
Do not
use a brush with metallic bristles this might damage the
burner.
4.
Remove any fallen deposits from bottom of inner case.
5.
Clean the burner with soft brush and check the flame
ports are clear. Blockages may be removed with stiffer
brush or air compressor.
6.
Check the condition of the electrodes.
7.
Check the spark gap, positioning and height of electrodes.
See Figure 11-1.
8.
Check the fan impeller is clean and free to rotate.
9.
Replace used gaskets with new gaskets. See Parts list for
correct gasket kit number.
Figure - 11-1 Electrodes
11 - GENERAL MAINTENANCE AND CLEANING
DANGER
Before servicing, turn off electrical power to boiler at
service switch. Close manual gas valve to turn gas
supply OFF to boiler. Failure to comply will result in
death or serious injury.
!
11.4 Draining the Boiler
•
turn boiler off
• isolate electrical supply
• close boiler gas service cock
• allow boiler to cool
• drain boiler through onboard drain if available or
external drain valve.
11.5 Draining the Heating Circuit
• Follow all steps in Section 11.4.
•
Close central heating flow and return valves.
• Connect suitable pipe or hose to drain valve.
• Route it to suitable container or plumbing drain.
• Open drain tap.
0.20po (
+ 0.0
4)
5 m
m (
+1)
0.39po (
+ 0
.04)
10 m
m (
+1)
PN 240012363 REV. A [08/31/2018]