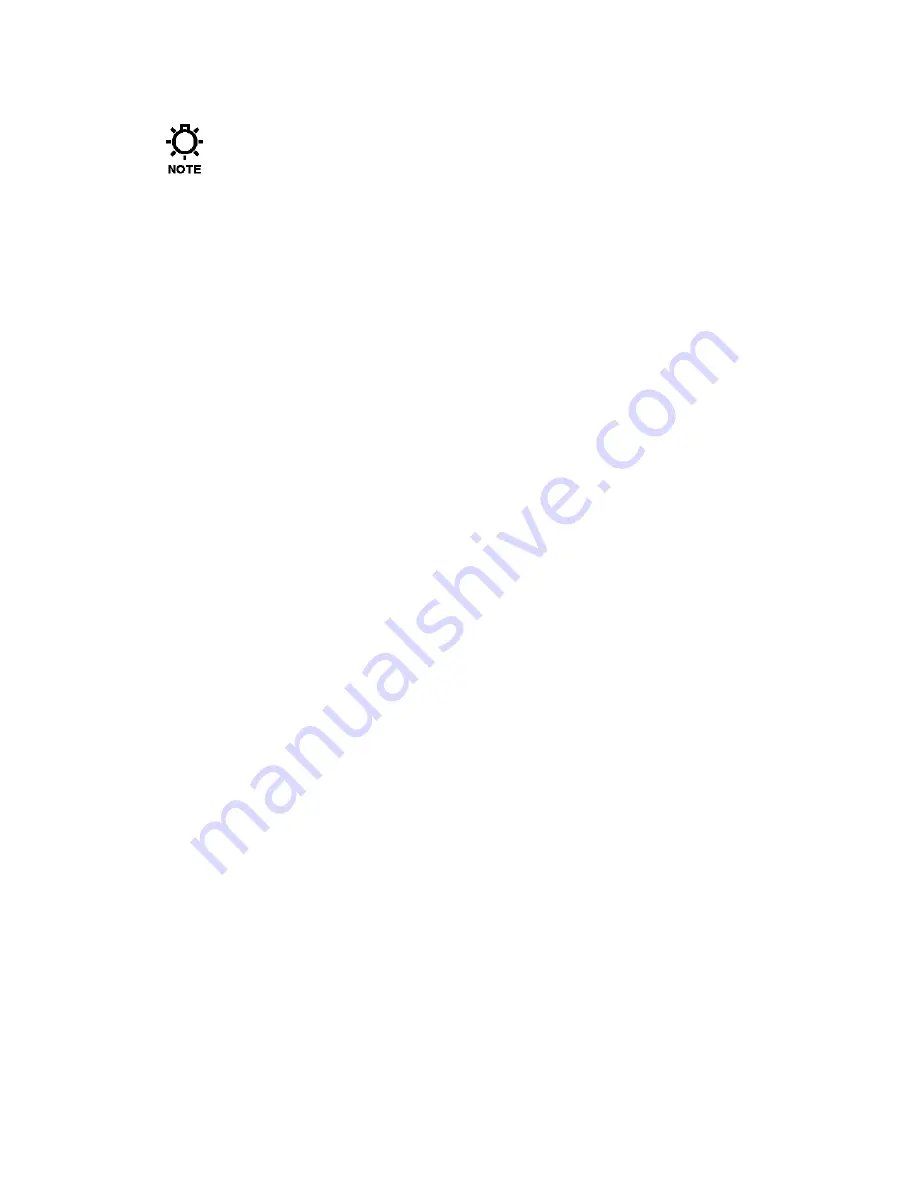
14
IT IS RECOMMENDED THAT SEAL BE TESTED AT THIS POINT BY PRESSURIZING
SEAL HOUSING WITH SUITABLE FLUID AT 10-15 PS1 ABOVE PUMP DISCHARGE
PRESSURE ROTATE SHAFT BY HAND AND OBSERVE FOR ANY LEAKAGE
ALONG THE SHAFT IN EITHER DIRECTION. IF LEAKAGE RATE IS SMALL
SOMETIMES A RUN IN PERIOD OF 5-20 MINUTES WILL CAUSE EVERYTHING TO
SEAT PROPERLY
F. Double Mechanical Seal (GH8, GA12, GA16)
Reference Drawing SD-2613, SD-2775
1. Before replacing seat, lightly lubricate seat ring. Then carefully align slot in seal seat
with pump end seat pin. Place protective material over polished seal seat surface and
press seal seat into front housing (Item 1).
