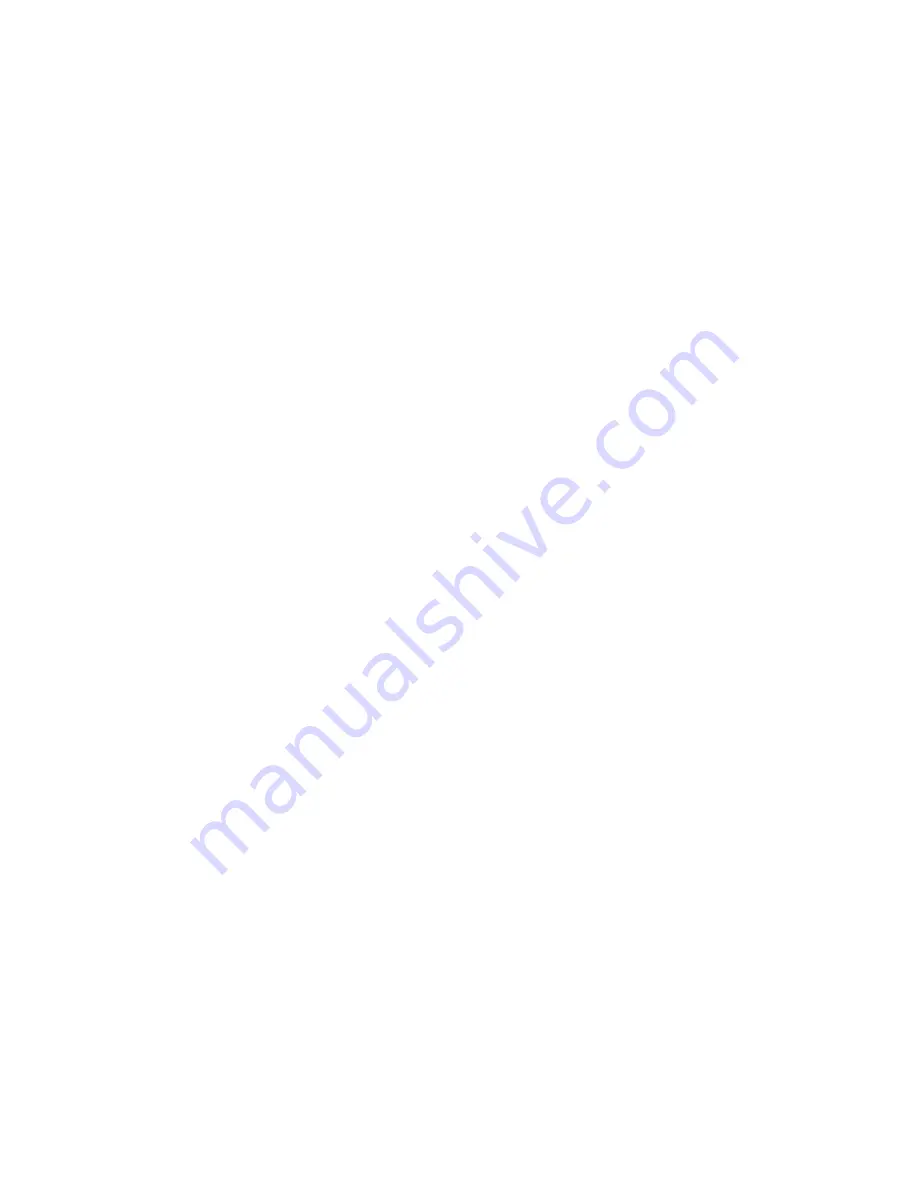
9
All mechanical seal types used in Eco Gearchem pumps consist of a rotating seal head
fixed to the shaft with set screws and a stationary seal face (or faces in the case of
double seals) mounted in the seal housing with a TFE O-ring gasket.
4. Mechanical Seal Maintenance
For proper seal functioning, the following conditions must be met:
A. The seal faces must be smooth, free of cracks, chips, or ridges and free of score
marks particularly those which emanate radially. Seal faces showing only light
scratches or marks may be re-lapped. Eco lapping standards are smooth and flat to 3
helium light bands. Avoid touching sealing faces.
B. The seal faces must be perpendicular to the shaft axis and run true. A bent shaft can
prevent proper sealing.
C. Secondary sealing elements such as O-rings and Teflon® wedges must be installed
so as not to pinch, cut or damage them. The use of a "bullet" to introduce the seal
head onto the shaft helps prevent damage Also the use of a lubricant that IS
compatible with the fluid being pumped is helpful.
D. The shaft must be free of nicks and scratches in the sealing area, particularly spiral
scratches When reinstalling a Type 9 seal head make sure the setscrews are
backed out so as not to damage the shaft when sliding the seal on.
E. Install the seal with the correct compressive contact. Dimensions and directions are
given for each model in the Reassembly Section.
F. A seal flush must be used for all double seal installations. The flush must be clean
and introduced at a pressure about 10 to 15 psi higher than discharge pump
pressure. For best results the flush inlet should be connected to the lower of the two
flush connections.
G. When reinstalling refurbished seal seats, always use a new seal seat O-ring. Slowly
heat TFE O-ring in water or other suitable solution until temperature reaches 160° -
175°F. Slip over seal set into position on O-ring groove and let cool. Do not use any
pointed or sharp-edged instruments that might cut or damage the O-ring during this
operation. New seal seats shipped from the factory include the O-ring already fitted to
the seat.
5. Stuffing Box Design
Eco Gearchem pumps with packing use either a plain stuffing box or one equipped with a
lantern ring. GH8, GA-12 and GA-16 packed pumps are supplied only in the later
configuration.
6. Stuffing Box Maintenance
Install packing rings carefully in the sequence noted on the drawings. Be sure gland is
clean and that shaft is not scored. New packing on a damaged shaft will not seal. Where
lantern rings are used, check to make sure they are properly positioned under the fitting
so that flush streams or lubricants will have access to the lantern ring.
Recommended lubricants are:
Service
•
Solvents
•
Acids/Alkalis
•
High temperatures
Lubricant
•
Soap-free grease
•
Fluorocarbon grease
•
Silicone/Carbon/Graphite
Summary of Contents for GA Series
Page 18: ...18 8 PUMP SPECIFICATION CHART...
Page 19: ...19 9 EXPLODED VIEW DRAWING G2 G4 SERIES...
Page 20: ...20 10 EXPLODED VIEW DRAWING G6 G8 SERIES...
Page 21: ...21 11 EXPLODED VIEW DRAWING GH8 SERIES...
Page 22: ...22 12 EXPLODED VIEW DRAWING GA12 GA16 SERIES...
Page 23: ...23 13 SEAL ARRANGEMENT DRAWINGS...
Page 24: ...24...
Page 25: ...25...
Page 26: ...26...
Page 27: ...27...
Page 29: ...29 15 GEARCHEM PUMP PRESSURES...
Page 30: ...30...
Page 32: ...32...
Page 33: ...33...
Page 35: ...35 15 PUMP PERFORMANCE CURVES...
Page 36: ...36...
Page 37: ...37...
Page 38: ...38...
Page 39: ...39...
Page 40: ...40...
Page 41: ...41...
Page 42: ...42...
Page 43: ...43...
Page 44: ...44...
Page 45: ...45...
Page 46: ...46...
Page 47: ...47...
Page 48: ...48...
Page 49: ...49...
Page 50: ...50...
Page 51: ...51...
Page 52: ...52...
Page 53: ...53...
Page 54: ...54...
Page 55: ...55...
Page 56: ...56...
Page 57: ...57...
Page 58: ...58...