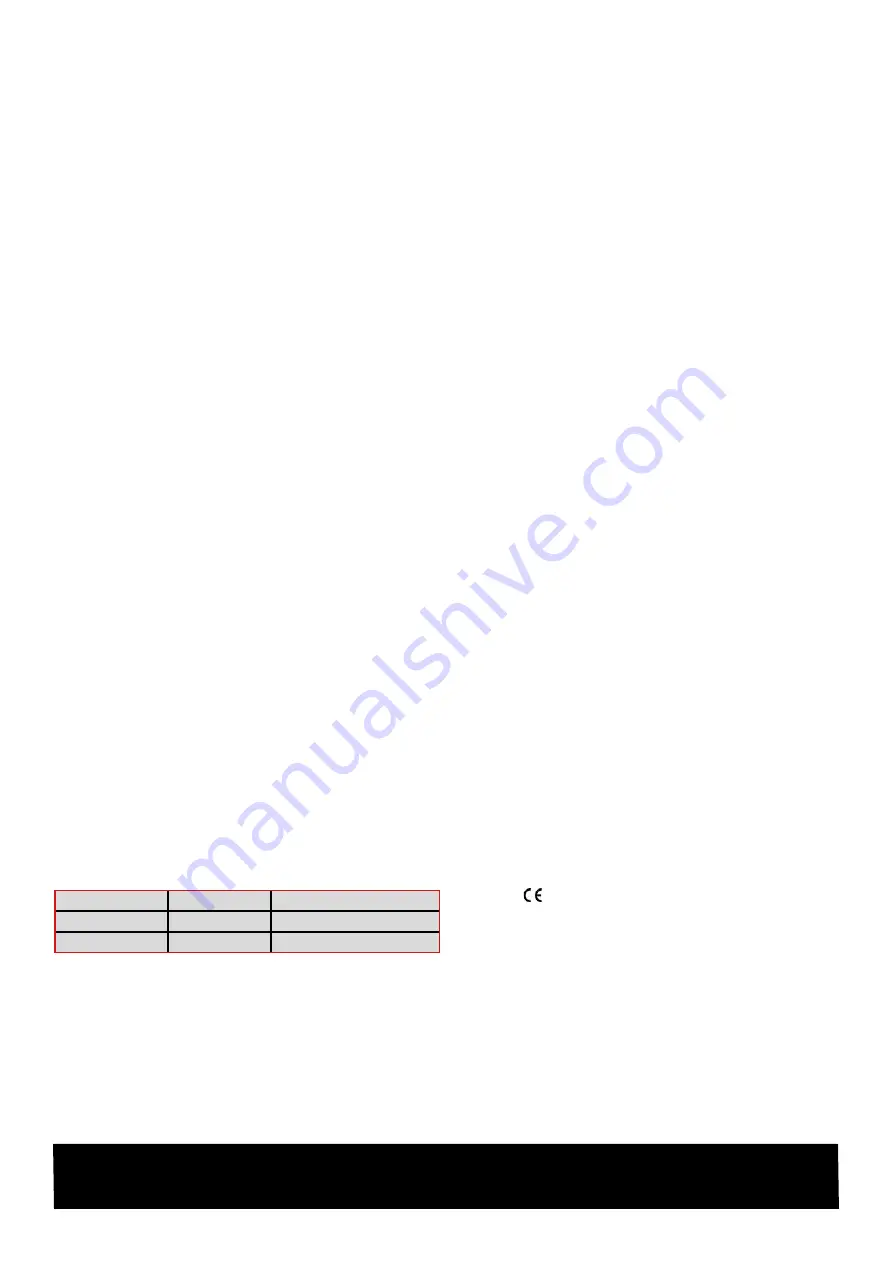
Testing
1. Functional test
Connect the main power cord of the pump. Manually fill the tank until
the float switch turns the pump on.
