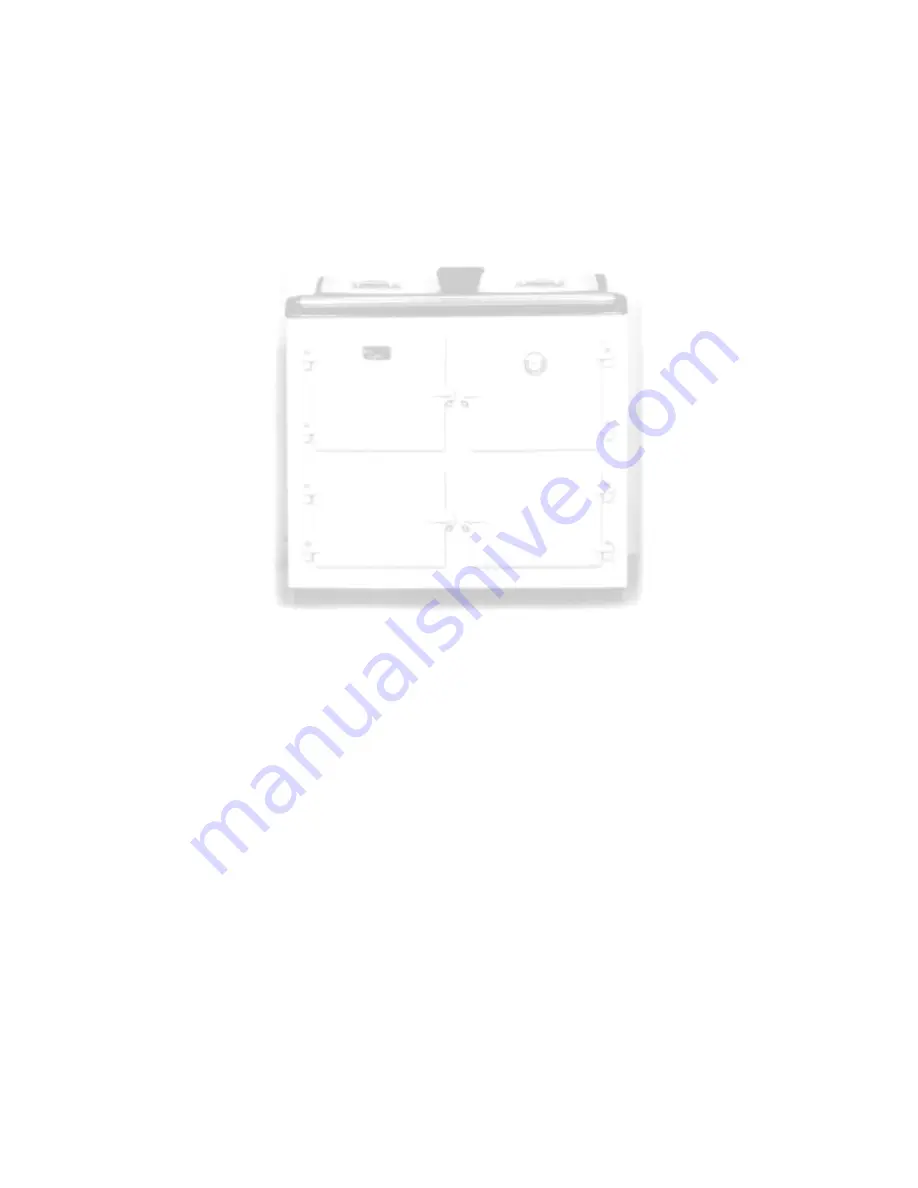
ECO RANGE
Cooker
Oil Condensing Boiler model
For use in Great Britain and Eire (GB & IE)
Instructions for Use, Installation and
Servicing
This appliance must be installed in accordance with the regulations in force and only used in
an adequately ventilated space. Please read these instructions before installation and use and
retain for future reference.
Summary of Contents for 15/21
Page 14: ...RECOMMENDED FLUE POSITION...
Page 15: ...OIL SUPPLY...