2. Reassemble front housing to pump. Replacement of housing O-ring (Item 16) is
recommended. Install seal head on drive shaft (Item 4). Remove holding clips. Adjust
seal head so that contact is made with pump end seal seat. Assembly seat retainer
with drive end seal seat, previously installed and a seat retainer O-ring (Item 37).
Tighten seat retainer bolts (Item 39A) which will set proper compression on seal
head.
3. Tighten seal head set screws through port. Replace pipe plug (Item 62 or 63) and
previous piping for flushing of double seal.
4. Test seal installation before returning pump to service. Using flush connections in
front housing, pressurize the seal cavity in the front housing at 10-15 psi above pump
discharge pressure. To be sure components are seated properly, rotate shaft by
hand several times. Remove front drive bearing flush plug to observe pump end of
shaft. Observe shaft and gland at coupling end. There should be zero leakage from
either end.
5.4 BOLT-ON THERMAL JACKETS INSTALLATION
The following tools are required:
•
Suitable wrenches (open end socket or adjustable) to bolt jacket halves together with
1/4", 3/8", or 1/2." Bolts provided with jacket.
•
Heat transfer cement (Term on "standard grade:
” or equivalent) to fill any slight
clearance between the interior surface of the bolt-on jacket and the exterior surface
of the pump.
•
A suitable mason's trowel to apply heat transfer cement to the interior surface of the
jacket.
•
Damp paper towels or rags for clean-up.
1. Install Gearchem pump that is to be jacketed in the process line.
2. Visually inspect pump to be jacketed and remove any foreign material (debris,
packing lists, or identification tags) which might come between the inner jacket
surface and the pump.
PUMPS HAVING PAINTED SURFACES REQUIRE NO SPECIAL PREPARATION.
PAINT SHOULD BE DRY.
3. Check for proper fit of the bolt-on jacket halves by removing bolts which hold the
halves together, and place both halves around the pump. Normally there is a slight
clearance between the inner jacket surface and the pump.
4. Remove jacket halves from the pump and lay them on a clean, dry, work area, inner
surfaces face up.
5. With a trowel, coat the inner surfaces of the jacket halves with heat transfer cement.
Coating should be approximately 1/8" to 1/4" thick. Also dab a small quantity of the
cement on the back of the pump flanges in three or four places.
Summary of Contents for GA Series
Page 18: ...18 8 PUMP SPECIFICATION CHART...
Page 19: ...19 9 EXPLODED VIEW DRAWING G2 G4 SERIES...
Page 20: ...20 10 EXPLODED VIEW DRAWING G6 G8 SERIES...
Page 21: ...21 11 EXPLODED VIEW DRAWING GH8 SERIES...
Page 22: ...22 12 EXPLODED VIEW DRAWING GA12 GA16 SERIES...
Page 23: ...23 13 SEAL ARRANGEMENT DRAWINGS...
Page 24: ...24...
Page 25: ...25...
Page 26: ...26...
Page 27: ...27...
Page 29: ...29 15 GEARCHEM PUMP PRESSURES...
Page 30: ...30...
Page 32: ...32...
Page 33: ...33...
Page 35: ...35 15 PUMP PERFORMANCE CURVES...
Page 36: ...36...
Page 37: ...37...
Page 38: ...38...
Page 39: ...39...
Page 40: ...40...
Page 41: ...41...
Page 42: ...42...
Page 43: ...43...
Page 44: ...44...
Page 45: ...45...
Page 46: ...46...
Page 47: ...47...
Page 48: ...48...
Page 49: ...49...
Page 50: ...50...
Page 51: ...51...
Page 52: ...52...
Page 53: ...53...
Page 54: ...54...
Page 55: ...55...
Page 56: ...56...
Page 57: ...57...
Page 58: ...58...