2. To test the overflow alarm circuit (only EE400M and EE300 only)
a) Kink the tube coming from the pump discharge so it cannot pump
out.
b) Pour water into the pump reservoir, filling it completely.
c) As the water level nears the top of the unit the overflow alarm
switch should activate.
d) Un-kink the tube and allow the pump to empty the tank. As the
water level goes down the overflow safety switch will deactivate
and the appliance will energise again (or the alarm will reset).
Maintenance
Warning! Before attempting any maintenance on the unit,
disconnect the power cord from the power supply to avoid the risk
of electrical shock.
Attention: The overflow alarm circuit (EE400M and EE300 only) can
still be under power.
If the pump does not perform as stated in above tests, remove the tank
cover of the pump (EE400M only). The drive unit can be removed
now. The EE150 and EE300 can be opened by inserting a screwdriver in
one of the side slots of the tank and levering it away (do not over-stress
the material). After that, unscrew the two Phillips screws located on top
(EE150 only). Now verify that the float mechanism moves up and down
freely. If the float binds, it may be dirty or damaged. The motor itself
does not need any maintenance so do not attempt any repairs. Also,
never open the drive unit of the EE400M because breaking the seal will
invalidate the warranty. However, the tank and float mechanism will need
to be cleaned once a year. The tank and the floats should be cleaned
with mild detergent using a damp cloth.
Reassemble the pump in reverse order.
Cleaning the check valve and verify its operating
1. After unscrewing the cap nut remove the discharge line from the
check valve
2. Use a SW 20 wrench to remove the check valve from the drive unit.
3. Visually check the valve for obstructions. If damaged, replace.
4. To re-install the check valve, hands tighten it to the drive unit.
Then, tighten 1/2-turn further with a wrench. Be careful not to
over-tighten as this may distort the O-ring seal under the check valve.
Replacement items
The discharge nipple with integrated check valve is available for
replacement. (see table)
model
Item-number
description
EE150 / EE400
M
22214
check valve
EE300
22213
check valve
Troubleshooting
If the pump does not function properly, refer to the following:
1. Unit does not run:
a) Check the power supply
b) Check the appliance to see if condensation is actually being
generated
c) Check to make sure the pump float mechanism moves freely and
clicks the activation switch when moved up and down.
(EE150+EE400M quiet click noise only due to construction
type of switch)
d) Check the drain line (s) into the pump for obstructions. Note:
If these lines are clogged and remain clogged, the appliance may
eventually be damaged.
2. Pump makes loud noise when running:
a) Check the tank for debris and clean if necessary. Refer to the
maintenance section for cleaning instructions.
3. Unit runs but does not pump liquid out:
a) Check the floats to be sure that they are not stuck in the up
position.
b) Check the height of the discharge tubing to be sure it does not
exceed the allowed head (see specifications)
c) Check the discharge tube for obstructions and clear if needed.
d) Check the check valve for obstructions. Refer to the maintenance
section for cleaning instructions.
4. Liquid drains back into pump from discharge line:
a) Check valve may have debris in it. Refer to the maintenance
section for cleaning instructions
b) If the discharge line is plumbed so the highest point is less
than 1 m above the pump, the check valve may allow liquid to drain
out of the line. This is normal and will not damage the pump.
5. Liquid leaks from around the check valve
a) Check the proper fit of the cap nut that holds the discharge
tube in place.
b) If the check valve is too tight or too loose it may leak around
the O-ring. Check that the valve is hand tight, and then tighten
an addition 1/2 turn with a wrench.
c) If the O-ring under the check valve is damaged, replace with a
new one or purchase a replacement check valve, which includes an
O-ring.
Warranty
1 year. This warranty covers all parts with material or manufacturing
faults. The buyer’s only remedy is the replacement or repair of the defec-
tive parts. In no case can labour costs and any consequential damage
be cited as a basis for a complaint. Any returned units must be complete
and must be accompanied by a written list of the defects ascertained.
We are unable to accept any liability in case of nonconforming in-
stallation or noncompliance with the specifications or maintenance
recommendations.
Conformity:
All data contained in these specifications are solely intended to describe
the product and do not constitute warranted characteristics in the legal
sense.
Subject to technical modifications.
- 5 -
GB